2025 Auteur: Howard Calhoun | [email protected]. Laatst gewijzigd: 2025-01-24 13:22
Het gebruik van investeringsmodellen is een vrij populaire methode van gieterijproductie. De methode onderscheidt zich door de complexiteit van het technologische proces en hoge arbeidskosten voor voorbereidende processen. Daarom wordt het gebruikt waar het nodig is om de afmetingen nauwkeurig in acht te nemen en een hoge kwaliteit van het oppervlak van de onderdelen te garanderen. Dit is hoe turbinebladen en hoogwaardige gereedschappen, kunstgebitten en sieraden worden gegoten, evenals sculpturen met een complexe configuratie. De essentie van verloren-wasgieten is dat de gietvorm uit één stuk bestaat, het model van laagsmeltende materialen wordt niet verwijderd tijdens het gieten, maar wordt gesmolten. Dit zorgt voor een zorgvuldige inachtneming van maatvoering en reliëf. In de holte die overblijft van het model wordt metaal gegoten. Na voltooiing van het afkoelen wordt de mal vernietigd en wordt het product verwijderd. Bij het gieten van grote series worden de productkosten verlaagd.
Methode voordelen
Het belangrijkste voordeel van investeringsgieten is de nauwkeurigheid van de matrijsoverdracht en de lage oppervlakteruwheid. Daarnaast zijn er nog andere voordelen:
- Productie van licht bewerkte legeringsonderdelen beschikbaar.
- Vermindert de noodzaak voor verdere bewerking.
- Producten worden gegoten die anders in delen zouden moeten worden gemaakt en aan elkaar geassembleerd.
- Bij grote series wordt een vermindering van de specifieke arbeidsintensiteit (per product) en de bijbehorende kostprijs bereikt.
- Mogelijkheid tot mechanisatie en gedeeltelijke automatisering van de voorbereidende bewerkingen van het gieten zelf.
Deze voordelen maken de methode een van de meest populaire en gebruikt in de hedendaagse metallurgie, vooral in combinatie met moderne progressieve gietmethodes.
Nadelen van investeringsgieten
De onbetwiste voordelen van de methode, zo lijkt het, hadden ervoor moeten zorgen dat deze overheersend was onder andere methoden. Ondanks de populariteit van de methode voor het gieten van investeringen, hebben nadelen de wijdverbreide toepassing ervan verhinderd. Het grootste nadeel is de complexiteit van het meerfasenproces. Het vereist vrij complexe en dure technologische apparatuur voor de voorbereidende fasen. Voor eenvoudige producten die in kleine batches worden geproduceerd, heeft deze methode hogere kosten.
Voor de kosteneffectieve toepassing van investeringsgieten worden de voor- en nadelen van de methode vergeleken, de beslissing over:haar keuze wordt gemaakt op basis van een beoordeling van de prijs/kwaliteitsverhouding. Daarom wordt het vooral gebruikt voor de meest kritische en dure producten die op een andere manier moeilijk te verkrijgen zijn, zoals turbinebladen, sculpturen, hogesnelheidsgereedschappen, enz. Een ander toepassingsgebied zijn grootschalige gietstukken, in waarbij het schaaleffect het mogelijk maakt om een forse kostenreductie te realiseren.
Technologie
Investeringsgiettechnologie is een meerfasig productieproces dat relatief arbeidsintensief is. In de eerste fase wordt een hoofdmodel gemaakt, het wordt de standaard voor de vervaardiging van werkmodellen nadat het alle stadia van het eindproduct heeft doorlopen. Voor de productie van een mastermodel worden zowel speciale modelcomposities als traditionele - gips of hout - gebruikt. Het materiaal van het hoofdmodel moet kracht en verwerkingsgemak combineren.
Verder zorgt de investeringsgiettechnologie voor het creëren van een mal waarin alle werkende modellen zullen worden gegoten. Mallen zijn gemaakt van gips, rubber, siliconen, minder vaak metaal. Structureel moet het noodzakelijkerwijs verwijderbaar zijn en ontworpen voor herhaald gebruik. De mal wordt gevuld met een modelsamenstelling, nadat deze is uitgehard, wordt deze gedemonteerd en wordt het volgende werkmodel verwijderd.
Bij het produceren van unieke onderdelen of kleine oplagen, worden de fasen van het maken van een masterlay-out en een mal overgeslagen en wordt een lay-out (of meerdere) gemaakt door het materiaal handmatig te vormen.
De volgende stap in het proces van het gieten van investeringen isfabricage rond de lay-out (of blok van lay-outs) van de gietvorm. Deze matrices zijn structureel al niet scheidbaar en wegwerpbaar, waardoor een zorgvuldige naleving van de afmetingen en ruwheid van het product kan worden bereikt. In de moderne industrie worden twee soorten mallen gebruikt - traditionele zand-klei mallen voor het gieten in de grond en schaal mallen - voor de productie van precieze en dure onderdelen.
Nadat de mal is voltooid, wordt het model eruit gesmolten door te verhitten of te blazen met oververhitte stoom. Schelpvormen worden extra versterkt door verhitting tot 1000 ˚С.
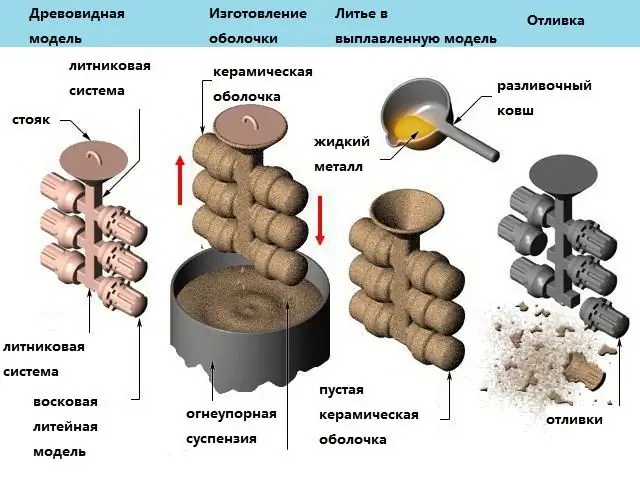
De laatste fase van het proces omvat het daadwerkelijk gieten van het product, het afkoelen in natuurlijke omstandigheden of door een speciale methode in een thermostaat, het vernietigen van de mal en het reinigen van het product. De methode maakt het mogelijk gietstukken van hoge kwaliteit te verkrijgen met een gewicht van enkele grammen tot tientallen kilogrammen.
Modelopstellingen
Het materiaal voor de productie van de lay-out moet bepaalde eigenschappen hebben. Het zou eigenschappen moeten hebben zoals:
- Plasticiteit in de vaste fase. Het is noodzakelijk om de vorm van het toekomstige product nauwkeurig te herhalen en indien nodig te corrigeren.
- Kracht. Het model moet zonder vervorming bestand zijn tegen het proces van het vormen van een vorm eromheen.
- Smeltbaar. Het renderen van een model zou niet veel tijd en energie moeten kosten.
- Gesmolten vloeibaarheid. De compositie zou gemakkelijk in alle uitsparingen en details van het reliëf moeten doordringen, precies de contouren van het toekomstige detail herhalend.
- Economie. Vooral belangrijk voor productie van grote series.
Voor modelsamenstellingen wordt meestal een mengsel van stearine en paraffine gebruikt. Deze materialen vullen elkaars parameters met succes aan en compenseren het onvoldoende smeltpunt van paraffine en de overmatige viscositeit van stearine.
Composities op basis van bruinkoolwas zijn niet minder populair in de industrie. De belangrijkste eigenschappen zijn vochtbestendigheid, sterkte en het vermogen om zeer gladde coatings te vormen, wat vooral waardevol is voor productmodellering.
Verbindingen bestaande uit een mengsel van bruinkoolwas, paraffine en stearine worden ook gebruikt.
Matrijzen maken
Voor de productie van unieke producten wordt een lay-out gemaakt door handmatig of volgens sjablonen een stuk modelmateriaal uit te snijden. Op draaibanken worden ook modellen in de vorm van revolutielichamen gemaakt. Onlangs is de methode van 3D-printen van modellen steeds wijdverbreid geraakt. Het is geschikt voor zowel enkele lay-outs als kleine series.
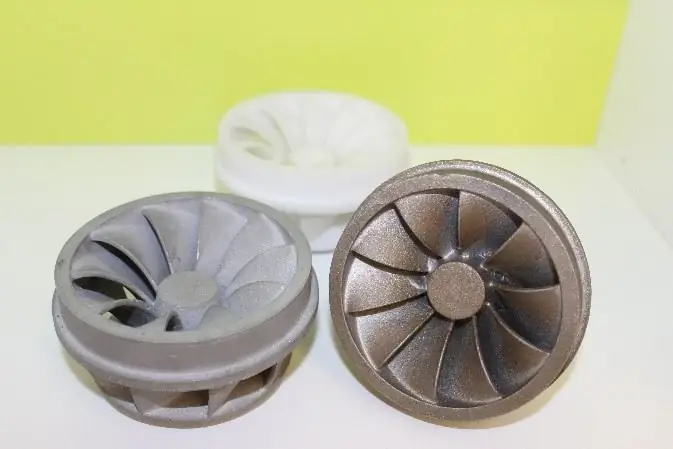
De kosten van een moderne industriële 3D-printer zijn nog steeds hoog, maar door het gemak van herconfiguratie van het ene product naar het andere, kan het een effectief hulpmiddel voor het maken van modellen worden in het geval van een groot aantal heterogene bestellingen in kleine series.
Om een groot aantal identieke lay-outs te maken, wordt een matrix gemaakt van gips, rubber, siliconen of metaal. Werklay-outs worden op hun beurt geproduceerd door in een matrix te gieten. Door het ontwerp moet de mal inklapbaar zijn om de mogelijkheid te bieden om een bepaald aantal modellen te vervaardigen. Het geselecteerde materiaal moet ook een dergelijke mogelijkheid bieden, daarom worden er eisen aan gesteld als sterkte, dichtheid, lage ruwheid en chemische inertie met betrekking tot de lay-out. De malsubstantie moet ook een minimale hechting aan de mock-up hebben om ervoor te zorgen dat de voltooide mock-ups gemakkelijk kunnen worden verwijderd en de afmetingen kunnen worden aangehouden. Een belangrijke eigenschap van de matrijs is de sterkte en slijtvastheid, vooral bij grote series.
Maquettes en blokken maken
Een veelgebruikte methode voor het vervaardigen van investeringsmodellen is ze onder lage druk in mallen te gieten. De injectie van het vloeibare mengsel gebeurt zowel handmatig, met behulp van zuigerspuiten, als mechanische, hydraulische of pneumatische superchargers. In het geval van het gebruik van bruinkoolwas, is het vanwege de hoge viscositeit noodzakelijk om de pijpleidingen te verwarmen voor het toevoeren van de samenstelling. Modellen van geëxpandeerd polystyreen worden gemaakt door extrusie op geautomatiseerde vormmachines.
Om de economische efficiëntie te verhogen en de arbeidsintensiteit te verminderen in het geval van serieproductie van kleine gietstukken, worden hun lay-outs gecombineerd tot blokken. Poortsystemen worden boven de blokken gevormd door individuele lay-outs aan de sprues te bevestigen met behulp van een handsoldeerbout. Bij enkelvoudige gietstukken of kleine series worden de modellen met de hand gemaakt.
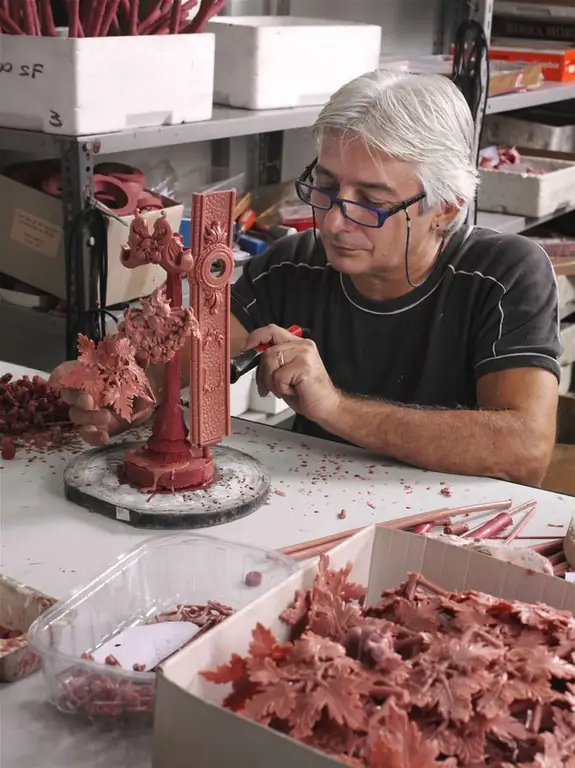
Bij het vormen van poortsystemen is het noodzakelijk om te zorgen voor een niet-turbulente stroom van de smelt, uniforme vulling van alle elementen van de matrix. Bij het invullen van een formulier van PGS moet u ook toezien op de uniforme vulling van alleopeningen tussen sprues en het voorkomen van schade.
Een mal maken
In de beschouwde investeringsgietmethode zijn er twee hoofdtypen mallen:
- Zand-klei mengsels (SGM).
- Shell.
Gegoten was-gietmatrijzen worden voornamelijk gebruikt bij de productie van kleine series producten die geen zeer hoge nauwkeurigheid vereisen. Het fabricageproces is behoorlijk arbeidsintensief en vereist hoge en vaak unieke vaardigheden van modelbouwers en vormers. Gedeeltelijke mechanisatie leent zich alleen voor bepaalde bewerkingen, zoals het voorbereiden en vullen van het vormzand, het aanstampen ervan.
Schaalvormen daarentegen worden gebruikt om onderdelen te produceren die een speciale fabricageprecisie vereisen. Het fabricageproces is complexer en langduriger, maar het leent zich beter voor mechanisatie.
Grond gieten
Dit is de vroegste methode van metaalverwerking die door de mensheid is beheerst. Het werd door onze voorouders beheerst gelijktijdig met het begin van het gebruik van metalen producten als wapens, gereedschappen of gebruiksvoorwerpen, dat wil zeggen ongeveer 5000 jaar geleden. Gesmolten metaal wordt in een voorbereide matrix gegoten uit een mengsel van zand en klei. De vroegste plaatsen voor metaalbewerking ontstonden net waar afzettingen van metalen in de vorm van klompjes en placers in de buurt waren. Een typisch voorbeeld is de Kasli-fabriek in de Oeral, wereldberoemd om zijn ijzeren kantwerk.
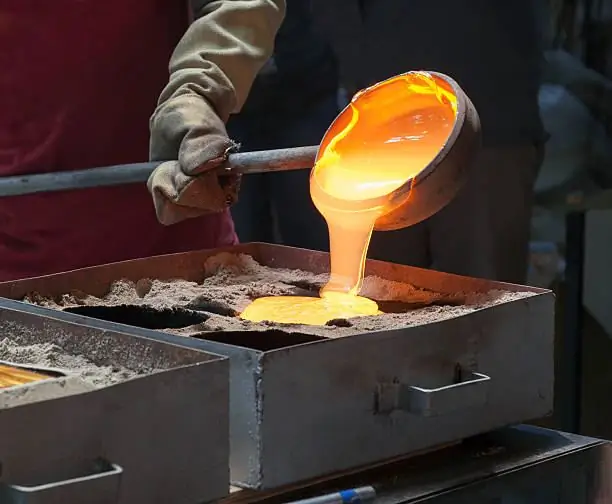
De investeringsgietmethode wordt gebruikt voor de vervaardiging van metalen producten - zowel ferro alsgekleurd. En alleen voor metalen die een verhoogde neiging vertonen om in de vloeibare fase te reageren (zoals titanium), is het nodig om matrices te maken van andere samenstellingen.
Het productieproces van gieten in PGS bestaat uit de volgende fasen:
- modelbouw;
- bereiding van de kolf;
- vulling en verdichting van het mengsel in de kolf;
- metaal gieten;
- het gietstuk verwijderen en schoonmaken.
Formulier van ASG - voor eenmalig gebruik. Om het eindproduct te krijgen, moet het worden gebroken. Tegelijkertijd is het grootste deel van het mengsel beschikbaar voor hergebruik.
Samenstellingen van voornamelijk kwartszand met verschillende korrelgroottes en plastic klei, waarvan het geh alte varieert van 3 tot 45 procent, worden gebruikt als materialen voor ASG. Zo worden bijvoorbeeld kunstgietstukken geproduceerd met een mengsel met een kleigeh alte van 10-20%, voor bijzonder grote gietstukken wordt het kleigeh alte aangepast tot 25%.
Er worden twee subtypes gebruikt:
- Geconfronteerd met mengsels. Ze bevinden zich op het binnenoppervlak van de mal en werken samen met het gesmolten metaal. Ze moeten hittebestendig zijn en niet kunnen worden vernietigd door temperatuurverschillen en de daaruit voortvloeiende spanningen. Deze mengsels hebben een fijne korrel om de details van het oppervlak zorgvuldig over te brengen. Het vermogen van het mengsel om gas door te laten is ook erg belangrijk.
- Vullen van mengsels. Ze worden gebruikt voor opvulling tussen de bekledingslaag en de wanden van de kolf. Ze moeten bestand zijn tegen het gewicht van het gegoten metaal, de vorm van het product behouden en bijdragen aan de tijdige en volledige verwijdering van gassen. Geproduceerd uit goedkopere zandsoorten,herbruikbaar.
Als de gietgassen niet ontsnappen door de massa's van het vormzand, maar door het poortsysteem, treden er defecten op in het gietstuk, wat leidt tot een huwelijk.
De traditionele technologie van in de grond werpen wordt in detail geïllustreerd in A. Tarkovsky's film "Andrei Rublev". In het korte verhaal "The Bell" leidt de jonge man Boriska, de zoon van een overleden meester, een gieterijartel en werpt een kerkklok.
Shell-casting
De methode van investeringsgieten in schaalvormen wordt gekenmerkt door de beste overdracht van productafmetingen en lage oppervlakteruwheid. Het model is gemaakt van smeltbare verbindingen, zoals bruinkoolwas. Gieterijen gebruiken ook op grote schaal de samenstelling van paraffine-stearine in gelijke verhoudingen. Bij gietstukken van grote afmetingen worden zouten in het modelmateriaal opgenomen om het model tegen vervorming te beschermen. Door in de oplossing te dompelen, wordt het model bedekt met 6-10 lagen met een suspensie op hoge temperatuur.
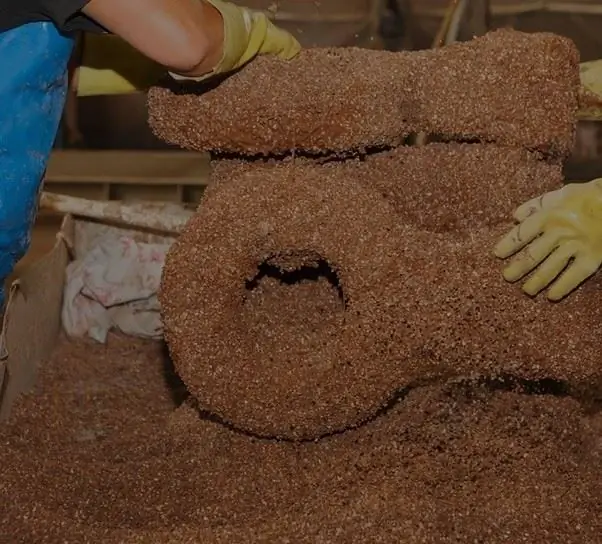
Gehydrolyseerde silicaten werken als bindmiddel, elektrokorund of kwartskristallen worden als hittebestendige beregening beschouwd. Shell-vormmaterialen worden gekenmerkt door hoge sterkte, lage hygroscopiciteit en uitstekende gasdoorlatendheid.
De lay-out wordt gedroogd in een atmosfeer van gasvormige ammoniak. In de volgende fase wordt de mal verwarmd tot 120 ˚C om het paraffinemodel te verwijderen. De resten van het mengsel worden verwijderd met oververhitte stoom onder hoge druk. Vervolgens wordt de mal gecalcineerd bij temperaturen tot 1000 ˚С, wat leidt tot de definitieve fixatie en verwijdering van stoffen,die tijdens het gietproces als gassen kunnen vrijkomen.
De schaal wordt in een soort kolf geplaatst, die is bedekt met stalen kogels. Dit helpt om de configuratie te behouden bij het vullen van de mal met smelt en verbetert tegelijkertijd de omstandigheden voor het koelen van het gietstuk. De smelt wordt in vormen gegoten die tot 1000 zijn verwarmd. Na afkoeling van het product volgens een speciaal programma in een thermostaat, wordt de mal vernietigd, het gietstuk verwijderd en gereinigd.
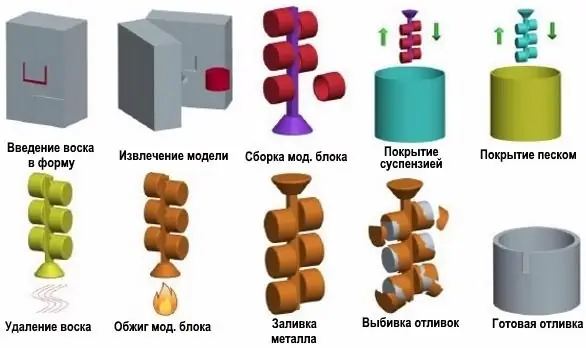
Het belangrijkste voordeel van deze gietmethode is een hoge maatnauwkeurigheid en een lage oppervlakteruwheid.
Extra voordelen van de methode:
- Het gieten van onderdelen van moeilijk te bewerken legeringen.
- Items gieten die anders stuk voor stuk gegoten zouden moeten worden en dan weer in elkaar gezet moeten worden.
De nadelen van deze investeringsgietmethode zijn een laag metaalgebruik en een verhoogde arbeidsintensiteit.
Precisiegieten
Precisie-investeringsgieten - dit is de naam die wordt gegeven aan zowel de technologie als het eindproduct zelf. De hoge nauwkeurigheid van het gieten wordt verzekerd door het feit dat het tijdens de voorbereiding van de mal niet nodig is om het model van het product eruit te extraheren. Bij het gebruik van de traditionele methode is de productie van een gietmatrix een complex en zeer tijdrovend proces in meerdere fasen. Dit geldt met name in het geval van gietdelen met een complexe configuratie, met uitsparingen, verdiepingen en inwendige holtes.
Bij het gieten van een gietijzeren of koperen vaas met een variabele oppervlaktekromming moet je bijvoorbeeld veel trucjes gebruiken. Ja, eerstde onderste helft van de kolf wordt gevuld, dan wordt het model verwijderd, omgedraaid en de bovenste helft wordt geramd. Het model moet composiet worden gemaakt, de handvatten van de vaas zijn gemaakt van twee elementen, ze worden in twee fasen door de modelholte getrokken - eerst het onderste element, dan het bovenste. Al deze talrijke draaien en slepen kunnen geen positief effect hebben op de integriteit van het matrijsoppervlak en uiteindelijk op de nauwkeurigheid van het handhaven van de afmetingen van het gietstuk en de kwaliteit van het oppervlak. Bovendien blijft het probleem bestaan om de delen van de kolven nauwkeurig op elkaar af te stemmen en stevig aan elkaar te bevestigen.
De productie van investeringsgietwerk is verstoken van deze tekortkomingen, het vereist geen hooggekwalificeerde modelbouwers en vermindert de arbeidsintensiteit van pre-casting-operaties aanzienlijk. Dit komt vooral tot uiting bij grote series gietstukken.
De methode maakt het mogelijk om de 2-5e nauwkeurigheidsklasse te bereiken volgens GOST 26645-85. Dit maakt het mogelijk om zeer nauwkeurige producten te gieten, zoals turbinebladen, snijgereedschappen, waaronder hoogwaardige frezen en boren, kritische hoogbelaste beugels, kleine zwaarbelaste onderdelen van voertuigen, werktuigmachines en andere complexe mechanismen.
Hoge maatnauwkeurigheid en hoge oppervlakteklasse minimaliseren de noodzaak voor verdere bewerking van het gietstuk, wat metaal bespaart en de productiekosten verlaagt.
Apparatuur
De benodigde apparatuur voor het gieten van investeringen is gevarieerd en complex. Ondernemingen combineren ze tot één goed gecoördineerd complex,georganiseerd als een site, workshop of afzonderlijke productie.
De samenstelling van het complex hangt af van de productieschaal, grootte, configuratie en circulatie van gietstukken.
Bij de productie van kunstgebitten en sieraden omvat de uitrusting dus:
- model tafel;
- moffeloven met thermostaat;
- een set scalpels en spatels om de vorm van het model te corrigeren;
- vormbord;
- kolf;
- tanks voor het opslaan en bereiden van vormzand;
- set zandstampergereedschappen;
- kroes voor het smelten van metaal;
- pincet;
- hamer om de mal te breken.
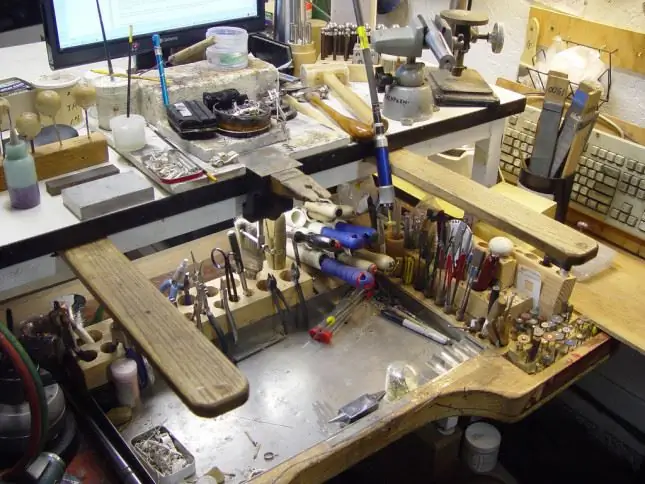
Dit productiecomplex past gemakkelijk op één tafel en in één kast. Als het de bedoeling is om in massaproductie te gaan, bijvoorbeeld aluminium gietstukken - onderdelen van een apparaat, dan is apparatuur vereist voor:
- vormen en gieten van keramische mallen;
- droogvormen;
- het modelmateriaal uitsmelten en een hittebestendige laag aanbrengen;
- gietstukken reinigen van gietmateriaal.
En tot slot, de eigenlijke uitrusting van het gieterijcomplex, ontworpen om een smelt te verkrijgen en in een mal te gieten. Het kan gietapparatuur zijn:
- onder lage druk;
- centrifugaal;
- op de gebruikelijke manier van zwaartekracht.
Spuitgiet- en centrifugaalgietmachines zijn een afzonderlijke, sterk gemechaniseerde en geautomatiseerdeproductiecomplex, geïsoleerd van de sfeer van de winkel. Ze minimaliseren handarbeid en menselijke blootstelling aan schadelijke omstandigheden. Afgesloten kamers waarin de complexen zich bevinden, zorgen voor een volledige opvang en zuivering van uitlaatgassen, wat de milieuvriendelijkheid van de onderneming aanzienlijk verhoogt.
Lost-wax casting heeft een vrij hoog ontwikkelingspotentieel, vooral in combinatie met geavanceerde matrijzenbouw- en giettechnieken.
Aanbevolen:
Beleggen in beleggingsfondsen: winstgevendheid, voor- en nadelen. Regels voor beleggingsfondsen
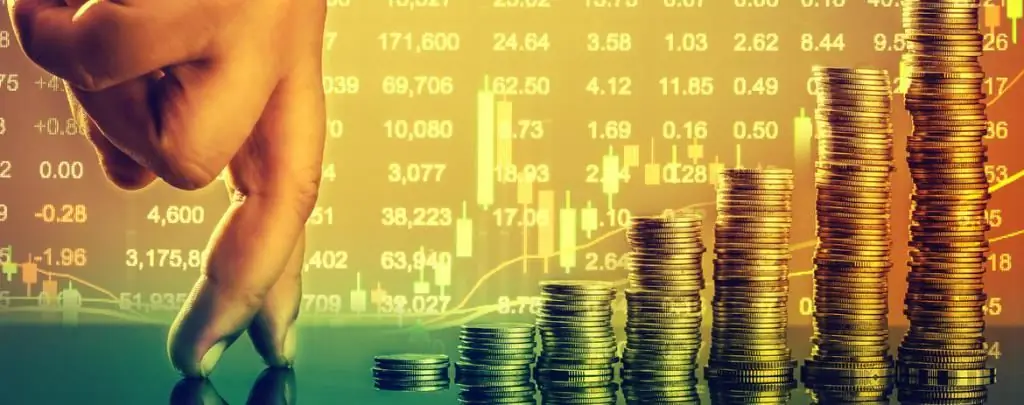
Zo'n interessant financieel instrument als een beleggingsfonds (ook bekend als beleggingsfonds) verscheen relatief recent op het grondgebied van de voormalige Sovjet-Unie. En, het moet worden opgemerkt, onder de algemene bevolking is over hen niet erg bekend. Daarom wordt in het kader van het artikel gezocht naar het antwoord op één vraag: wat zijn beleggingsfondsen?
Indicatoren voor scalperen zonder opnieuw te tekenen: kenmerken, voor- en nadelen
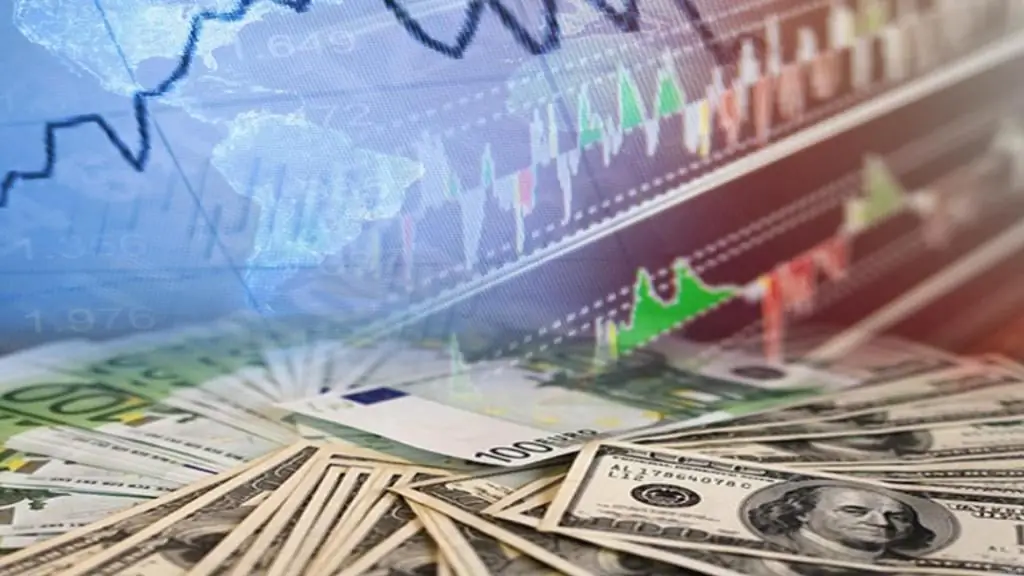
Bij het handelen op de financiële markten zijn er verschillende methoden waarmee handelaren verdienen. Elk handelssysteem heeft zijn eigen kenmerken en kenmerken, en de meeste gebruiken speciale tools. In dit artikel leert de lezer over verschillende soorten handelshulpmiddelen, inclusief indicatoren voor "Scalperen" zonder opnieuw te tekenen
Plexiglas graveren: voor- en nadelen, technologie, apparatuur
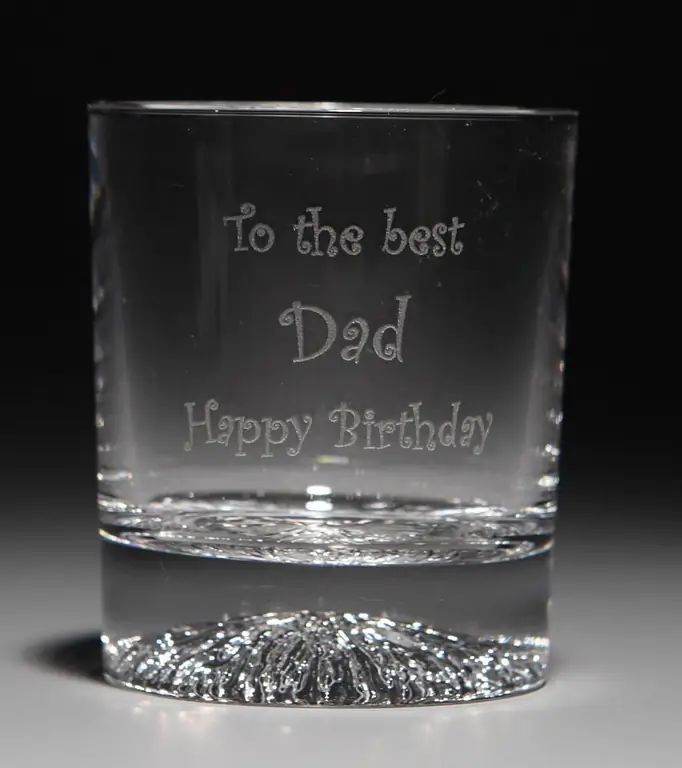
Gravure van plexiglas wordt beschouwd als een ambacht van schilderen. Een souvenirbeeldje, glas-in-loodramen of een glazen tafel, versierd met prachtige tekeningen, belichamen een delicate artistieke smaak. Beits- en zandstra altechnologieën behoren tot het verleden. Tegenwoordig kan iedereen met behulp van een lasermachine een zeer gedetailleerd patroon maken
Ultrasone verwerking: technologie, voor- en nadelen
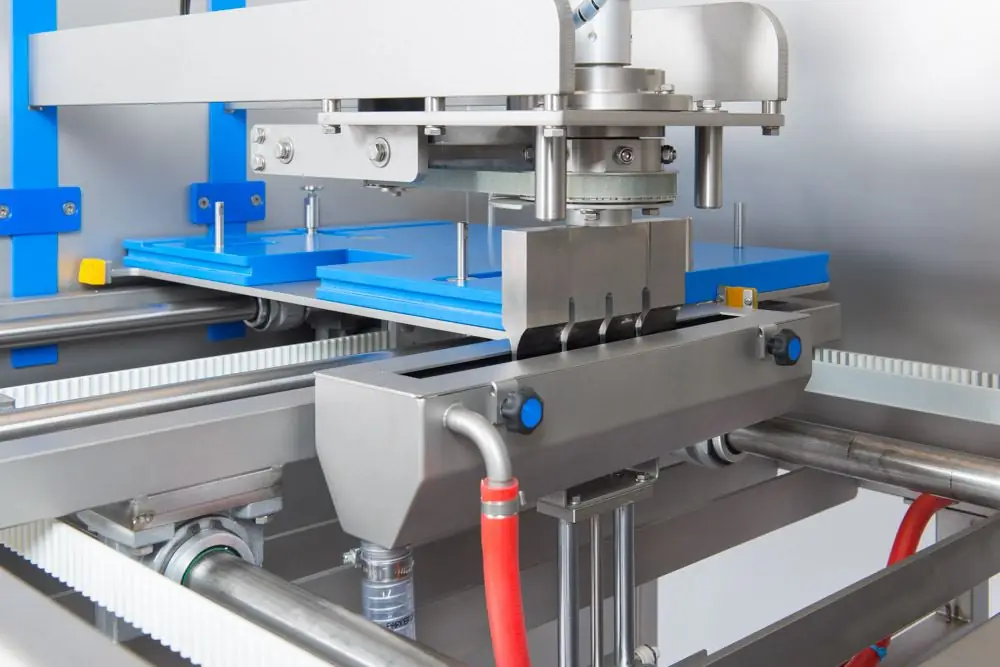
De metaalverwerkende industrie is in dit ontwikkelingsstadium in staat om de complexe taken van het snijden en boren van werkstukken van verschillende hardheidsgraden op te lossen. Dit werd mogelijk door de ontwikkeling van fundamenteel nieuwe manieren om het materiaal te beïnvloeden, waaronder een brede groep van elektromechanische methoden. Een van de meest effectieve technologieën van dit type is ultrasone behandeling (UZO), gebaseerd op de principes van elektroakoestische straling
Kamerdrogen van hout: technologie, voor- en nadelen
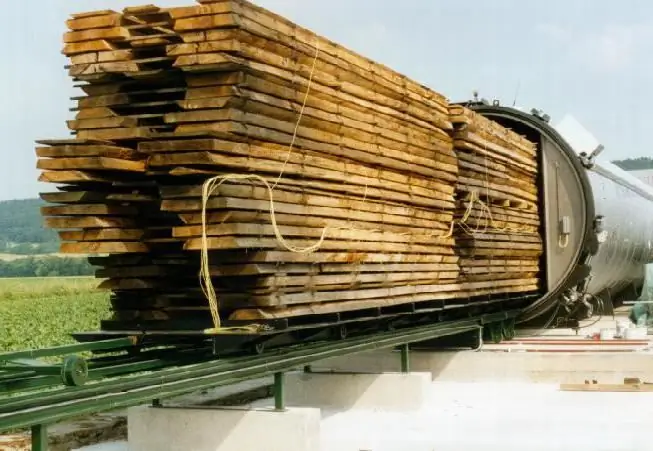
Het artikel is gewijd aan het drogen van hout in de kamer. De droogtechnologie, stadia en hoofdbewerkingen, evenals de voor- en nadelen ervan, worden overwogen