2025 Auteur: Howard Calhoun | [email protected]. Laatst gewijzigd: 2025-01-24 13:22
Tegenwoordig zijn een groot aantal verschillende dingen, onderdelen, enz. gemaakt van staal. Uiteraard vereist dit een grote hoeveelheid bronmateriaal. Daarom gebruiken de fabrieken al lang de methode van continu gieten van staal, gekenmerkt door het belangrijkste kenmerk: hoge productiviteit.
Essentiële uitrusting voor werk
Tot op heden zijn er verschillende installaties bekend om op deze manier staal te gieten, afgekort als UNRS. Aanvankelijk werd een verticale installatie ontwikkeld en in productie genomen, 20-30 meter onder het niveau van de werkvloer. Later werd echter de wens om af te zien van de verdieping van de vloer de belangrijkste motor voor de ontwikkeling van deze installaties. Dit leidde tot de ontwikkeling en implementatie van continugietinstallaties van het torentype. De hoogte van deze installaties was 40 m. Deze versie van de machine werd echter om twee redenen niet veel gebruikt. Eerst bouwenzo'n eenheid in de werkplaats is behoorlijk problematisch en arbeidsintensief. Ten tweede deden zich nog meer problemen voor met de werking ervan.
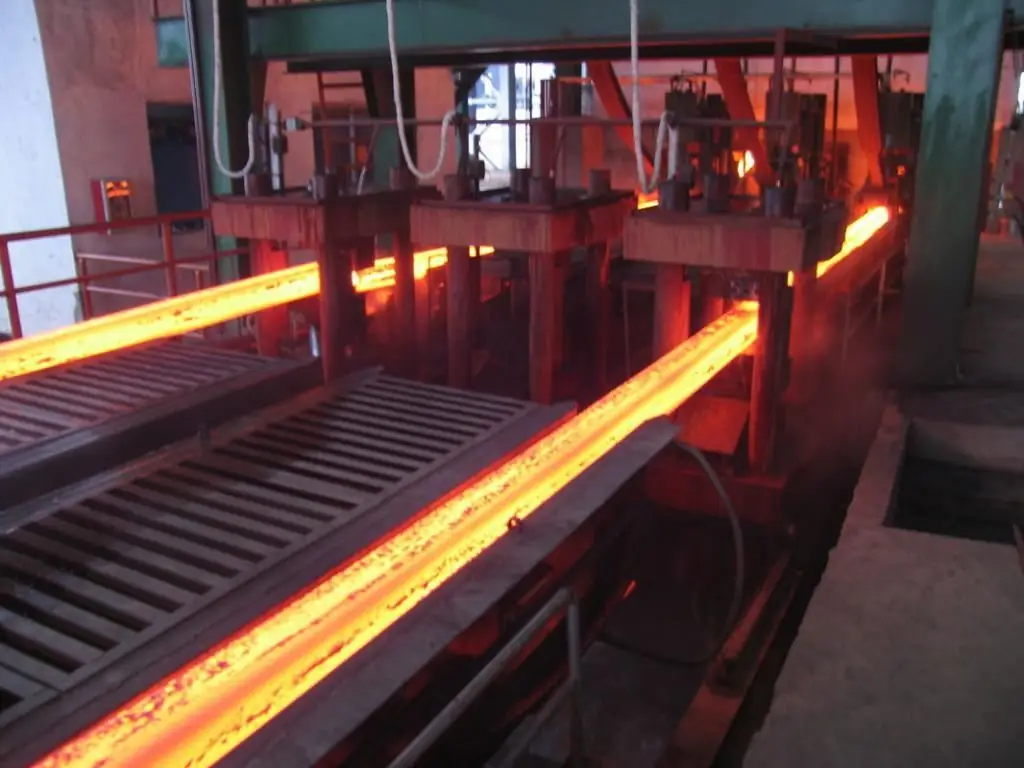
Gebogen en radiale installaties
Na verloop van tijd werd het continu gieten van staal overgebracht naar het werk met verticale buigmachines. Het belangrijkste kenmerk is het buigen van de staaf die 90 graden achter de assen naar buiten komt. Daarna werd in de installatie een speciaal richtmechanisme gebruikt om de staaf recht te trekken, en pas na deze fase vond het snijden plaats. Continu gieten van staal op dergelijke apparatuur is om de een of andere reden niet erg populair geworden. Ten eerste maakte de bocht het natuurlijk mogelijk om de hoogte te verminderen, maar tegelijkertijd de dwarsdoorsnede van de staaf zelf ernstig te beperken. Hoe meer er nodig was om een deel van het materiaal te krijgen, hoe groter de bocht moest zijn, waardoor de hoogte weer toenam. Ten tweede werden de buigmachines met nog grotere moeilijkheden in de staalfabrieken geplaatst dan de verticale.
Tegenwoordig winnen installaties voor het continu gieten van radiaal staal steeds meer aan populariteit. Op een dergelijke eenheid wordt de staaf gevormd in de mal en verlaat deze langs dezelfde boog waarlangs deze erin is binnengekomen. Daarna wordt het rechtgetrokken door een pull-correct mechanisme. En dan kun je de staaf al in blanco's snijden. Het is dit ontwerp dat in de praktijk het meest rationeel bleek te zijn om de goederenstroom in de staalfabriek te organiseren.
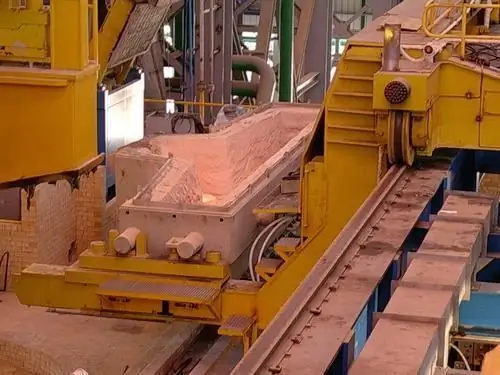
Waar begint het casten
Technologie van continustaalgieten is een nogal ingewikkeld proces. Het is echter redelijk om te zeggen dat het principe hetzelfde blijft, ongeacht de gebruikte productie-opstelling. U kunt de technologie beschouwen aan de hand van het voorbeeld van een verticale UNRS.
De machine wordt geleverd met een pollepel om staal door een speciale kraan te gieten. Daarna stroomt het staal in de verdeelbak, die voorzien is van een stop. Voor enkelstrengs machines zal er één stop zijn, voor meerstrengs machines zal er één stop per stroom zijn. Bovendien heeft de verdeelbak een speciaal schot om de slak vast te houden. Vanuit de verdeelbak stroomt het staal in de mal, door een doseerglas of een stop. Belangrijk hierbij is dat voor het eerste gieten het zaad vanaf de onderzijde in de mal wordt gebracht. Het vult ofwel de dwarsdoorsnede van de hele mal, of alleen de vorm van het werkstuk. De bovenste laag van het zaad zal de onderkant van de mal zijn. Bovendien heeft het ook de vorm van een zwaluwstaart voor toekomstige koppeling met een staaf.
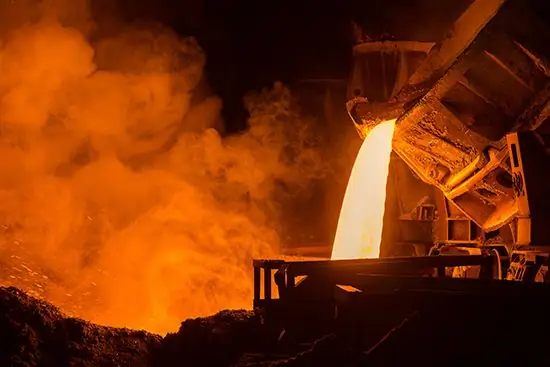
Verdere casting
Vervolgens, in het proces van continu gieten van staal, is het noodzakelijk om te wachten tot het niveau van grondstoffen boven het zaad stijgt tot een hoogte van ongeveer 300-400 mm. Wanneer dit gebeurt, start het mechanisme waardoor de trekinrichting in werking treedt. Het heeft trekrollen, onder invloed waarvan het zaad zal vallen en de gecreëerde staaf meetrekt.
Een continugietmachine heeft een mal van meestal koper met holle wanden. Hij is onder intensdoor de werking van koelwater, en het inwendige gedeelte ervan komt overeen met de vorm van de te verkrijgen ingot. Het is hier dat de ingots-lege korst wordt gevormd. Bij hoge gietsnelheden kan het scheuren van deze korst en lekkage van metaal optreden. Om dit te voorkomen, wordt de mal gekenmerkt door heen en weer gaande bewegingen.
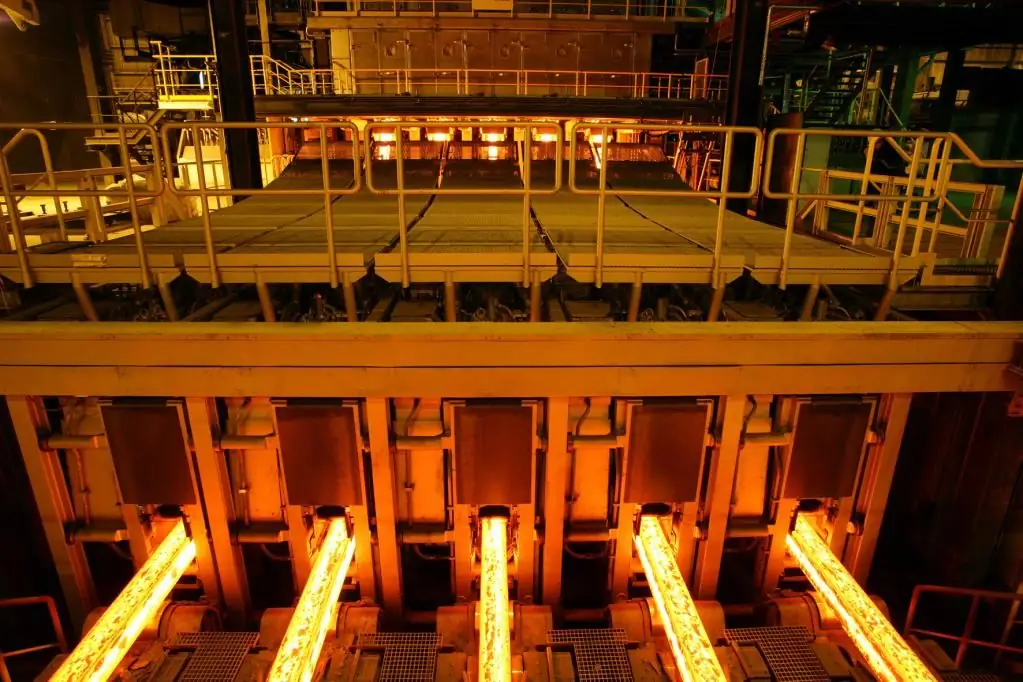
Kenmerken van de matrijsbewerking
De continugietmachine heeft een elektromotor die verantwoordelijk is voor het creëren van deze heen en weer gaande beweging. Dit wordt gedaan door de kracht van de versnellingsbak met een draaimechanisme van het nokkentype. Eerst beweegt de mal in dezelfde richting als het werkstuk, dat wil zeggen naar beneden, en nadat het proces is voltooid, keert het terug naar boven. De zwaaislag is van 10 tot 40 mm. De mal is een belangrijk compartiment bij het continu gieten van staal op elk type apparatuur, en daarom zijn de wanden gesmeerd met paraffine of een ander smeermiddel dat geschikt is voor de kenmerken.
Het is vermeldenswaard dat in moderne apparatuur het metaalniveau radiometrisch wordt gecontroleerd door een stuursignaal op de pollepelstop toe te passen. In de matrijs zelf kan een neutrale of een reducerende atmosfeer boven het metaalniveau worden gecreëerd om oxidatie van het product tijdens de productie te voorkomen.
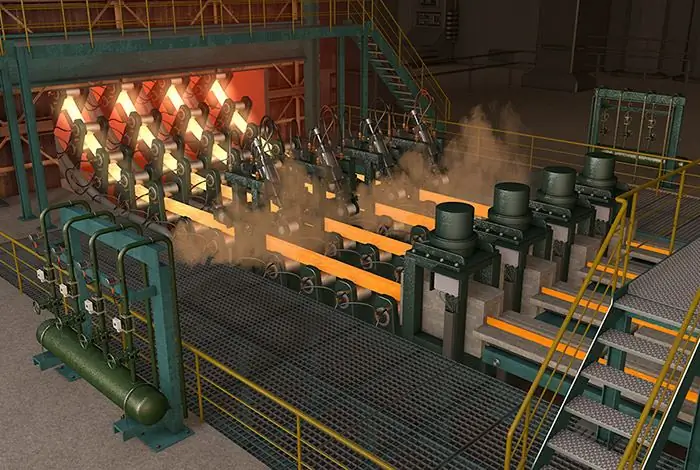
Ingots peel
Het is vermeldenswaard dat werken onder vacuüm ook als een veelbelovende gietmethode wordt beschouwd. Een eenheid kan uitvoeren:door meerdere vormen tegelijk gieten. Het aantal streams van één installatie kan dus oplopen tot acht.
De warmteafvoerwerking van het koude zaad wordt gebruikt om de bodem van de staafhuid te vormen. De ingot verlaat de mal onder invloed van het zaad, dat in de secundaire koelzone (SCZ) wordt gezogen. In het midden van de knuppel zal het staal nog in vloeibare toestand zijn. Hierbij is het belangrijk op te merken dat, volgens de eisen van de staalgiettechnologie, de huiddikte bij het verlaten van de mal minimaal 25 mm moet zijn. Om aan deze eisen te voldoen, is het noodzakelijk om het juiste materiaaldebiet te kiezen.
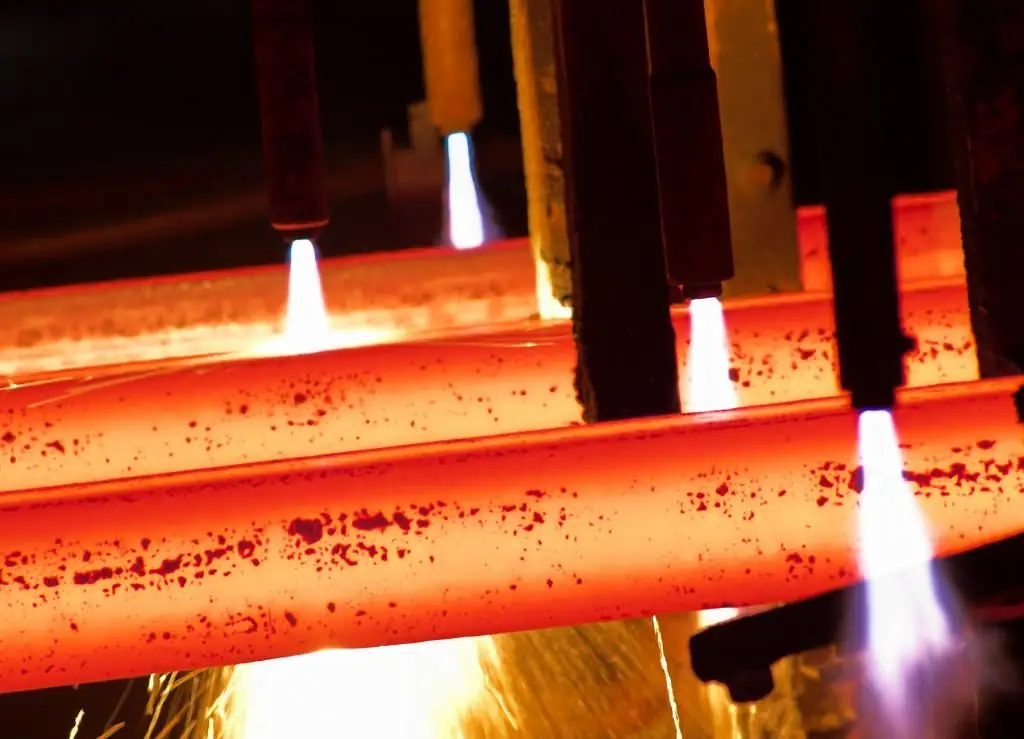
Kenmerken van het installatie- en gietproces
Technologische kenmerken zijn ongeveer als volgt. Als de doorsnede van de staaf 160x900 mm is, moet de snelheid tussen 0,6 en 0,9 m/min liggen. Als de doorsnede 180x1000 mm is, wordt de snelheid verlaagd tot 0,55-0,85 m/min. De hoogste snelheidsindicator is vereist voor de doorsnede van een vierkante staaf 200x200 mm - 0,8-1,2 m/min.
Op basis van de bovenstaande indicatoren kunnen we concluderen dat de gemiddelde gietsnelheid van één streng met continugiettechnologie 44,2 t/u is. Als je de optimale snelheid overschrijdt, zal de centrale porositeit toenemen.
Verder is het vermeldenswaard dat de stabiliteit van het gietstuk en de kwaliteit van het product zelf worden beïnvloed door de temperatuur van het metaal. Empirisch werd gevonden dat bij een temperatuur van meer dan 1560 gradenBij Celsius is het oppervlak van de baar vaak bedekt met scheuren. Is de temperatuur lager dan aangegeven, dan zal het glas vaak worden aangedraaid. Zo werd gevonden dat de optimale temperatuur voor de methode van continu gieten van staal 1540-1560 graden Celsius zou zijn. Om deze indicator te behouden, moet de verwarmingstemperatuur van de oven vóór de release in het bereik van 1630-1650 graden zijn.
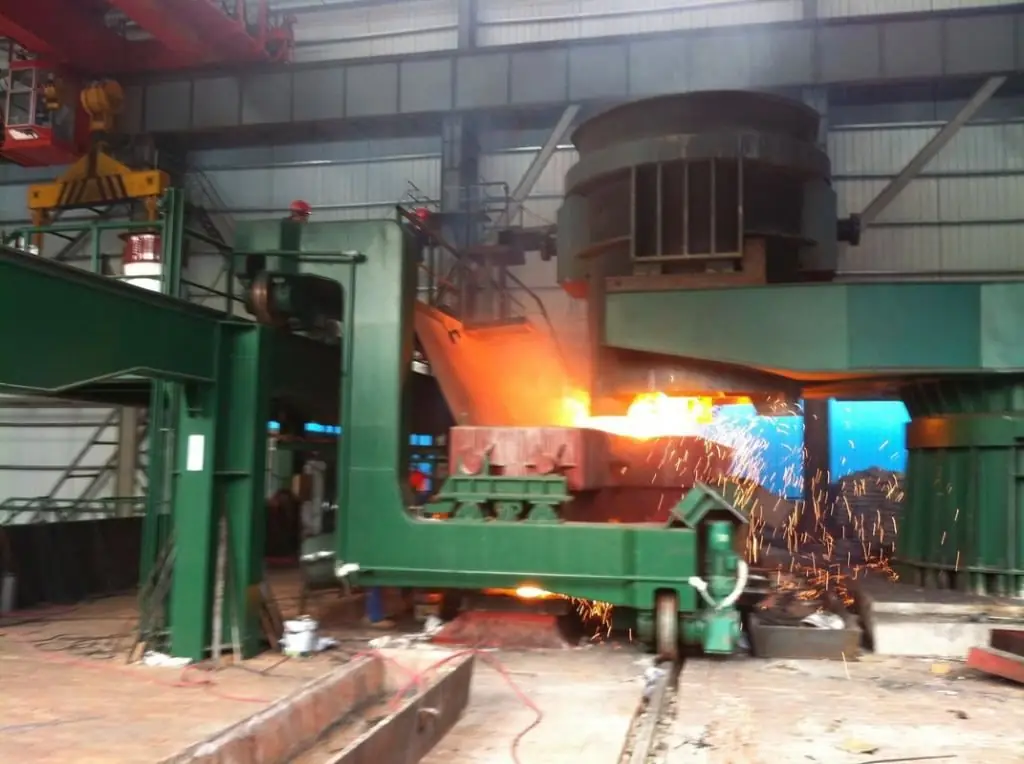
Secundaire koelzone
In deze sectie wordt de meest intensieve en directe koeling van de ingot uitgevoerd met behulp van water dat uit de spray komt. Er is een speciaal systeem van stationaire, geen aandrijfrollen. Hun rotatie voorkomt dat de staaf buigt of kromtrekt. Door intense afkoeling in deze zone zullen de wanden van de staaf snel dikker worden en zal de kristallisatie zich in de diepte verspreiden. De snelheid waarmee de staaf wordt getrokken en de mate van afkoeling moeten zodanig worden gekozen dat tegen de tijd dat de staaf de trekrollen binnengaat, deze al volledig stevig is.
Wat zijn de voordelen van continu gieten
Aangezien deze methode om staal te gieten de methode van gieten in vormen heeft vervangen, is het de moeite waard om met deze methode te vergelijken. In het algemeen is het de moeite waard om de volgende voordelen te benadrukken: hogere productiviteit, lagere kosten en verminderde arbeidsintensiteit van het proces. Door de constante vorming van de staaf wordt de krimpholte overgebracht naar de staart, in tegenstelling tot de staafvormen, waar elke staaf zijn eigen holte had. Hierdoor neemt het opbrengstpercentage van geschikt metaal aanzienlijk toe. UNRS stelt u in staat omeen werkstuk met verschillende vormen, van een klein vierkant 40x40 mm tot een rechthoek van 250x1000 mm. Het gebruik van continugietmachines maakte het mogelijk om de smeedmolens volledig te verlaten. Dit verlaagde de kosten van het productieproces aanzienlijk, en daarmee de prijs op de markt. Bovendien is het proces van metallurgische verwerking vereenvoudigd.
Flaws
Ondanks de mogelijkheid van hoge mechanisatie en automatisering van het proces, een hoog percentage goede ingots en andere hierboven beschreven voordelen, heeft deze methode ook enkele negatieve kanten. De nadelen van continu gietstaal zijn als volgt.
Ten eerste is er geen mogelijkheid om blokken met een complexe configuratie te produceren. Ten tweede is het aanbod van ingots en blanks vrij beperkt. Het is vrij moeilijk om machines om te bouwen om grondstoffen van een ander merk te gieten, wat de uiteindelijke kosten van een product van een ander merk kan verhogen als het in dezelfde fabriek wordt geproduceerd. Sommige staalsoorten, bijvoorbeeld kokende, kunnen met deze methode helemaal niet worden gemaakt.
Het laatste nadeel van de continue methode van staalgieten is erg belangrijk. Het is een mogelijke storing in de apparatuur. Het falen van de UNRS zal leiden tot enorme prestatieverliezen. Hoe langer het duurt om te repareren, hoe meer verliezen zullen toenemen.
Aanbevolen:
Hoskold-methode, Ring-methode, Inwood-methode - manieren om investeringskapitaal terug te krijgen
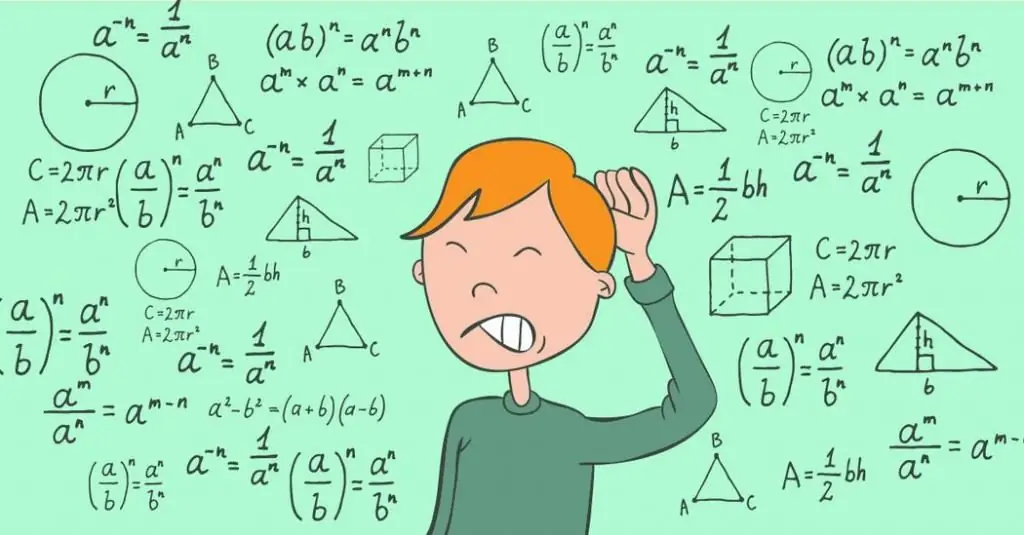
Wanneer iemand zijn eigen geld investeert in een inkomen genererend object, verwacht hij niet alleen winst te ontvangen van het geïnvesteerde kapitaal, maar ook om het volledig terug te betalen. Dit kan worden gedaan door wederverkoop of door het behalen van dergelijke winsten die niet alleen rente opleveren, maar ook geleidelijk investeringen opleveren
Rookwinkel: voorbereiding van benodigde documenten, opstellen van een businessplan, selectie van benodigde apparatuur, doelen en ontwikkelingsstadia
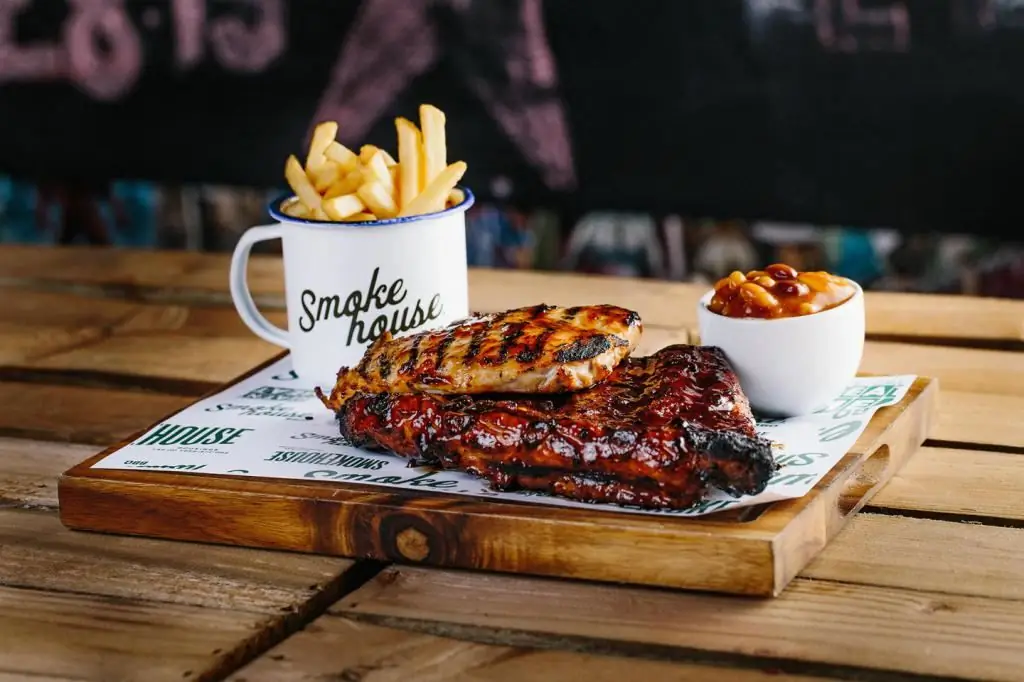
Het artikel gaat over een bedrijf als een rookwinkel. Leer hoe u een bedrijf start en waar u moet beginnen. Over hoe je apparatuur moet kiezen en hoe die moet zijn. Over waar je op moet letten bij het kiezen van leveranciers en over het proces van het produceren van gerookte producten
Kapper aan huis: voorbereiding van benodigde documenten, opstellen van een businessplan, selectie van benodigde apparatuur, doelen en ontwikkelingsstadia
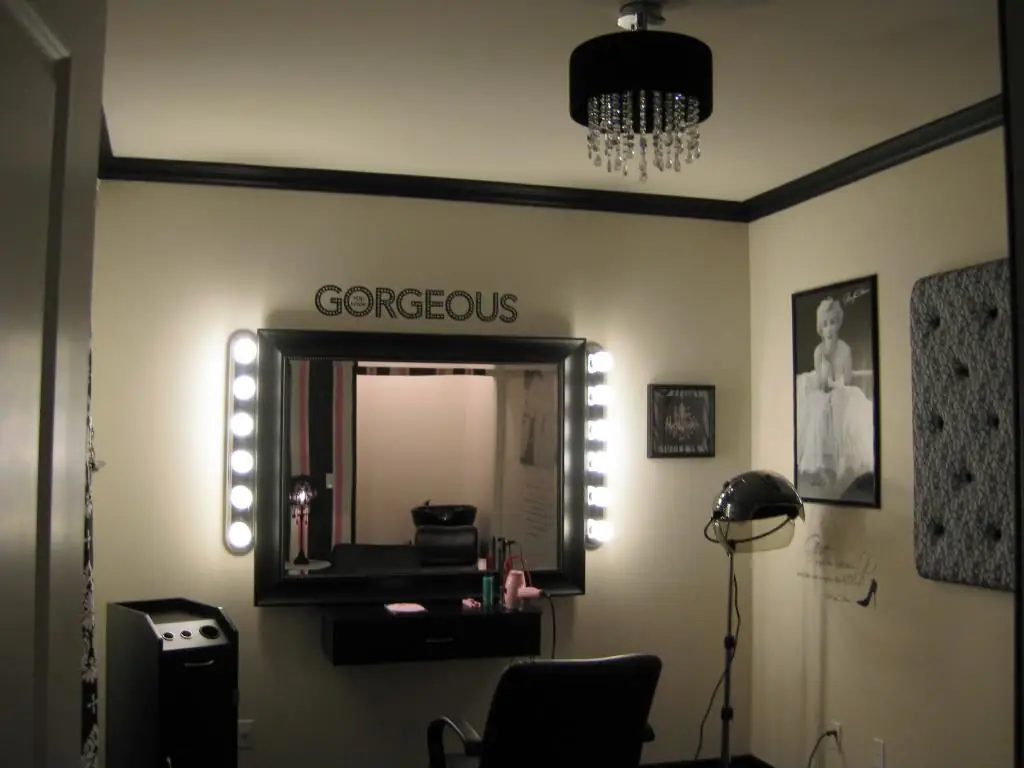
Kapsalons voor creatieve mensen is een veelbelovende en interessante business. Welnu, als er geen geld is om een grote salon te openen, dan is het in het begin heel goed mogelijk om uw project vanaf de eerste fase te starten. Hiervoor kan een kapsalon aan huis worden georganiseerd, wat geen grote investeringen vereist. Is het de moeite waard om zo'n bedrijf aan te gaan en welke stappen moet je doorlopen om het te openen?
Letterpress is Boekdruktechnologie, moderne ontwikkelingsstadia, benodigde apparatuur, voor- en nadelen van dit type drukwerk
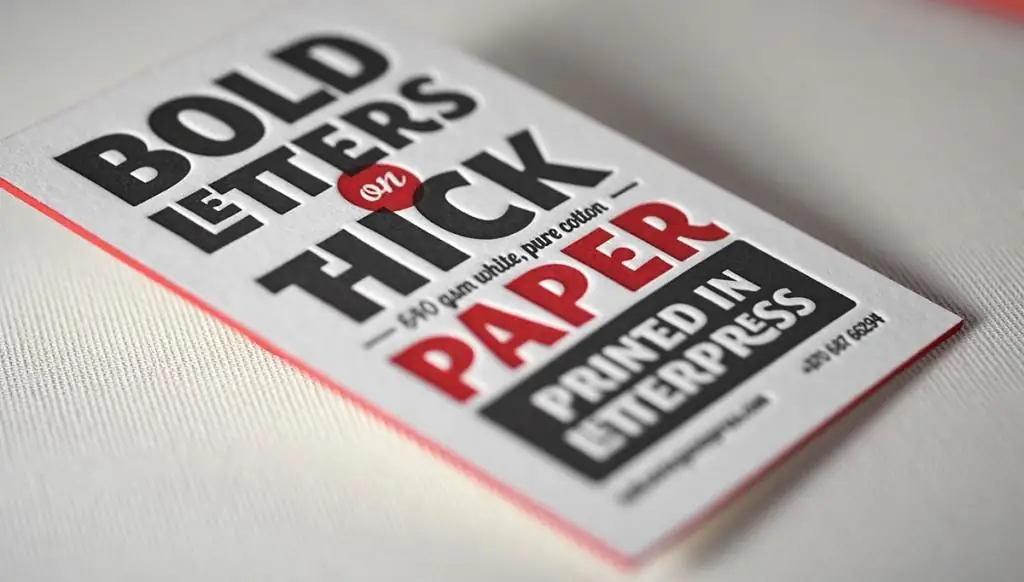
Letterpress is een van de typische methoden voor het toepassen van informatie met behulp van een reliëfmatrix. De elementen die uitsteken, worden bedekt met verf in de vorm van een pasta en vervolgens tegen het papier gedrukt. Zo worden verschillende massatijdschriften, naslagwerken, boeken en kranten gerepliceerd
Gieten in siliconen mal: apparatuur. Vacuüm gieten in siliconen mallen
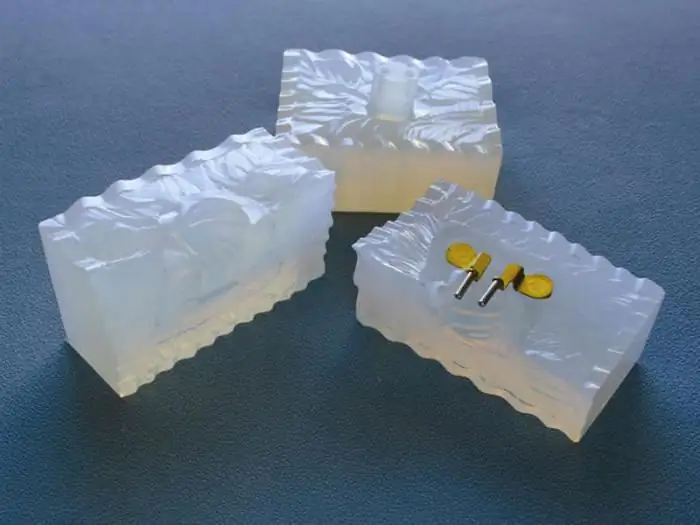
Voor de vervaardiging van een klein aantal plastic plano's wordt vacuümgieten in siliconenvormen het vaakst gebruikt. Deze methode is vrij economisch (het maken van een metalen mal kost meer tijd en geld). Bovendien worden siliconenvormen herhaaldelijk gebruikt, wat ook de productiekosten aanzienlijk verlaagt