2025 Auteur: Howard Calhoun | [email protected]. Laatst gewijzigd: 2025-01-24 13:22
In de productie- en bouwsector is niet-destructief testen een van de meest populaire methoden voor het diagnosticeren van materialen. Met behulp van deze methode evalueren bouwers de kwaliteit van lasverbindingen, controleren ze de dichtheid in bepaalde secties van constructies, waardoor diepe gebreken en gebreken worden onthuld. Diagnostische magnetische foutdetectoren kunnen zowel oppervlakte- als ondergrondse schade detecteren met een hoge mate van nauwkeurigheid.
Apparaat
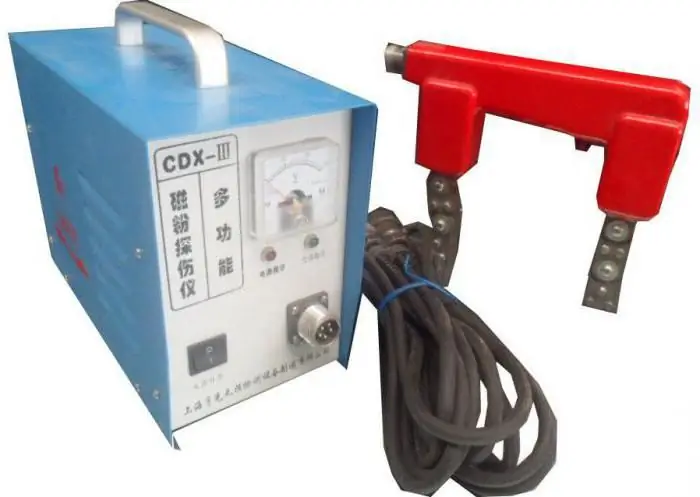
De basis van het segment van magnetische diktemeters en foutdetectoren zijn draagbare apparaten die zijn voorzien van magnetiseerbare werklichamen - meestal in de vorm van een tang. Uiterlijk zijn dit kleine apparaten, waarvan de vulling een elektromagneet is die de polen van de golfwerking regelt. In de middenklasse kun je werken met magnetische permeabiliteit, waarvan de coëfficiënt hoger is dan 40. De body is voorzien van een ergonomische handgreep, waardoor het apparaat op moeilijk bereikbare plaatsen kan worden gebruikt. Om elektrische stroom te leveren, zijn de instrumenten ook voorzien van een kabel die is aangesloten op een generatorstation (als er buiten wordt gewerkt) of op een huishoudelijk elektriciteitsnet van 220 V. Meer geavanceerde niet-destructieve testapparatuurheeft een stationaire basis die is aangesloten op een computer. Dergelijke diagnostische hulpmiddelen worden vaker gebruikt om de kwaliteit van gefabriceerde onderdelen in productie te controleren. Ze voeren kwaliteitscontroles uit en repareren de kleinste afwijkingen van de standaardindicatoren.
Ferroprobe foutdetectoren
Een verscheidenheid aan magnetische apparaten die zijn ontworpen om defecten op een diepte tot 10 mm te detecteren. Ze worden met name gebruikt om discontinuïteiten in de structuur van constructies en onderdelen op te lossen. Dit kunnen zonsondergangen, schelpen, scheuren en haarlijnen zijn. De fluxgate-methode wordt ook gebruikt om de kwaliteit van lassen te beoordelen. Na afloop van de werksessie kunnen magnetische foutdetectoren van dit type ook de mate van demagnetisatie van het onderdeel bepalen als onderdeel van complexe diagnostiek. In termen van toepassing op onderdelen van verschillende vormen en maten kennen de apparaten praktisch geen beperkingen. Maar nogmaals, men mag de maximale diepte van structuuranalyse niet vergeten.
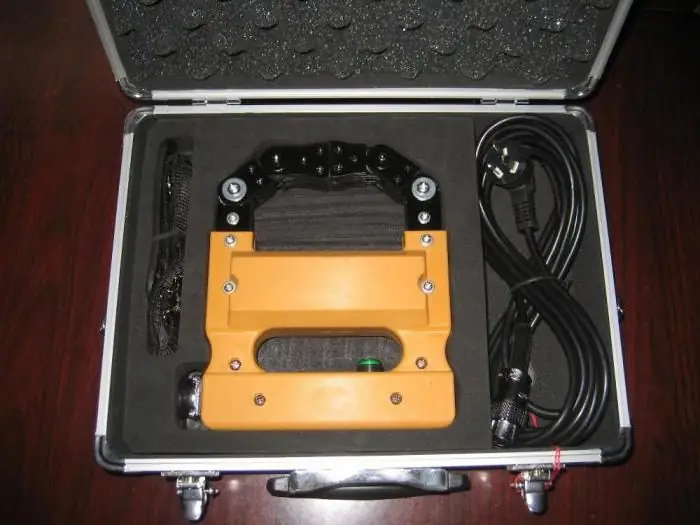
Magnitografische en wervelstroom-foutdetectoren
Met behulp van magnetografische apparaten kan de operator productfouten detecteren op een diepte van 1 tot 18 mm. En nogmaals, de beoogde tekenen van afwijkingen in de constructie zijn discontinuïteiten en defecten in lasverbindingen. De kenmerken van de wervelstroomtesttechniek omvatten de analyse van de interactie van het elektromagnetische veld met de golven die worden gegenereerd door wervelstromen die worden toegevoerd aan het onderwerp van controle. Meestal wordt een wervelstroom-foutdetector gebruikt om producten van elektrisch geleidende materialen te onderzoeken. Apparaten van dit typelaten een zeer nauwkeurig resultaat zien bij het analyseren van onderdelen met actieve elektrofysische eigenschappen, maar het is belangrijk om te bedenken dat ze op een ondiepe diepte werken - niet meer dan 2 mm. Wat de aard van defecten betreft, maakt de wervelstroommethode het mogelijk om discontinuïteiten en scheuren te detecteren.
Magnetische deeltjesfoutdetectoren
Dergelijke apparaten zijn ook voornamelijk gericht op oppervlaktedefecten die kunnen worden gerepareerd op een diepte van maximaal 1,5-2 mm. Tegelijkertijd wordt de mogelijkheid van onderzoek toegestaan om een breed scala aan defecten aan het licht te brengen - van de parameters van de las tot de detectie van tekenen van delaminatie en microscheuren. Het werkingsprincipe van dergelijke niet-destructieve testapparatuur is gebaseerd op de activiteit van poederdeeltjes. Onder invloed van een elektrische stroom worden ze gericht op de inhomogeniteit van magnetische oscillaties. Hiermee kunt u de onvolkomenheden van het oppervlak van het doelobject van studie corrigeren.
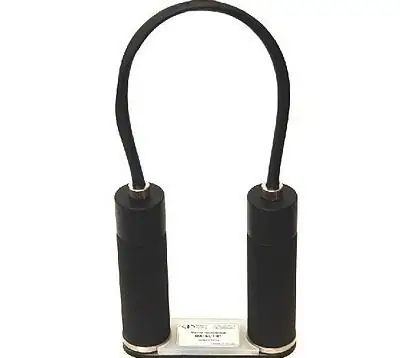
De hoogste nauwkeurigheid bij het bepalen van defecte gebieden met deze methode is aanwezig als het vlak van het defecte gebied een hoek van 90 graden vormt met de richting van de magnetische flux. Naarmate we van deze hoek afwijken, neemt ook de gevoeligheid van het instrument af. Tijdens het werken met dergelijke apparaten worden ook extra hulpmiddelen gebruikt om de parameters van defecten op te lossen. Zo is de magnetische foutdetector "Magest 01" in de basisconfiguratie voorzien van een dubbele loep en een ultraviolette zaklamp. Dat wil zeggen, de directe bepaling van de fout op het oppervlak wordt uitgevoerd door de operator door visuele inspectie.
Voorbereiding op het werk
Voorbereidende activiteiten kunnen in twee groepen worden verdeeld. De eerste omvat het direct voorbereiden van het werkoppervlak en de tweede - het instellen van het apparaat. Wat het eerste onderdeel betreft, het onderdeel moet worden ontdaan van roest, verschillende soorten vet, olievlekken, vuil en stof. Een hoogwaardig resultaat kan alleen worden verkregen op een schone en droge ondergrond. Vervolgens wordt de foutdetector ingesteld, waarbij de belangrijkste stap kalibratie met verificatie tegen standaarden zal zijn. De laatste zijn monsters van materialen met defecten, die kunnen worden gebruikt om de juistheid van de resultaten van de analyse van het apparaat te evalueren. Ook kunt u, afhankelijk van het model, het werkdieptebereik en de gevoeligheid vastleggen. Deze indicatoren zijn afhankelijk van de taken van het detecteren van defecten, de kenmerken van het materiaal dat wordt onderzocht en de mogelijkheden van het apparaat zelf. Moderne hightech foutdetectoren maken ook automatische aanpassing mogelijk volgens de gespecificeerde parameters.
Het onderdeel magnetiseren
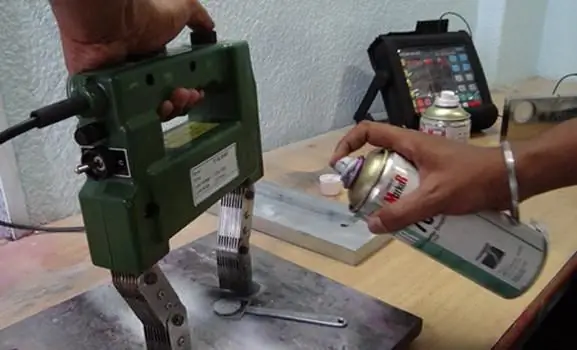
De eerste fase van werkoperaties, waarin de magnetisatie van het te onderzoeken object wordt uitgevoerd. In eerste instantie is het belangrijk om de stroomrichting en het type magnetisatie correct te bepalen met gevoeligheidsparameters. Met de poedermethode kunt u bijvoorbeeld paal-, cirkelvormige en gecombineerde impact op het onderdeel uitvoeren. In het bijzonder wordt circulaire magnetisatie uitgevoerd door een elektrische stroom rechtstreeks door het product, door de hoofdgeleider, door de wikkeling of door een afzonderlijk gedeelte van het element met de aansluiting van elektrische schakelaars te leiden. BIJIn de poolactiemodus zorgen magnetische foutdetectoren voor magnetisatie met behulp van spoelen, in een solenoïde medium, met behulp van een draagbare elektromagneet of met behulp van permanente magneten. Dienovereenkomstig stelt de gecombineerde methode u in staat om twee methoden te combineren door extra apparatuur aan te sluiten tijdens het magnetiseren van het werkstuk.
Toepassing van magnetische indicator
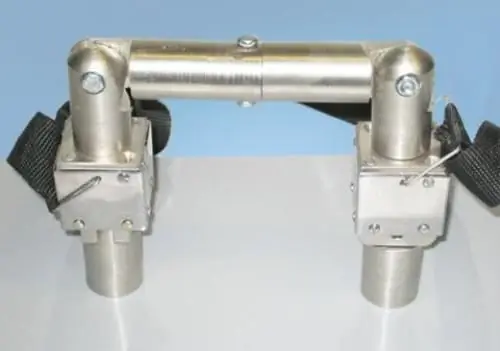
Indicatormateriaal wordt aangebracht op het vooraf voorbereide en gemagnetiseerde oppervlak. Hiermee kunt u de gebreken van het onderdeel identificeren onder invloed van een elektromagnetisch veld. Er is al gezegd dat poeders in deze hoedanigheid kunnen worden gebruikt, maar sommige modellen werken ook met suspensies. In beide gevallen is het belangrijk om, voordat u gaat werken, de optimale omstandigheden voor het gebruik van het apparaat te overwegen. Magnetische foutdetector "MD-6" wordt bijvoorbeeld aanbevolen voor gebruik bij temperaturen van -40 tot 50 °C en bij luchtvochtigheid tot 98%. Als de voorwaarden voldoen aan de vereisten voor gebruik, kunt u beginnen met het toepassen van de indicator. Het poeder wordt in het hele gebied aangebracht - zodat ook een kleine dekking van niet voor studie bestemde gebieden wordt geboden. Dit geeft een nauwkeuriger beeld van het defect. De suspensie wordt aangebracht door middel van een straal met behulp van een slang of spuitbus. Er zijn ook methoden om het onderdeel onder te dompelen in een container met een magnetisch indicatormengsel. Vervolgens kunt u direct doorgaan met het oplossen van problemen met het product.
Onderdeel inspecteren
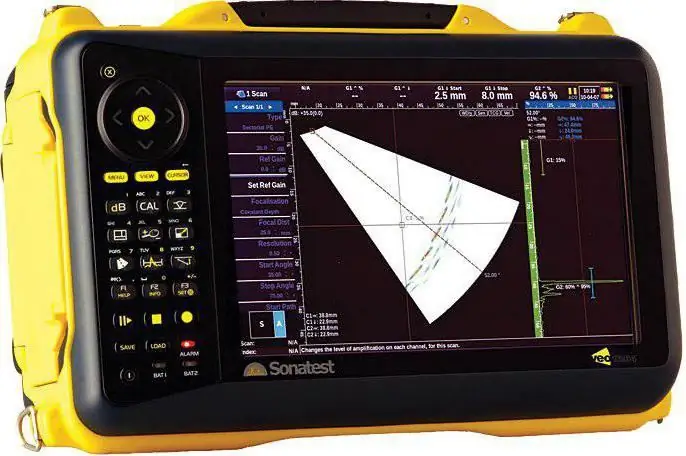
De operator moet wachten tot de indicatoractiviteit eindigt,of het nu poederdeeltjes of suspensie zijn. Het product wordt visueel gecontroleerd met de bovengenoemde apparaten in de vorm van optische apparaten. In dit geval mag de vergrotingskracht van deze apparaten niet groter zijn dan x10. Ook kan de operator, afhankelijk van de vereisten voor het onderzoek, al foto's maken voor een nauwkeurigere computeranalyse. Multifunctionele magnetische foutdetector-stations hebben in hun basisuitrusting apparatuur voor het decoderen van replica's met poederafzettingen. De tekeningen die tijdens het sorteren worden verkregen, worden vervolgens vergeleken met standaardmonsters, waardoor we een conclusie kunnen trekken over de kwaliteit van het product en de toelaatbaarheid ervan voor het beoogde gebruik.
Conclusie
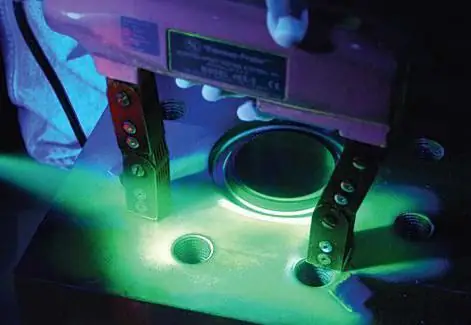
Magnetische foutdetectie-instrumenten worden veel gebruikt op verschillende gebieden. Maar ze hebben ook nadelen die het gebruik ervan beperken. Afhankelijk van de bedrijfsomstandigheden zijn dit onder meer de vereisten voor temperatuuromstandigheden en in sommige gevallen onvoldoende nauwkeurigheid. Als universeel controlemiddel raden experts aan om een meerkanaals magnetische foutdetector te gebruiken, die ook de functie van ultrasone analyse kan ondersteunen. Het aantal kanalen kan 32 bereiken. Dit betekent dat het apparaat optimale foutdetectieparameters kan behouden voor hetzelfde aantal verschillende taken. In wezen worden kanalen opgevat als het aantal bedrijfsmodi gericht op bepaalde kenmerken van het doelmateriaal en de omgevingsomstandigheden. Dergelijke modellen zijn niet goedkoop, maar ze bieden:de juistheid van de resultaten bij het detecteren van oppervlaktedefecten en interne structuur van verschillende soorten.
Aanbevolen:
Glasoven: soorten, apparaat, specificaties en praktische toepassing
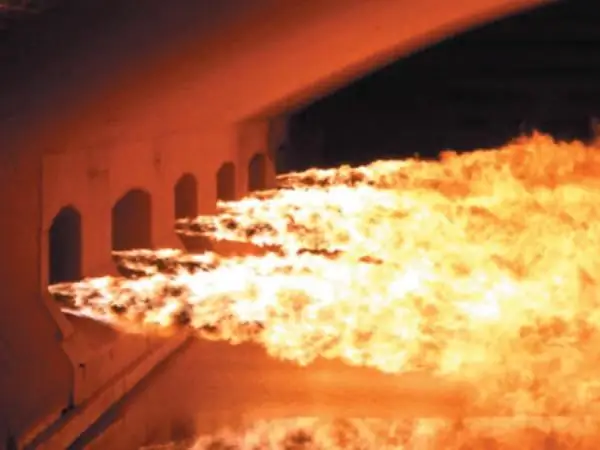
Tegenwoordig gebruiken mensen glas actief voor verschillende doeleinden. Het glasproductieproces zelf is het smelten van grondstoffen of lading. Glassmeltovens worden gebruikt om het materiaal te smelten. Ze zijn er in verschillende soorten en zijn ingedeeld volgens verschillende criteria
Magnetische grijper PML: goederenbeweging, classificatie, werkingsprincipe
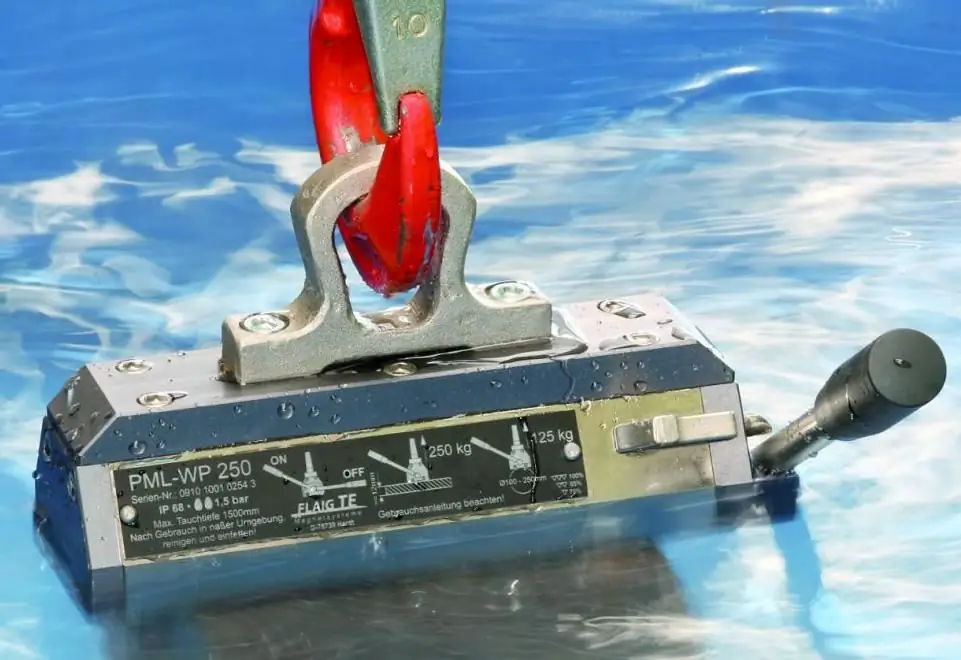
Magnetische grijpers van het type PML zijn eenvoudige apparaten die worden gebruikt voor het lossen en transporteren van ladingen van staal en gietijzer. Deze lastgrijpers hebben hun voordelen ten opzichte van andere typen grijpers en hebben praktisch geen nadelen, wat de reden is voor hun brede verspreiding
Mobiel tankstation: beschrijving, apparaat, werkingsprincipe, toepassing
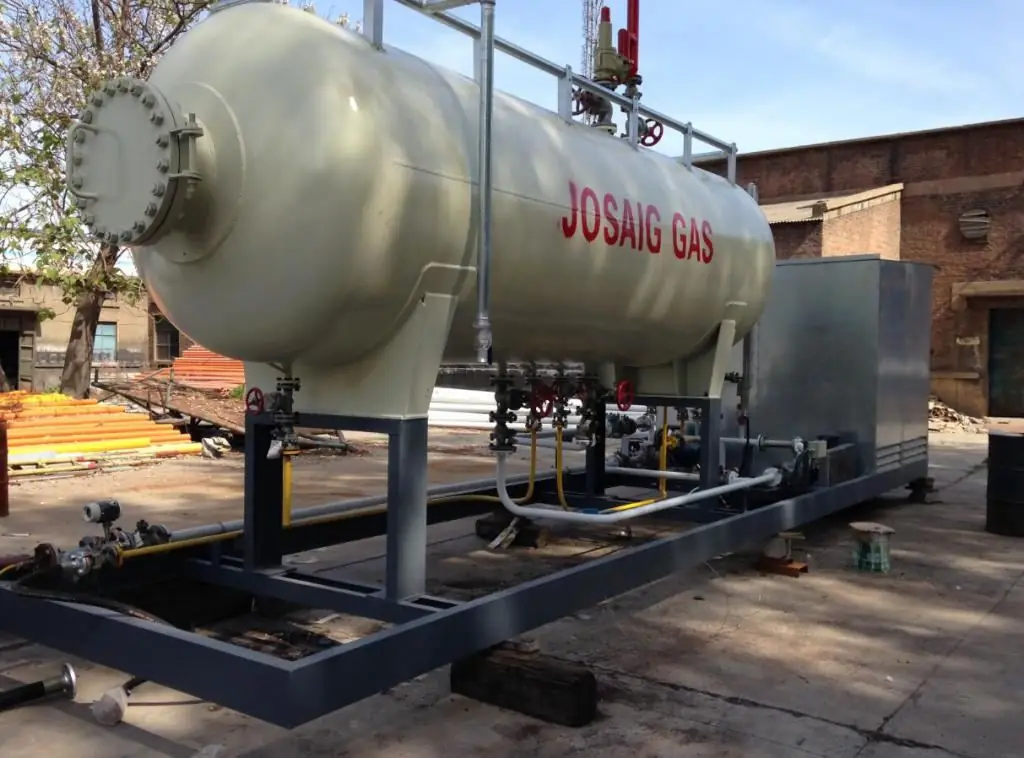
Mobiel tankstation is tegenwoordig een vrij populair bedrijfsidee. Daarom is het behalen van enig succes op dit gebied alleen mogelijk als u maximale aandacht besteedt aan de verschillende hoofdpunten die in dit artikel worden beschreven
Isolatiekleppen - wat is het? Apparaat, toepassing
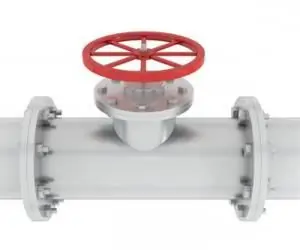
Het concept van "afsluitkleppen" verwijst naar apparaten die de kracht van de stroming van een bepaald medium regelen. Meestal zijn elementen van kleppen aanwezig op pijpleidingen. Vervolgens zullen we begrijpen in welke soorten kleppen is onderverdeeld, wat het is en waar het wordt gebruikt
Wat is radiografisch onderzoek? Radiografische controle van lassen. Radiografische controle: GOST
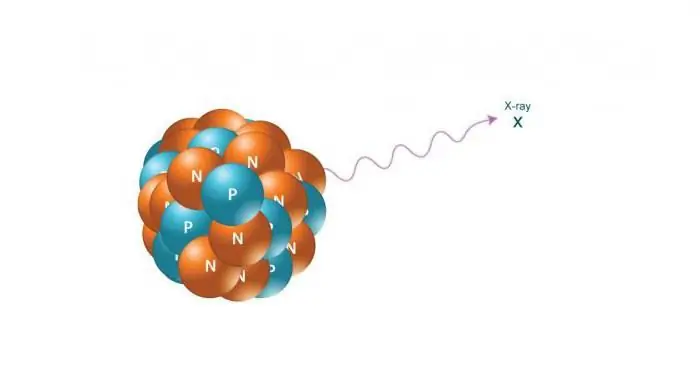
Fysieke basis van methoden voor stralingscontrole. Kenmerken van radiografische controle. De belangrijkste stadia van radiografische controle van lassen. Veiligheidsmaatregelen bij de productie van radiografische controle. Normatieve en technische documentatie