2025 Auteur: Howard Calhoun | [email protected]. Laatst gewijzigd: 2025-01-24 13:22
Het hoofd van elke onderneming, ongeacht het werkterrein, droomt dat de winst groeit en de productiekosten ongewijzigd blijven. Het "5S"-systeem in productie (in de Engelse versie 5S), dat alleen gebaseerd is op het rationele gebruik van interne reserves, helpt om dit resultaat te bereiken.
Dit systeem is niet helemaal opnieuw gemaakt. Iets soortgelijks werd aan het eind van de 19e eeuw voorgesteld door de Amerikaan Frederick Taylor. In Rusland werd dit gedaan door de wetenschapper, revolutionair, filosoof en ideoloog A. A. Bogdanov, die in 1911 een boek over de principes van wetenschappelijk management publiceerde. Op basis van de daarin uiteengezette bepalingen introduceerde de USSR de NOT, dat wil zeggen de wetenschappelijke organisatie van de arbeid. Maar het meest perfecte was het 5C-systeem dat werd voorgesteld door de Japanse ingenieur Taiichi Ohno en door hem werd geïntroduceerd in de Toyota Motor-fabriek in productie. Wat is het en waarom is het Japanse systeem zo populair geworden?
Feit is dat het gebaseerd is op een eenvoudig principe dat geen kosten met zich meebrengt. Het bestaat uitde volgende - elke medewerker, van de schoonmaker tot de directeur, moet zijn aandeel in de algehele workflow zoveel mogelijk optimaliseren. Dit leidt tot een verhoging van de winst van de productie als geheel en tot een verhoging van het inkomen van al haar werknemers. Nu is het stokje van de introductie van het "5C"-systeem overgenomen door bedrijven over de hele wereld, waaronder Rusland. In dit artikel zullen we proberen sceptici ervan te overtuigen dat Japanse knowhow echt werkt, en op elk gebied van activiteit.
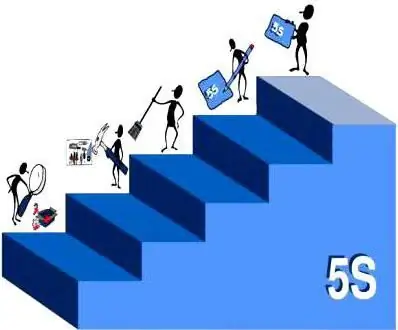
Het "5C"-systeem in productie, wat is het
International 5S staat voor vijf stappen ("step" in het Engels stap). Sommige economen en voorstanders van een nieuwe werkhouding verklaren de naam door de vijf Japanse postulaten die consequent in het 5S-systeem worden geïmplementeerd: seiri, seiton, seiso, seiketsu en shitsuke. Voor ons zijn onze native "5C's" dichterbij en begrijpelijker - vijf opeenvolgende stappen die moeten worden voltooid om de welvaart van onze productie te bereiken. Dit is:
1. Sorteren.
2. Orde bewaren.
3. Schoon houden.
4. Standaardisatie.
5. Verbetering.
Zoals je kunt zien, vereist het "5C"-systeem niets bovennatuurlijks bij de productie. Misschien is dat de reden waarom men nog steeds wantrouwen en een frivole houding jegens haar kan ontmoeten.
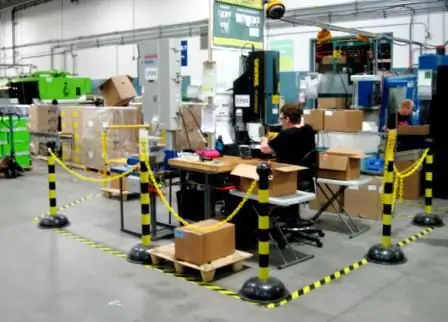
Stappen van het maken van een systeem
De wijze Japanner Taiichi Ohno, die, dankzij de introductie van zijn methoden in de Toyota-fabriek, uit deingenieur tot CEO, merkte op hoeveel verliezen er optreden als gevolg van verschillende inconsistenties en overlays. Zo werden er enkele kleine schroefjes niet op tijd op de transportband gezet, waardoor de hele productie stil kwam te liggen. Of andersom, de onderdelen werden met marge aangeleverd, bleken overbodig en als gevolg daarvan moest een van de medewerkers ze terugbrengen naar het magazijn, waardoor ze hun tijd verdoen met leeg werk. Taiichi Ohno ontwikkelde een concept dat hij "just in time" noemde. Dat wil zeggen dat er nu precies zoveel onderdelen als nodig op de transportband werden afgeleverd.
Andere voorbeelden kunnen worden gegeven. Het "5S"-systeem in productie omvatte ook het concept van "kanban", wat in het Japans "reclamebord" betekent. Taiichi Ohno stelde voor om aan elk onderdeel of elk gereedschap een zogenaamde "kanban"-tag te bevestigen, waarin alle benodigde informatie over het onderdeel of gereedschap werd gegeven. In principe geldt het voor alles. Bijvoorbeeld aan goederen, medicijnen, mappen op kantoor. Het derde concept waarop het 5S-systeem in productie is gebaseerd, is het concept van "kaizen", wat continue verbetering betekent. Er werden ook andere concepten bedacht, die alleen geschikt waren voor zeer gespecialiseerde productieprocessen. In dit artikel zullen we ze niet beschouwen. Als resultaat van alle in de praktijk geteste innovaties zijn er 5 stappen gevormd die toepasbaar zijn op elke productie. Laten we ze in detail analyseren.
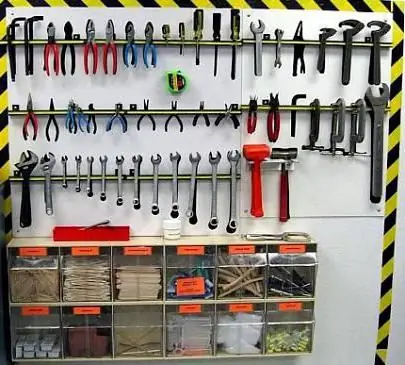
Sorteren
Velen van ons hebben items op onze desktops die, inin principe niet nodig. Bijvoorbeeld oude formulieren, ongebruikte dossiers, concepten van berekeningen, een servet waarop een kopje koffie stond. En tussen deze chaos kunnen zich de nodige bestanden of documenten bevinden. De basisprincipes van het "5S"-systeem zijn het optimaliseren van uw workflow, dat wil zeggen ervoor zorgen dat er geen tijd wordt verspild aan het zoeken naar de juiste dingen tussen het puin van het onnodige. Dit is sorteren. Dat wil zeggen, op de werkplek (in de buurt van de machine, op de tafel, in de werkplaats - overal), worden alle items op twee stapels gelegd - het noodzakelijke en het onnodige, dat moet worden weggegooid. Verder wordt alles wat je nodig hebt ontleed in de volgende stapels: "vaak en constant gebruikt", "zelden gebruikt", "bijna niet gebruikt". Hiermee is het sorteren voltooid.
Orde houden
Als je de items gewoon uit elkaar ha alt, heeft het geen zin. Het is noodzakelijk om deze zaken (gereedschappen, documenten) zo te ordenen dat wat constant en vaak wordt gebruikt in zicht is, of dat het snel kan worden meegenomen en gemakkelijk kan worden teruggezet. Wat zelden wordt gebruikt, kan ergens in een doos worden verzonden, maar er moet een kanban-tag aan worden bevestigd zodat deze na een tijdje gemakkelijk en nauwkeurig kan worden gevonden. Zoals je ziet begint het 5S systeem op de werkvloer met de simpelste stappen, maar blijkt in de praktijk zeer effectief te zijn. En bovendien verbetert het de stemming en het verlangen om te werken.
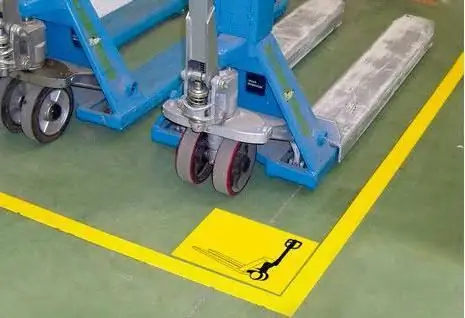
Schoon houden
Deze derde stap is voor velen de meest logische. Van kinds af aan wordt ons geleerd om rein te zijn. Op dein de productie is het ook nodig, en niet alleen de tafels van kantoorpersoneel of kasten in horeca, maar ook machines, bijkeukens van schoonmakers moeten schoon zijn. In Japan zorgen werknemers goed voor hun werkplekken, ze worden drie keer per dag schoongemaakt - 's ochtends voor het werk, tijdens de lunch en 's avonds, aan het einde van de werkdag. Bovendien hebben hun ondernemingen speciale markeringen van gebieden geïntroduceerd waarmee ze de volgorde in de productie kunnen observeren, dat wil zeggen dat gebieden met afgewerkte producten, opslag van bepaalde onderdelen, enzovoort zijn gemarkeerd met verschillende kleuren.
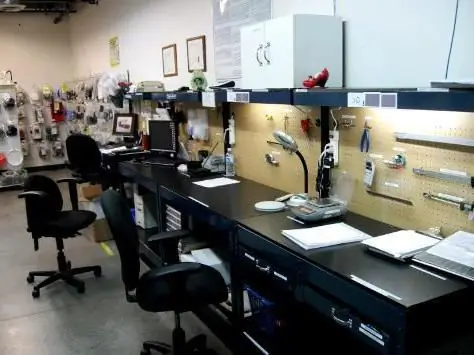
Standaardisatie
De principes van standaardisatie zijn uitgevonden door Taiichi Ohno. Ze worden ook veel gebruikt door het moderne 5S-systeem. Productiemanagement krijgt dankzij standaardisatie een prachtig instrument om alle processen te beheersen. Hierdoor worden de oorzaken van vertragingen uit de planning snel geëlimineerd en worden fouten gecorrigeerd die leiden tot het vrijgeven van producten van lage kwaliteit. In de fabriek van Toyota Motor zag de standaardisatie er als volgt uit: voormannen maakten dagelijkse werkplannen, nauwkeurige instructies werden op de werkplek opgehangen en aan het einde van de werkdag controleerden speciale arbeiders welke afwijkingen van het plan gedurende de dag waren opgetreden en waarom. Dit is de basisregel van standaardisatie, dat wil zeggen nauwkeurige instructies, werkplannen en controle over de uitvoering ervan. Nu voeren veel ondernemingen, bijvoorbeeld de ENSTO-fabrieken in Estland, een bonussysteem in voor werknemers die zich strikt houden aan de bepalingen van het 5C-systeem en op basis hiervan hun productiviteit verhogen, watis een grote stimulans om dit systeem als een manier van leven te gebruiken.
Verbetering
De vijfde stap, die het "5S"-systeem in productie voltooit, is gebaseerd op het concept van kaizen. Het betekent dat alle medewerkers, ongeacht hun functie, moeten streven naar verbetering van het werkproces op het gebied dat hen is toevertrouwd. De filosofische essentie van kaizen is dat ons hele leven elke dag beter wordt, en aangezien werk een deel van het leven is, moet het ook niet afzijdig blijven van verbeteringen.
Het werkterrein is hier breed, want perfectie kent geen grenzen. Volgens de opvattingen van de Japanners zouden arbeiders zelf hun productieproces moeten willen verbeteren, zonder instructies of dwang. Nu bouwen veel organisaties teams van werknemers op die de productkwaliteit bewaken, hun positieve ervaringen aan anderen overdragen en uitmuntendheid helpen bereiken.
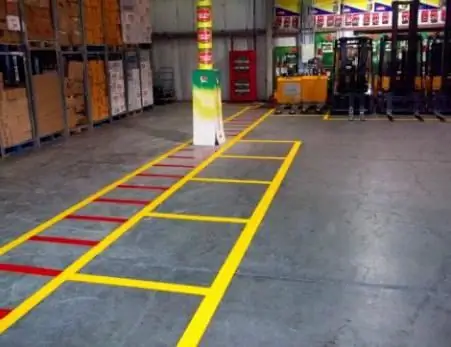
Basisfouten
Om het "5C"-systeem te laten werken, volstaat het niet om het te organiseren of werknemers in dienst te nemen die hun collega's zullen dwingen het te implementeren. Het is belangrijk dat mensen het nut van deze innovatie inzien en het als levensstijl accepteren. De introductie van het "5S"-systeem in Rusland in productie stuit op moeilijkheden, juist omdat onze Russische mentaliteit anders is dan de Japanse. Veel van onze producties worden gekenmerkt door het volgende:
1. Werknemers, vooral als er geen prikkels voor hen zijn, proberen niet de winst van de onderneming te vergroten. Ze vragen,waarom zou je de baas nog rijker maken als hij alles al heeft.
2. De leiders zelf zijn niet geïnteresseerd in de introductie van het "5S"-systeem, omdat ze er het nut niet van in zien.
3. Veel richtlijnen "van bovenaf" zijn gewend om alleen uit te voeren voor "tick". In Japan is er een heel andere houding ten opzichte van hun werk. Dezelfde Taiichi Ohno, die het "5S"-systeem introduceerde, dacht bijvoorbeeld niet aan persoonlijk gewin, maar aan het voordeel van het bedrijf waarin hij slechts ingenieur was.
4. Bij veel ondernemingen wordt het 5S-systeem gedwongen ingevoerd. Magere productie, wat inhoudt dat alle soorten verliezen (werktijd, grondstoffen, goede werknemers, motivatie en andere indicatoren) worden geëlimineerd, werkt niet, omdat werknemers zich op onbewust niveau beginnen te verzetten tegen innovaties, wat uiteindelijk alle inspanningen tot nul herleidt.
5. Managers die het systeem implementeren, begrijpen de essentie ervan niet volledig, wat storingen veroorzaakt in gevestigde productieprocessen.
6. Standaardisatie ontwikkelt zich vaak tot bureaucratie, een goede daad wordt overwoekerd met instructies en richtlijnen die het werk alleen maar hinderen.
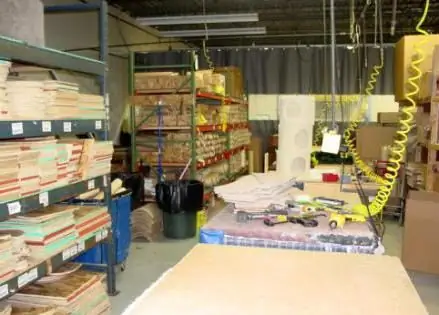
Beoordelingen
Russen die het "5S"-systeem in productie hebben geïntroduceerd, de feedback over deze innovatie is zeer dubbelzinnig. Uitgelichte voordelen:
- beter op de werkvloer;
- leid je werk niet af met onnodige kleine dingen;
- meer duidelijke workflow;
- vermoeidheid nam af aan het einde van de dienst;
- lichtjes verhoogdsalaris door verhoging van de arbeidsproductiviteit;
- beroepsblessures afgenomen.
Opgemerkte nadelen:
- bij het sorteren dwingen ze alles weg te gooien;
- standaardisatie heeft geleid tot een toename van bureaucratie;
- De introductie van het "5C"-systeem heeft de problemen in alle delen van de onderneming niet verergerd;
- Door het 5S-systeem op de eerste plaats te zetten, worden belangrijke problemen overschaduwd, zoals het gebrek aan reserveonderdelen.
Aanbevolen:
Mystery shopper: wat is het, kenmerken en principes van het beroep
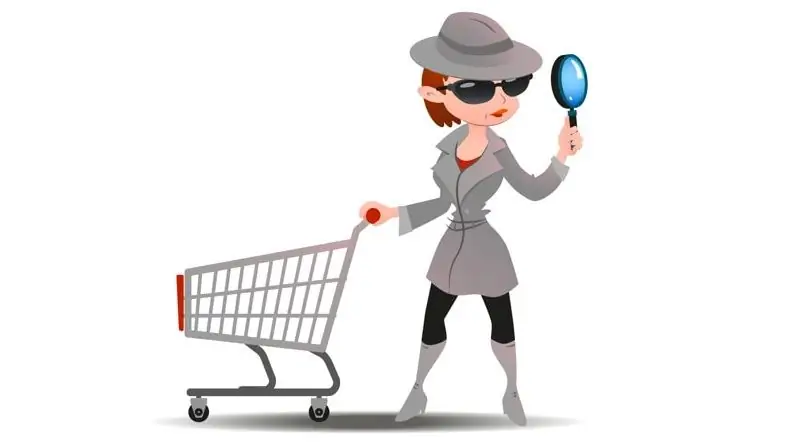
De "mystery shopper"-methode wordt veel gebruikt in westerse bedrijven, maar is recentelijk bekend geworden op de Russische markt. Bedenk wat voor soort beroep het is, waar je vacatures moet zoeken, aan welke kwaliteiten een sollicitant voor de plaats van een mystery shopper moet voldoen, en ook hoe de kwaliteit van het werk wordt beoordeeld en mogelijke fouten
Moderne productie. De structuur van de moderne productie. Problemen van moderne productie

Ontwikkelde industrie en een hoog niveau van de economie van het land zijn sleutelfactoren die de rijkdom en het welzijn van de mensen beïnvloeden. Zo'n staat heeft grote economische kansen en potentieel. Een belangrijk onderdeel van de economie van veel landen is de productie
Waar moet je op letten bij het huren van een appartement: regels voor het huren van een appartement, het opstellen van een contract, het controleren van meterstanden, beoordelingen
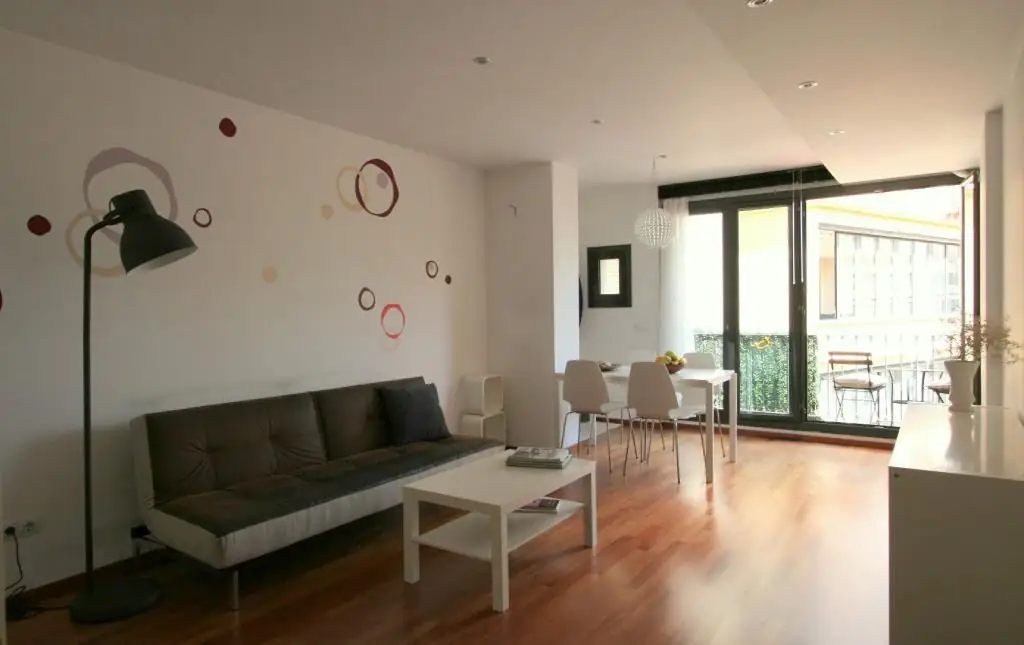
Ga je een appartement huren, maar ben je bang om opgelicht te worden? Uit dit artikel leer je hoe je een appartement correct huurt, hoe je een appartement kiest, waar je op moet letten bij het intrekken en de nuances van het opstellen van een huurovereenkomst
Tomaat "Lady's man": beoordelingen, beschrijving, kenmerken, kenmerken van de teelt
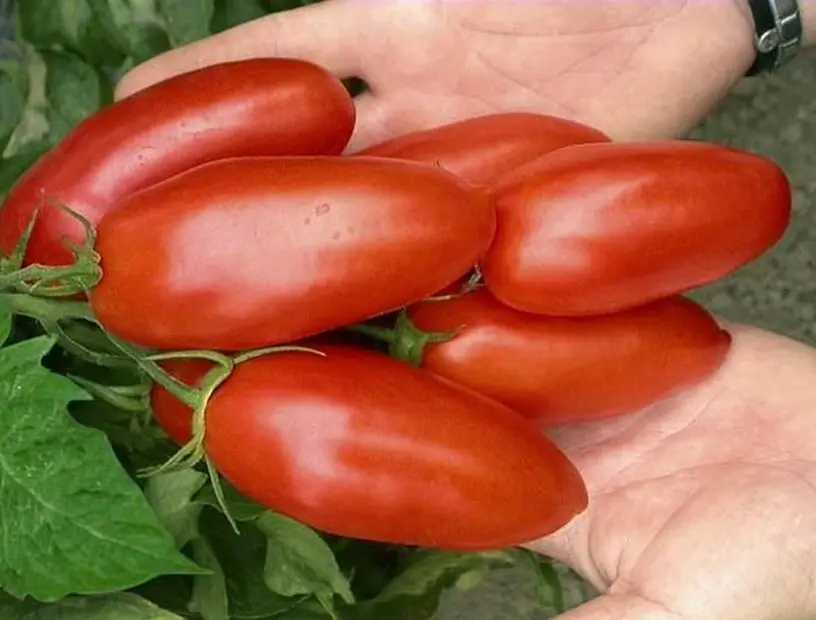
Tegenwoordig is het tomatenras "Lady's Man", waarvan de beoordelingen buitengewoon positief zijn, de leider onder de vroegrijpe tomaten. Amateurtuinders die minstens één keer in hun bed hebben geplant, zijn altijd fans gebleven"
Konijnen van het Strokach-ras: beschrijving van de soort, kenmerken van verzorging, voortplanting, kenmerkende kenmerken van het ras en regels voor het houden
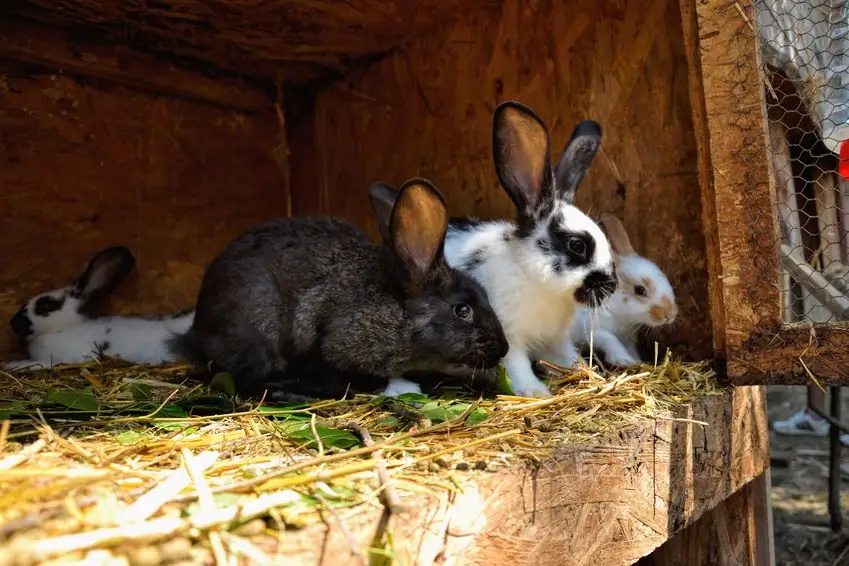
Als iemand een doel heeft om konijnen van het Strokach-ras te fokken, dan is het noodzakelijk om te onthouden dat het het beste is om alleen de sterkste en beste individuen van het Duitse ras te hebben. Als ze thuis worden gekweekt, slagen veel boeren er niet altijd in om een zuiver ras te fokken, omdat sommige individuen bont zijn of ziek worden