2025 Auteur: Howard Calhoun | [email protected]. Laatst gewijzigd: 2025-01-24 13:22
De productie van gasblokken is momenteel behoorlijk winstgevend. Het materiaal behoort tot de groep van cellenbeton. Dit betekent dat het meeste is gevuld met gasbellen, wat hun fysieke gewicht aanzienlijk vermindert. Tegelijkertijd hebben ze goede thermische isolatie-eigenschappen en sterkteparameters. Dankzij de genoemde kenmerken zijn gasblokken in korte tijd behoorlijk populair geworden.
Algemene informatie over gasblokken
Als we het hebben over wat cellenbeton of een gasblok is, dan is dit een steen van kunstmatige oorsprong, die wordt gekenmerkt door de aanwezigheid van een groot aantal microscopisch kleine poriën. Dit materiaal wordt ook vaak geautoclaveerd cellenbeton genoemd, wat een idee geeft van de technologie voor de productie van gasblokken.
Het is vermeldenswaard dat het bouwmateriaal ook een hoge energiebesparing heeft. Dit wordt verklaard door de aanwezigheid van dezelfde poreuze structuur. Een ander goed voordeel is het geringe gewicht van elk blok.
De productie van gasblokken is ook daardoor enorm populair gewordenhet is mogelijk om niet alleen scheidingswanden voor constructies te bouwen, maar ook dragende muren. Het zal niet mogelijk zijn om dergelijk cellenbeton te gebruiken in de industriebouw of bij de constructie van hoogbouw. Het belangrijkste toepassingsgebied is particuliere constructie. In dit geval is er nog een voordeel te onderscheiden, namelijk dat de blokken geen sterke druk uitoefenen op de ondergrond, aangezien ze nogal wat wegen. Dit helpt om aanzienlijke fondsen te besparen op de inrichting van de stichting.
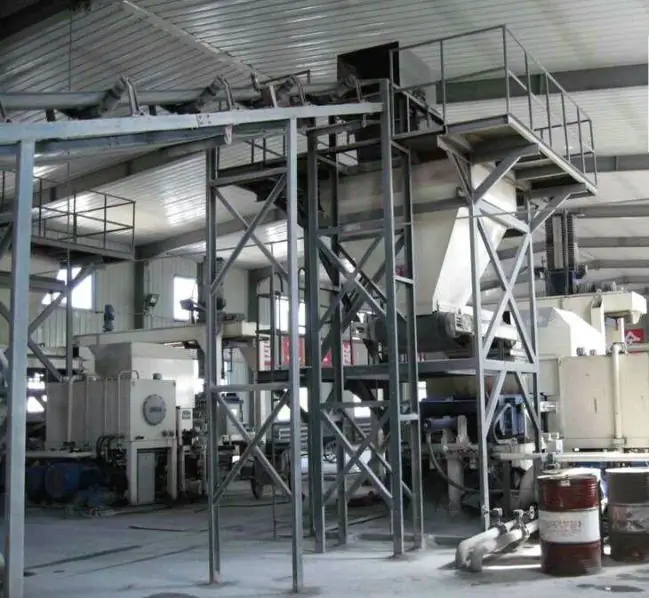
Cellenbetonmaterialen
Alle bovengenoemde voordelen zijn te danken aan de materialen die dienen als grondstof voor de productie van gasblokken. In feite zijn alle drie de componenten nodig voor de vervaardiging van het materiaal - dit zijn cement, kwartszand en een blaasmiddel, waarvan de rol wordt gespeeld door aluminiumpoeder. Hoewel kan worden gezegd dat sommige fabrikanten nog steeds extra elementen aan de samenstelling toevoegen, bijvoorbeeld kalk of as.
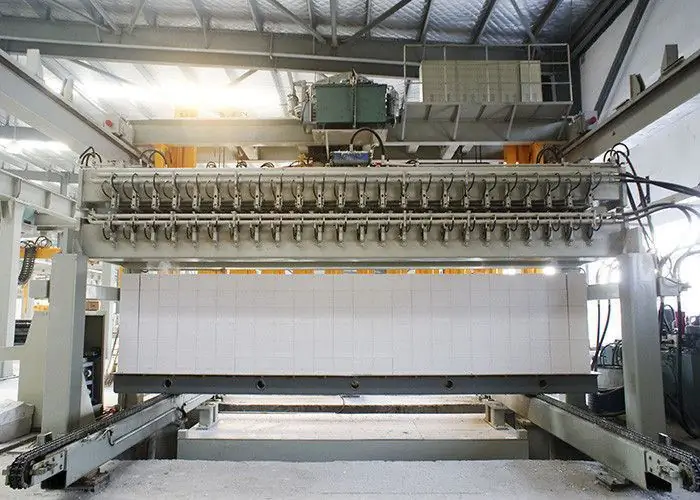
Cellenbetonproductie
De productie van gasblokken wordt uitgevoerd uit een groep droge materialen, die onder toevoeging van water met elkaar worden gemengd. Als laatste kunt u elk water van een technisch type gebruiken dat geschikt is volgens de vereisten van GOST 23732-79. Bij het toevoegen van vloeistof is het belangrijk om de temperatuur ervan te controleren. Als het heet genoeg is (45 graden Celsius), zal het de uitharding van het blok versnellen, waardoor de maximale veiligheidsfactor wordt verhoogd. Als het gaat om productie op industriële schaal,Dit zal ook de productiviteit helpen verhogen. Om deze redenen verwarmen bijna alle bedrijven met gasblokfabrieken water voordat ze het toevoegen aan droge ingrediënten. Een ander pluspunt van het gebruik van een verwarmde vloeistof is dat u de hoeveelheid cement kunt besparen, aangezien heet water de activiteit van droge grondstoffen sterker stimuleert.
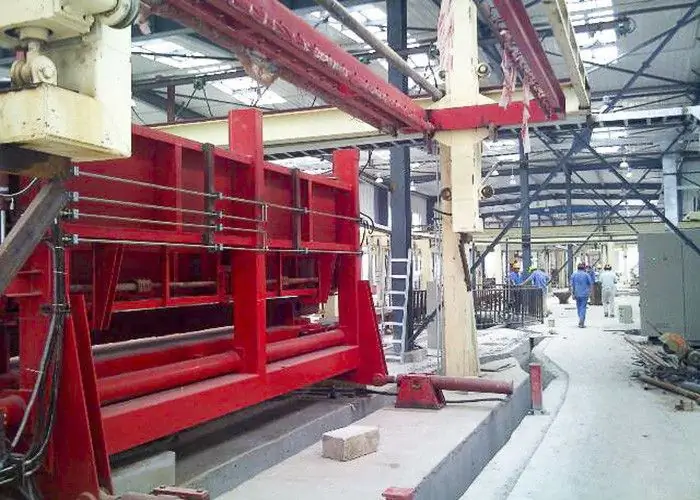
Selectie van zand voor productie
Mini-productie van gasblokken of industrieel vereist een zorgvuldige selectie van een ingrediënt als zand. Als we de kwestie vanuit een theoretisch oogpunt bekijken, kan zowel steengroeve- als rivierzand worden gebruikt. Er is één belangrijkste eis, namelijk dat deze grondstof een minimum aan slib- en kleiverontreinigingen moet hebben. De grootte van zandkorrels speelt ook een belangrijke rol - niet meer dan 2 mm.
Hier is het de moeite waard om de productie van een autoclaafgasblok te benadrukken, omdat bij de vervaardiging ervan zand kan worden vervangen door ingrediënten zoals slakken of as. Als u bijvoorbeeld as van thermische krachtcentrales gebruikt, wordt de dichtheid van het eindproduct verminderd, wat de productiekosten verlaagt.
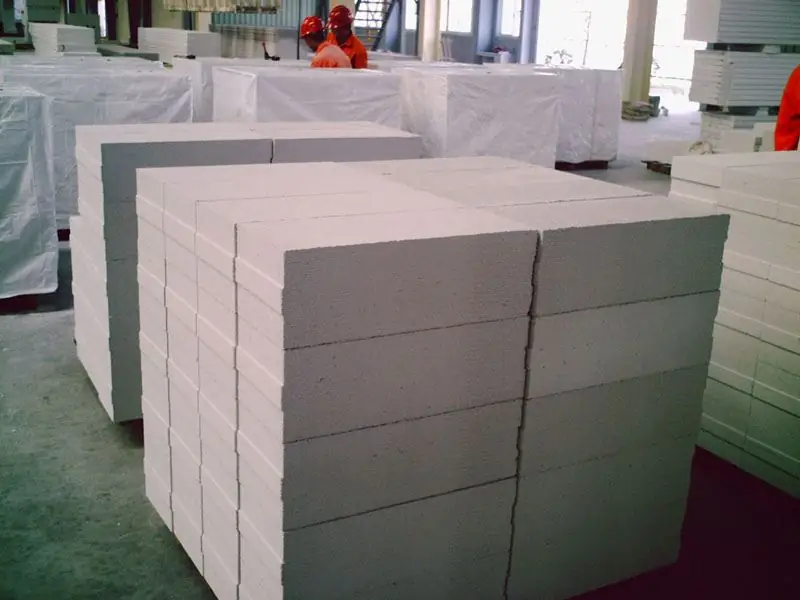
Cement en blaasmiddel
Om een kwaliteitsproduct te verkrijgen bij de productie van gasblokken, schuimblokken en ander cellenbeton, is het noodzakelijk om cementmerken zoals M400 of M500 te gebruiken. De beste optie zou zijn om de grondstof te kiezen die qua kenmerken volledig voldoet aan GOST 10178-85. Met betrekking totvergasser, dan wordt meestal aluminiumpoeder gekozen van het merk PAP-1 of het merk PAP-2. In zeldzame gevallen wordt als blaasmiddel geen poeder, maar een speciale pasta gekozen. Het is vermeldenswaard dat een suspensie ook kan worden gebruikt, omdat het niet altijd handig is om het poedervormige materiaal te kneden.
De essentie van de werking van het poeder is als volgt. Aluminium reageert met cement of kalkmortel, die de eigenschappen van alkali heeft. Tijdens dit proces worden elementen zoals calciumzouten (aluminaten) en gasvormige waterstof gevormd. Deze twee stoffen zullen de poriën vormen, waardoor de structuur overeenkomt.
Om een kwaliteitsproduct te creëren, is het erg belangrijk om de juiste verhoudingen van elk onderdeel te kiezen. Tot op heden zijn er algemene aanbevelingen voor de technologie voor de productie van gasbetonblokken: van 50 tot 70% cement van de totale massa, van 0,04 tot 0,09% van het aluminiummengsel, en ook van 20 tot 40% ruw zand materialen. Daarnaast is technisch water van 0,25 tot 0,8% en kalk van 1 tot 5% nodig. Met andere woorden, om bijvoorbeeld 1 kubieke meter van een product te krijgen, moet u beschikken over: 90 kg cement, water tot 300 liter, 375 kg zand en 35 kg kalk. De hoeveelheid aluminiumpoeder is slechts 0,5 kg.
Hoewel het belangrijk is om te begrijpen dat dit slechts algemene aanbevelingen voor de samenstelling zijn. Het aantal componenten kan al in productie worden aangepast, afhankelijk van het gewenste eindresultaat.
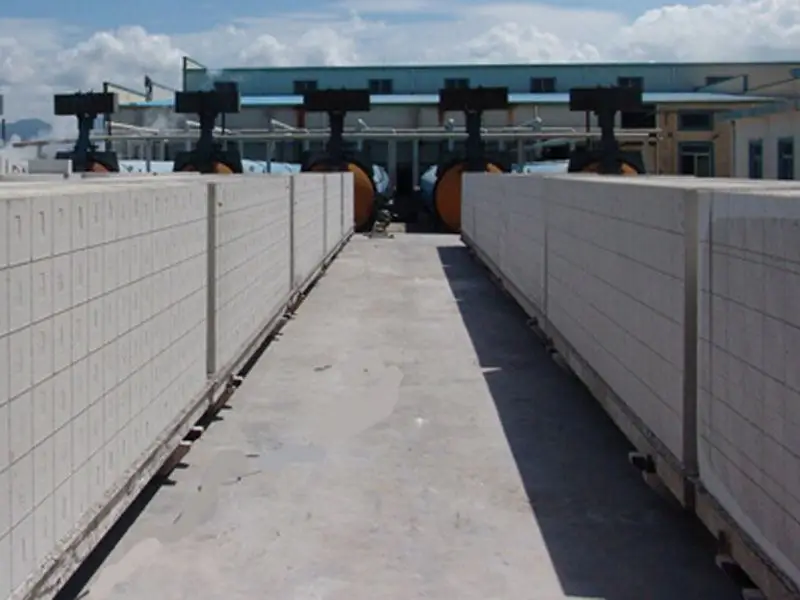
Wat heb je nodig voor productie?
Wat betreft de productietechnologie, hetsimpel genoeg. Desondanks werken thuismethoden of apparatuur hier niet. In dit geval moet u een speciale machine kopen voor de productie van gasblokken, als u cellenbeton voor uw eigen doeleinden wilt maken.
U moet echter begrijpen dat het niet mogelijk zal zijn om slechts één machine te kopen. De apparatuur is opgenomen in de productielijn van cellenbetonblokken in een complex. Dit is een soort minifabriekje. Wanneer u dergelijke apparatuur bij de fabrikant koopt, kunt u gebruikmaken van de diensten van een specialist die u zal helpen het technologische proces te begrijpen en in te stellen, u te vertellen hoe u de juiste componenten en hun hoeveelheid kiest.
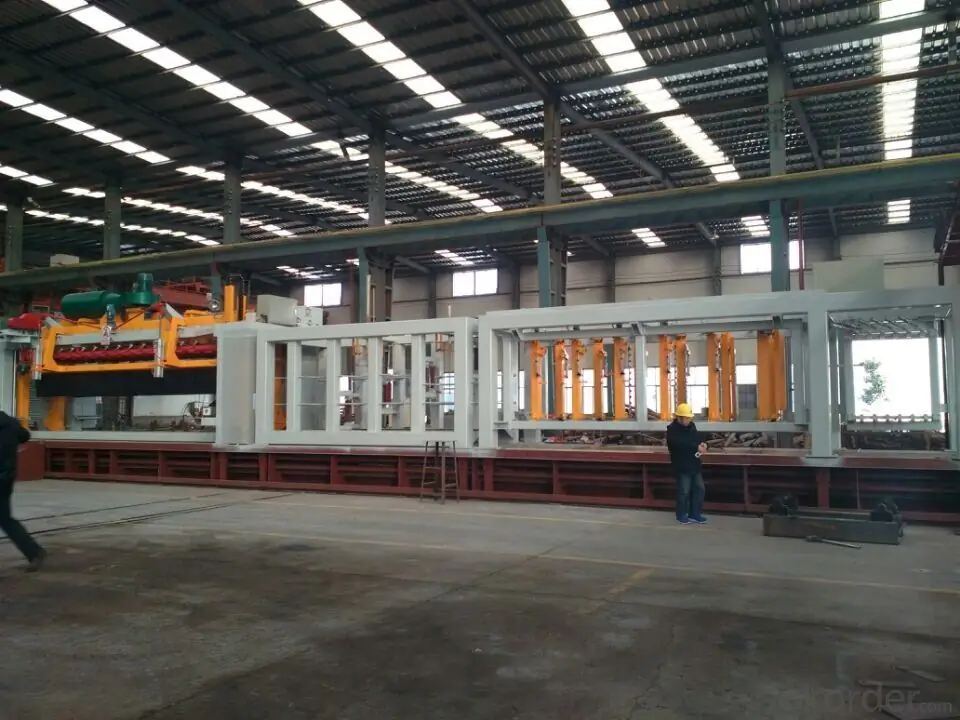
Verscheidenheden van apparatuur
Making armaturen zijn momenteel onderverdeeld in verschillende soorten. Het belangrijkste criterium voor het kiezen van een van hen is de vereiste productiviteit per dag. Het is ook erg belangrijk om te begrijpen hoeveel mensen zo'n rij zullen bedienen.
Het eerste type apparatuur is stationair. De dagelijkse productiviteit van een dergelijke lijn is 60 kubieke meter. Meestal wordt voor de plaatsing een magazijn of productiefaciliteit gebruikt, met een totale oppervlakte van minimaal 500 m22. Het belangrijkste kenmerk is dat de mallen naar een stationaire mixer gaan, waar ze worden gevuld met mortel. Daarna worden alle andere technologische productiestadia uitgevoerd. Er is slechts één extra werknemer nodig om de lijn met succes te laten werken.
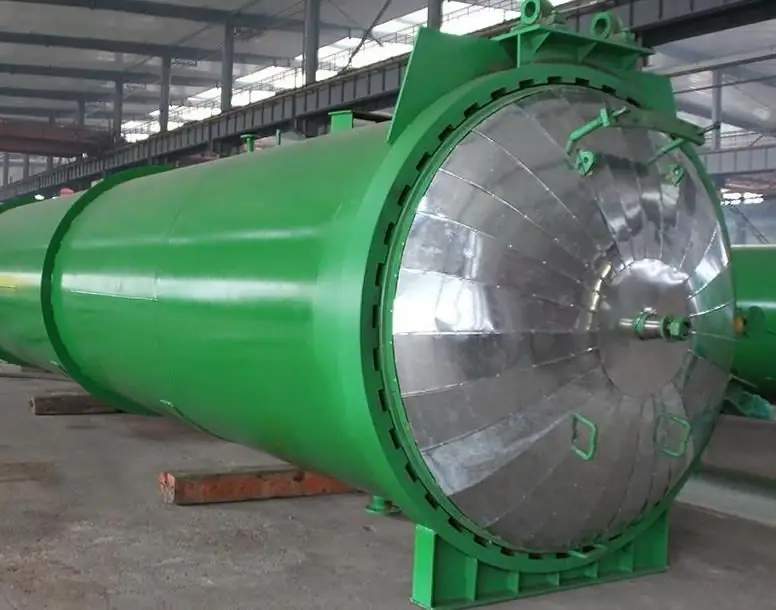
Transportbandapparatuur
Conveyorlijnen zijn uitgerust waar het nodig is om de productiviteit aanzienlijk te verhogen. Deze parameter van een dergelijk complex is 75-150 kubieke meter per dag. In dit geval is het productietempo hoger, alleen de duur van het stollen van de blokken verandert niet, omdat dit niet afhankelijk is van de lijn. Daarbij is echter veel meer ruimte nodig dan voor stationaire apparatuur. Daarnaast zijn er minimaal 8 mensen bij de dienstverlening betrokken, ondanks het feit dat de meeste procedures automatisch verlopen.
Kleine complexen
Wat betreft minilijnen voor productie, dit zijn de meest inefficiënte fabrieken, slechts 15 kubieke meter per dag. Ze verschillen van stationaire complexen doordat het niet de vorm is die hier naar voren komt, maar de mixer. Dit reduceert de benodigde ruimte aanzienlijk tot 140-160 m2. Meestal worden ze gekocht als startersoptie voor een productielijn voor gasblokken.
Er is nog een ander type, dat mobiele installaties wordt genoemd. Ze worden alleen gebruikt tijdens particuliere bouw. Het is vermeldenswaard dat dergelijke installaties volgens de berekeningen van specialisten vrij snel de moeite waard zijn. Bovendien helpen ze de bouwkosten met ongeveer 30% te besparen. De eigenaardigheid van mobiele units is dat ze worden geleverd met een compressor en dat ze zelfs kunnen werken wanneer ze zijn aangesloten op een normaal elektriciteitsnet thuis.
Productiestappen
Het is hier belangrijk op te merken dat cellenbeton kan worden geautoclaveerd en niet-geautoclaveerd. Het verschil is datde tweede optie is goedkoper, maar de sterkte-eigenschappen zijn ook minder. Vanwege het feit dat de productiekosten veel lager zijn, is het echter enorm populair. Om deze reden is het de moeite waard om de stadia van materiaalproductie te overwegen.
- De eerste fase is natuurlijk de selectie van alle benodigde componenten in hun exacte dosering. Daarna moeten ze grondig worden gemengd om een oplossing te verkrijgen. Als u over de apparatuur beschikt, duurt deze procedure niet langer dan 10 minuten.
- De tweede fase is dat de eerder bereide oplossing in speciale vormen moet worden geplaatst. Hiervoor wordt de juiste apparatuur gebruikt. Het is de moeite waard om te weten dat je de vorm maar voor de helft hoeft te vullen, omdat het mengsel na verloop van tijd zal toenemen door de vorming van gasbellen. Wat de tijd betreft, het proces duurt 4 uur, waarin het mengsel de vorm meestal volledig vult. Het komt ook voor dat er niet genoeg ruimte is. In dit geval moet het overtollige materiaal 2 uur na het laden worden verwijderd.
- De laatste fase is de belichting van het voltooide blok. Deze procedure duurt ongeveer 16 uur. Daarna kunt u zich bezighouden met het uit de vorm halen van het materiaal en het lossen op pallets. Vervolgens moet je ze op pallets laten staan, zodat ze de zogenaamde ontlaatsterkte krijgen. Na verloop van tijd duurt deze fase 2 tot 3 dagen. Na deze periode kunnen de blokken naar het magazijn worden gestuurd, maar ze kunnen alleen op de 28e dag worden verkocht, omdat pas tegen die tijd de sterkte het gewenste niveau zal bereiken.
Productie te koop
Aan het einde is het de moeite waard eraan toe te voegen dat de productiegasbetonblokken is een zeer winstgevende onderneming. Dit is duidelijk te zien na vergelijking van de kosten en de prijs. De kosten van 1 kubieke meter afgewerkte producten bedragen meestal 1800 roebel. Wat betreft de verkoopprijs voor 1 kubieke meter, deze kan 2500 roebel bereiken. Zoals u kunt zien, bereikt de nettowinst van slechts één kubieke meter 700 roebel.
Aanbevolen:
Wat is een technologieproject? Ontwikkeling van een technologisch project. Voorbeeld van een technologisch project
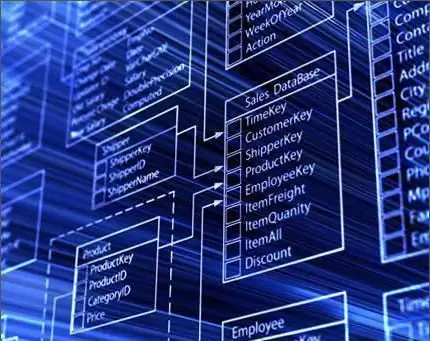
Als onderdeel van het artikel zullen we ontdekken wat een technologisch project is, en ook de problemen van de ontwikkeling ervan uitwerken
Inline-productie is Concept, definitie, organisatiemethoden en technologisch proces
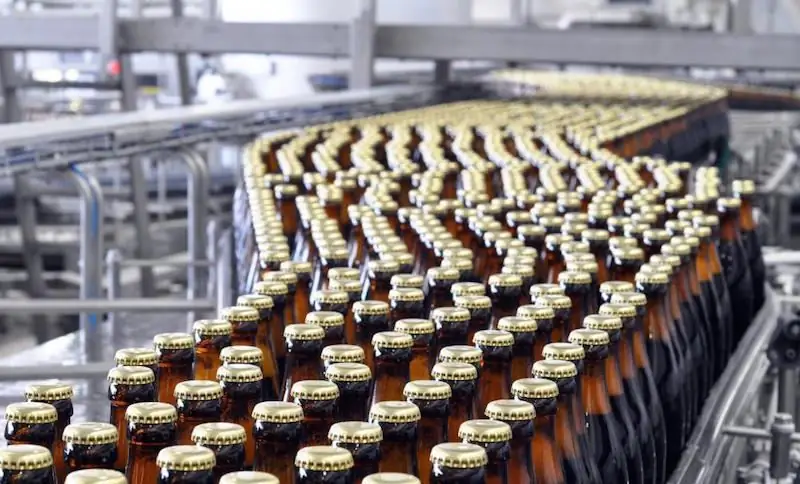
Het productieproces is een complexe technologische handeling die op verschillende manieren en middelen kan worden georganiseerd. Het werk van een onderneming in de omstandigheden van in-line productie van producten wordt tegenwoordig als het meest efficiënt beschouwd, maar tegelijkertijd veeleisend in termen van arbeids-, organisatorische en materiële kosten. In algemene zin is in-line productie een vorm van productieactiviteit waarin de principes van ritme en herhaalbaarheid van bewerkingen naar voren komen
Materialen vrijgegeven voor productie (posting). Boekhouding van de verwijdering van materialen. boekhoudkundige boekingen
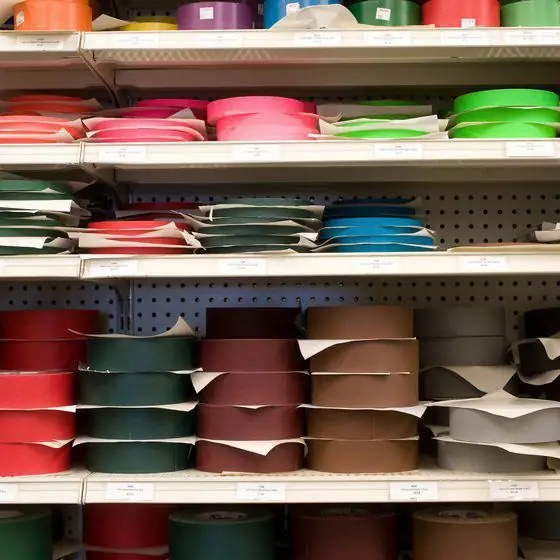
De meeste van alle bestaande ondernemingen kunnen niet zonder voorraden die worden gebruikt om producten te produceren, diensten te verlenen of werkzaamheden uit te voeren. Aangezien voorraden de meest liquide activa van de onderneming zijn, is hun correcte boekhouding uiterst belangrijk
Waar zijn munten van gemaakt: materialen en legeringen, technologisch proces
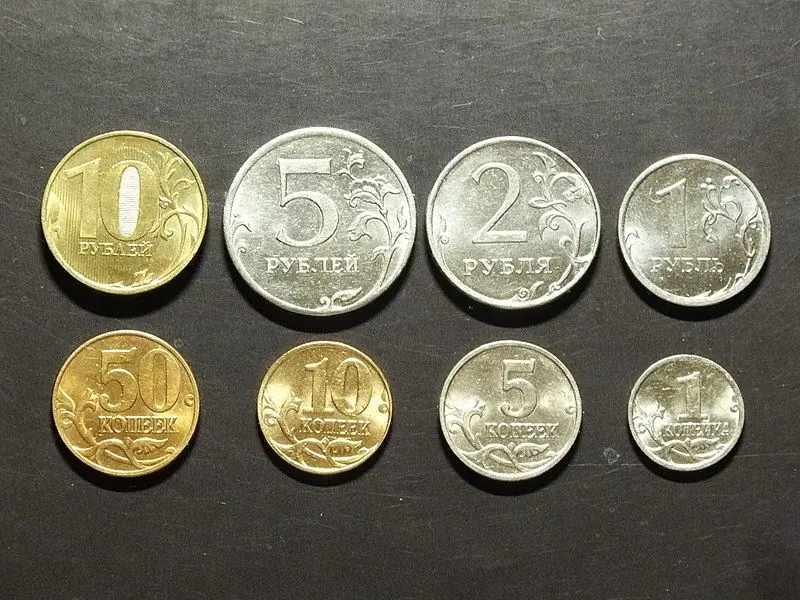
We hebben allemaal elke dag te maken met metaalgeld. Iedereen vindt munten in zijn portemonnee, zak, spaarvarken thuis op de plank. Mensen betalen met ijzergeld in winkels, bij koffieautomaten en op veel andere plaatsen. Maar niet veel mensen denken na over hoe lang het historische pad dat de munt heeft afgelegd om vandaag voor ons te verschijnen in de vorm waarin we gewend zijn hem te zien. Dit artikel belicht de belangrijkste mijlpalen in de ontwikkeling van ijzergeld, en je leert ook hoe en waar munten van worden gemaakt
Restauratie van onderdelen door lassen en verharden: methoden en methoden van restauratie, kenmerken, technologisch proces
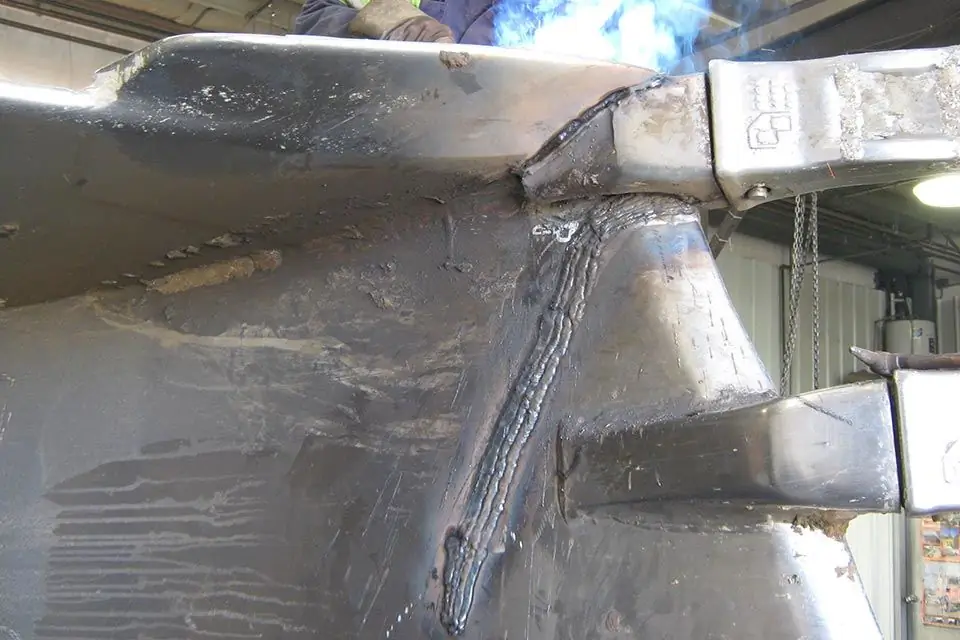
Las- en oppervlaktetechnologieën maken het mogelijk om metalen onderdelen effectief te herstellen, wat zorgt voor een hoge mate van betrouwbaarheid en duurzaamheid van het product. Dit wordt bevestigd door de praktijk om deze methoden te gebruiken bij het uitvoeren van reparatiewerkzaamheden op verschillende gebieden - van autoreparaties tot de productie van gewalst metaal. In de totale hoeveelheid werk aan de reparatie van metalen constructies, duurt het herstel van onderdelen door lassen en verharden ongeveer 60-70%