2025 Auteur: Howard Calhoun | [email protected]. Laatst gewijzigd: 2025-01-24 13:22
Gieten in schaalvormen wordt ook schaalgieten genoemd. En in het buitenland heet deze werkwijze Shell.
Algemene informatie
In de huidige industriële industrie worden veel verschillende gietmethoden gebruikt. Naast schaalgieten wordt ook investeringsgieten gebruikt, evenals in metalen mallen en verschillende andere methoden. Het algemene voordeel van deze gietmethoden, in vergelijking met zandvormen, is dat ze resulteren in nauwkeurigere eindmaterialen, zowel qua vorm als qua afmetingen. Bovendien wordt het aantal ruwheden op het oppervlak van dergelijke producten verminderd. In meer zeldzame gevallen, maar toch komt het voor dat de noodzaak voor latere bewerking na het smelten wordt geëlimineerd. Naast alles draagt het gebruik van gieten in schaalvormen en andere methoden ertoe bij dat dit proces zoveel mogelijk gemechaniseerd kan worden, waardoor ook de automatisering ervan toeneemt. En dit verhoogt natuurlijk de productiviteit van elke industriële faciliteit aanzienlijk.
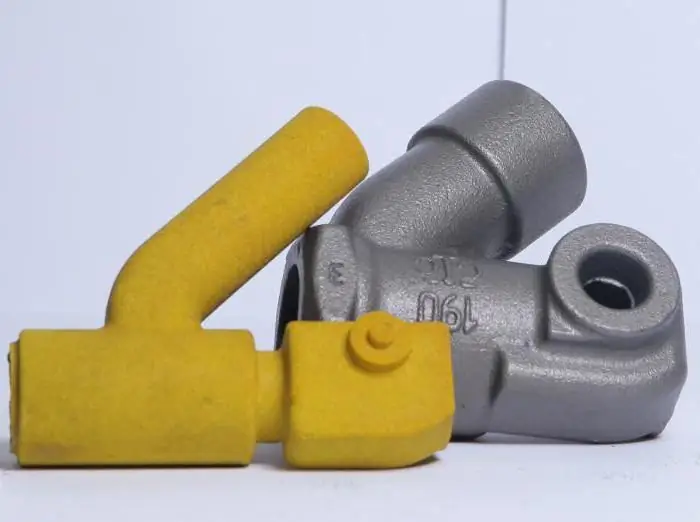
Shell-casting
Als we het hier specifiek over hebbenmethode, werd het voor het eerst geïntroduceerd in fabrieken in 1953. Momenteel wordt de methode vrij veel gebruikt. Het is bijvoorbeeld het gieten in schaalvormen dat de meeste onderdelen voor de Kirovets-tractor produceert. Alle onderdelen die volgens deze methode worden geproduceerd, zijn van de hoogste kwaliteit uit staal of gietijzer. Schelpgieten is een methode waarbij het uiteindelijke resultaat van het gieten een vorm heeft die bestaat uit twee zandharsschelpen. Deze methode voor het vervaardigen van onderdelen wordt ook alleen gebruikt in gevallen waarin het nodig is om een onderdeel te maken met kleine of middelgrote afmetingen, maar tegelijkertijd met een hoge nauwkeurigheid. Voorbeelden van toepassingen voor deze gietmethode zijn motoronderdelen of dunwandige gietstukken.
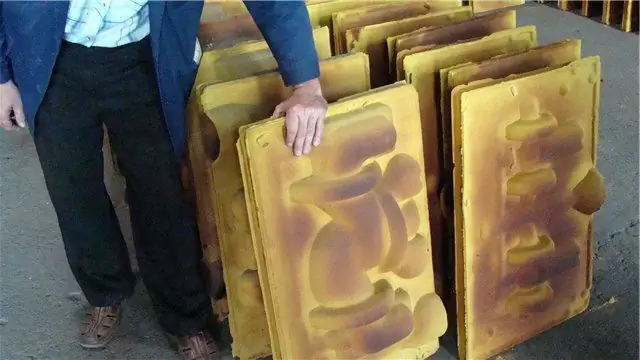
De essentie van de weg
Met deze werkwijze kun je verschillende onderdelen krijgen voor ventilatoren, motoren, pompen of textielmachines. De maximale lengte van het ontvangen product mag echter niet meer dan 1 meter bedragen en mag niet zwaarder zijn dan 200 kg.
De essentie van gieten in schaalvormen is gebaseerd op bepaalde eigenschappen van thermohardende harsen, die deel uitmaken van zand-harsmengsels. Het voordeel van het gebruik van dergelijke componenten is dat deze harsen de neiging hebben om snel en permanent uit te harden wanneer ze worden behandeld met een temperatuur van 200-250 graden Celsius.
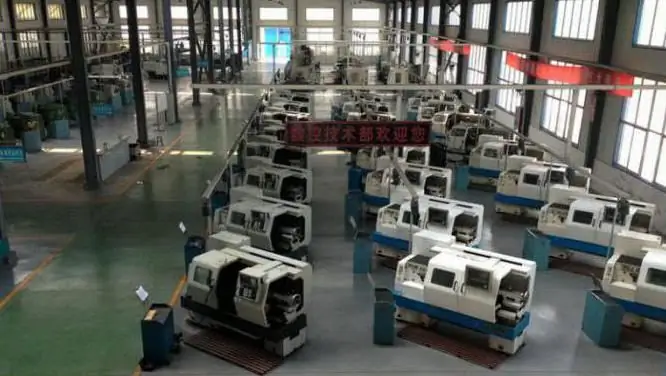
Een schelpvorm maken om te gieten
Om een mal te maken voor later gieten, is het nodig om fijnkorrelig kwartszand te hebben, dat wordt geleverd met de toevoeging van een thermohardende hars, die het verbindende element is om een volwaardige schaalvorm te verkrijgen. Deze materialen, met name de hars, worden gekozen omdat ze uitharden wanneer ze een bepaalde temperatuurbarrière passeren. Het productieproces is als volgt. Eerst wordt de hars verwarmd tot 140-160 graden Celsius. Onder invloed van een dergelijke omgeving verandert het in een vloeibare kleefmassa die de kwartszandvorm volledig omhult.
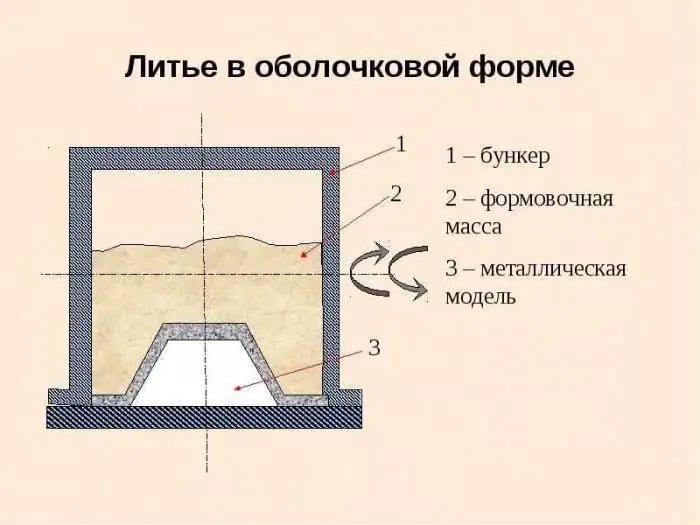
De reikwijdte van het gieten in schaalvormen is vrij breed en daarom wordt het proces van het maken van mallen automatisch of geautomatiseerd.
Nadat de mal volledig bedekt is met hars, wordt de temperatuur verhoogd tot 200-250 graden Celsius. Deze temperatuurdrempel is voldoende om de lijmmassa onomkeerbaar uit te harden en vorm te geven. Verder, wanneer het proces van het gieten van onderdelen begint, dat wil zeggen, wanneer het gesmolten metaal de mal binnenkomt, bereikt de temperatuur daarin ongeveer 600 graden. Deze modus is voldoende om ervoor te zorgen dat de hars niet smelt, maar uitbrandt, terwijl de poriën op de mal zelf achterblijven, waardoor het ontsnappen van gassen wordt vergemakkelijkt.
Voor- en nadelen van het gieten van schaalvormen
Net als elk ander productieproces heeft dit zijn voor- en nadelen. Als we deze manier van gieten vergelijken met bijvoorbeeld ingieten,gewone zandvormen, er zijn verschillende voordelen:
- Het eerste en nogal significante verschil is de nauwkeurigheidsklasse, die 7-9 is. Bovendien wordt de oppervlakteafwerking van het verkregen onderdeel verbeterd tot 3-6. Bovendien worden toeslagen verminderd, die zijn toegestaan voor latere bewerking van het resulterende onderdeel na het gieten.
- Een van de grote pluspunten is een aanzienlijke verlaging van de arbeidskosten voor de vervaardiging van gietstukken.
- Deze gietmethode vermindert het verbruik van gietmaterialen, evenals de hoeveelheid metaal omdat de grootte van de poortkanalen wordt verkleind.
- Aanzienlijke vermindering van de hoeveelheid huwelijksoutput.
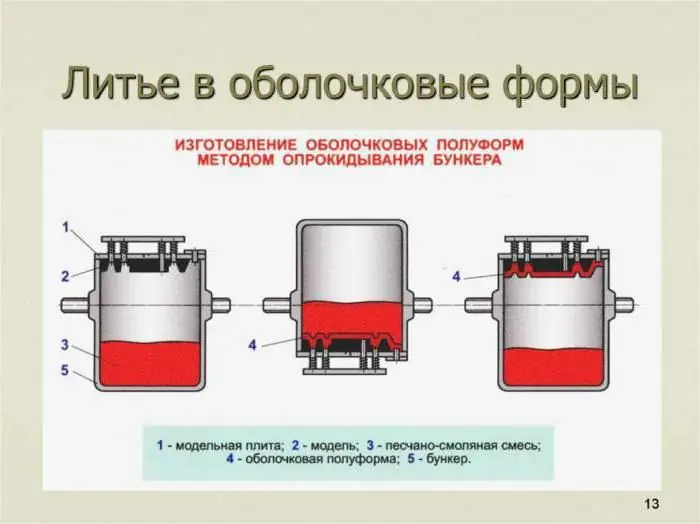
Er zijn echter enkele nadelen aan het gieten in schaalvormen. Deze omvatten:
- Levensduur schelpvorm - 1 gietstuk.
- De kosten van het vormen van zand zijn vrij hoog.
- Hoog percentage schadelijke gassen.
Corpusvormingsproces
Het lichaamsvormingsproces wordt in zes fasen uitgevoerd:
- De eerste stap is het proces van het gieten van het mengsel op een heet metalen model, evenals het proces om het enkele tientallen seconden te bewaren totdat zich een dunne, sterke korst rond het onderdeel vormt. Meestal zijn modellen gemaakt van gietijzer en wordt hun verwarming uitgevoerd tot 230-315 graden.
- Daarna is het noodzakelijk om een operatie uit te voeren om overtollig vormzand te verwijderen. De dikte van de korst moet uiteindelijk van 10 tot 20. zijnmm. Het hangt af van de verblijftijd van het mengsel op het model en van de temperatuur.
- Daarna is het noodzakelijk om de modelplaat samen met de mal over te brengen naar de oven, waar ze zullen zijn tot het einde van het uithardingsproces. Aan het einde van deze procedure moet de sterkte van de schaal tussen 2,4 en 3,1 MPa zijn.
- Na uit de oven te zijn verwijderd, wordt de geharde schaal van de plaat verplaatst. Voor deze procedure wordt een speciale duwer gebruikt.
- Daarna worden twee of meer modellen aan elkaar vastgemaakt met een soort klem of door te lijmen. Deze mallen kunnen worden gebruikt voor het gieten in schaalvormen of gewoon worden bewaard. Bijna onbeperkte houdbaarheid.
- Voordat het gietproces in de voltooide mal wordt gestart, wordt er een shot in gegoten, wat helpt om de mal tijdens verder gieten te voorkomen of te vernietigen.
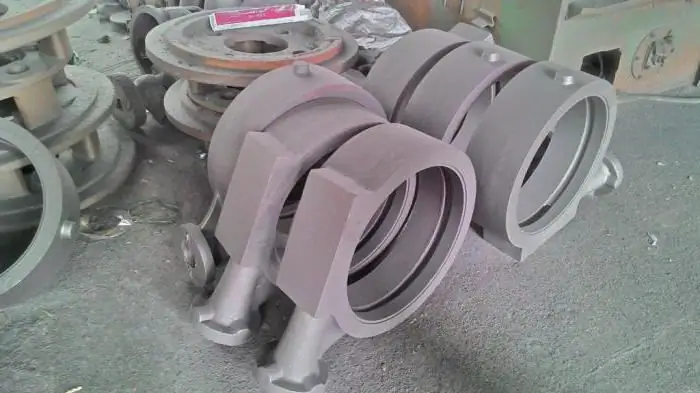
Castdetails
Het is de moeite waard om te beginnen met het feit dat typische toleranties die zijn toegestaan bij de vervaardiging van gereedschap 0,5 mm kunnen zijn. Oppervlakteruwheid is toegestaan in het bereik van 0,3 tot 0,4 micron. Dergelijke limieten worden gerechtvaardigd door het gebruik van fijnkorrelig zand. Ook vermeldenswaard: het gebruik van hars draagt er in hoge mate toe bij dat het oppervlak erg glad is.
Productievolumes
Om betrokken te zijn bij de productie van dergelijke mallen en onderdelen, is het noodzakelijk om een matrijsmodel te installeren. De benodigde tijd voor installatie is minder dan een week. Nadat de installatie is voltooid, kan de uitvoerhoeveelheid:bereik van 5 tot 50 stuks per uur. Dergelijke productievolumes per uur zijn vrij reëel, maar hiervoor is het noodzakelijk om het gietproces dienovereenkomstig voor te bereiden. De belangrijkste materialen die nodig zijn voor het gieten zijn gietijzer, aluminium, koper en legeringen van dit soort metalen. Een ander noodzakelijk materiaal is een legering die aluminium en magnesium gebruikt.
Aanbevolen:
Waar moet je op letten bij het huren van een appartement: regels voor het huren van een appartement, het opstellen van een contract, het controleren van meterstanden, beoordelingen
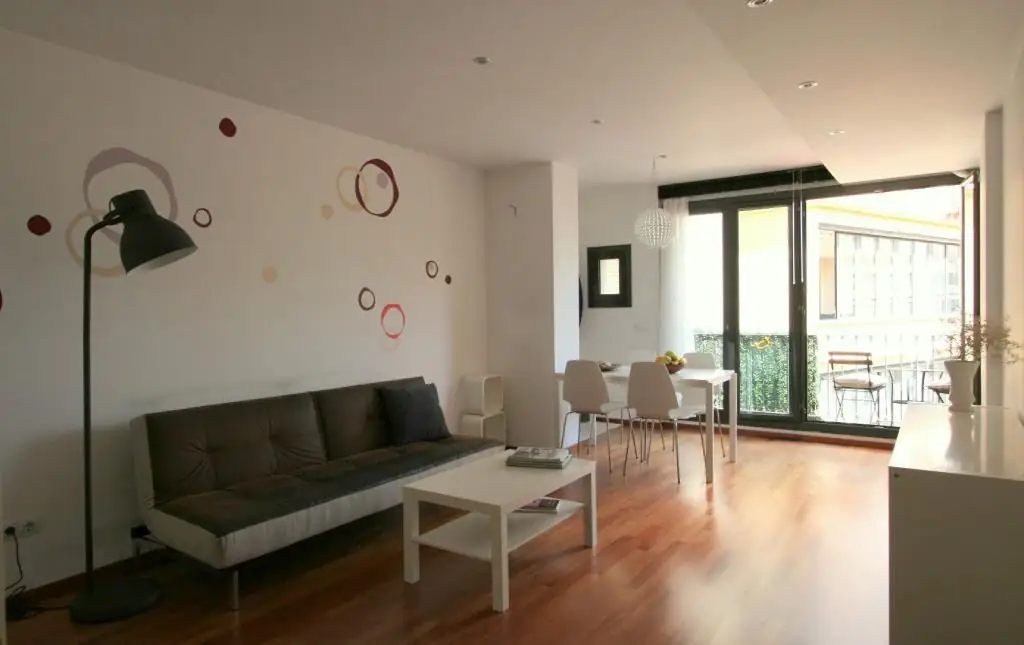
Ga je een appartement huren, maar ben je bang om opgelicht te worden? Uit dit artikel leer je hoe je een appartement correct huurt, hoe je een appartement kiest, waar je op moet letten bij het intrekken en de nuances van het opstellen van een huurovereenkomst
Technisch paspoort voor thuis: hoe en waar te maken? Productievoorwaarden van een technisch paspoort voor het huis
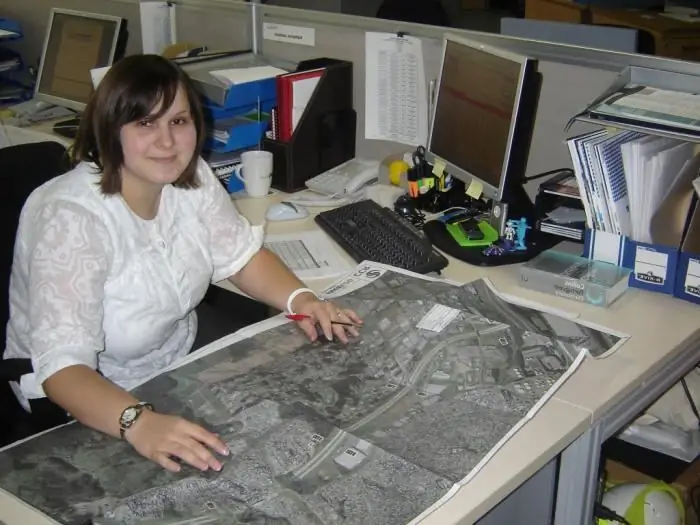
Een van de belangrijkste documenten met betrekking tot onroerend goed is een technisch paspoort voor een huis. Het is nodig om elke transactie uit te voeren en wordt vervaardigd in de BTI op de locatie van de faciliteit. Hoeveel kost het, welke documenten moeten worden verzameld, evenals de geldigheid van het kentekenbewijs en andere nuances in meer detail in het volgende materiaal
Machines voor het maken van sintelblokken. Apparatuur voor de productie van sintelblokken
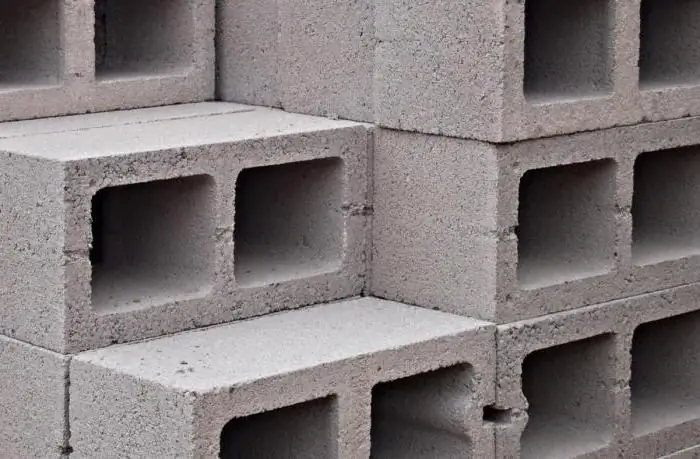
Het artikel is gewijd aan de productie van sintelblokken. Er wordt rekening gehouden met de fabricagetechnologie en de gebruikte apparatuur:
Wat is het kapitaaldekkings- en verzekeringsdeel van het pensioen? De termijn voor de overdracht van het kapitaalgedekte deel van het pensioen. Welk deel van het pensioen is verzek
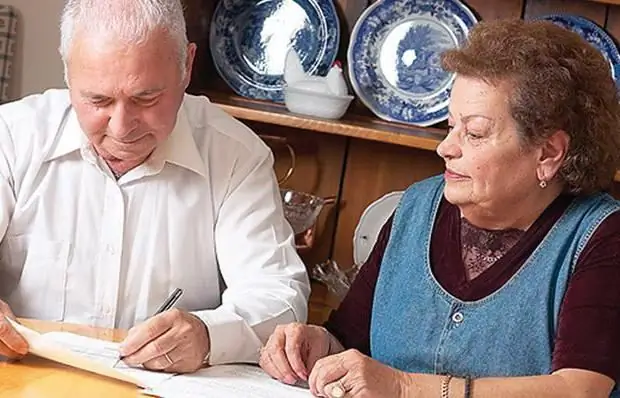
In Rusland is de pensioenhervorming al geruime tijd van kracht, iets meer dan een decennium. Desondanks begrijpen veel werkende burgers nog steeds niet wat het kapitaalgedekte en verzekerde deel van een pensioen is, en bijgevolg welke zekerheid hen op oudere leeftijd te wachten staat. Om dit probleem te begrijpen, moet u de informatie in het artikel lezen
De ui voorbereiden om op het hoofd te planten. Uiensets voorbereiden voor het planten. De grond voorbereiden voor het planten van uien in het voorjaar
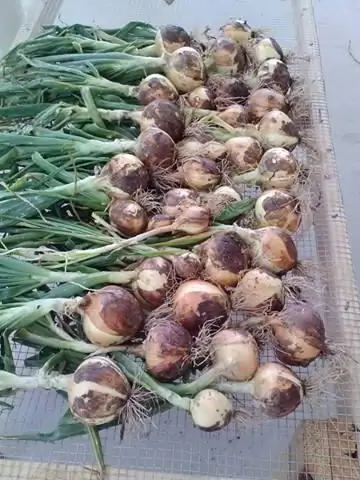
Elke huisvrouw weet dat er altijd uien in huis moeten zijn. Dit product wordt aan bijna elk gerecht toegevoegd, het kan ons lichaam grote voordelen bieden