2025 Auteur: Howard Calhoun | [email protected]. Laatst gewijzigd: 2025-01-24 13:22
Lean productie is een speciaal schema van bedrijfsmanagement. Het belangrijkste idee is om er constant naar te streven om elke vorm van kosten te elimineren. Lean manufacturing is een concept waarbij elke medewerker wordt betrokken bij de optimalisatieprocedure. Een dergelijke regeling is gericht op een maximale oriëntatie op de consument. Laten we eens nader bekijken wat een lean manufacturing-systeem is.
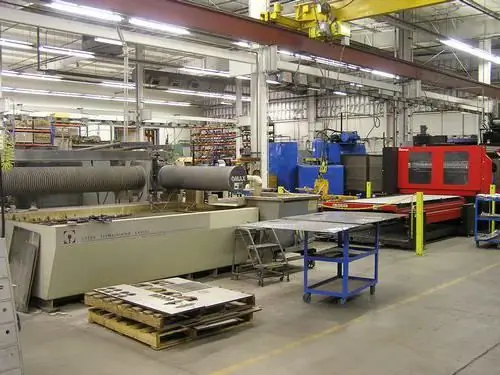
Geschiedenis van voorkomen
De introductie van lean manufacturing in de industrie vond plaats in de jaren vijftig bij de Toyota Corporation. De maker van een dergelijk controleschema was Taiichi Ohno. Een grote bijdrage aan de verdere ontwikkeling van zowel theorie als praktijk werd geleverd door zijn collega Shigeo Shingo, die onder meer een methode creëerde voor snelle omschakeling. Vervolgens hebben Amerikaanse specialisten het systeem onderzocht en geconceptualiseerd onder de naam lean manufacturing (lean production) - "lean production". Aanvankelijk werd het concept vooral toegepast in de auto-industrie. Na een tijdje werd het schema aangepast aan het procesproductie. Vervolgens werden lean manufacturing-tools gebruikt in de gezondheidszorg, nutsbedrijven, diensten, handel, het leger, de overheid en andere industrieën.
Hoogtepunten
Lean productie bij de onderneming omvat de analyse van de waarde van het product dat wordt geproduceerd voor de eindverbruiker, in elke fase van creatie. Het hoofddoel van het concept is de vorming van een continu proces van kosteneliminatie. Met andere woorden, lean manufacturing is de eliminatie van elke activiteit die hulpbronnen verbruikt maar geen waarde creëert voor de eindgebruiker. Zo hoeft hij het eindproduct of de onderdelen daarvan niet op voorraad te hebben. In het traditionele systeem worden alle kosten in verband met huwelijk, herbewerking, opslag en andere indirecte kosten doorberekend aan de consument. Lean manufacturing is een schema waarin alle bedrijfsactiviteiten zijn onderverdeeld in processen en operaties die wel en geen waarde toevoegen aan het product. De belangrijkste taak is daarom de systematische vermindering van deze laatste.
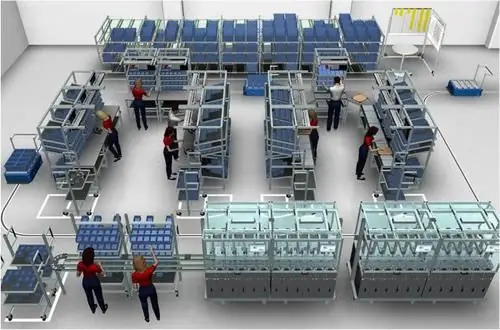
Lean waste
Als synoniem voor kosten wordt soms de term muda gebruikt. Dit concept betekent verschillende uitgaven, afval, afval enzovoort. Taiichi Ohno identificeerde zeven soorten kosten. Verliezen worden gegenereerd door:
- wacht;
- overproductie;
- verzending;
- extra verwerkingsstappen;
- onnodige bewegingen;
- defecte goederen vrijgeven;
- overtollige voorraad.
Het belangrijkste type verliezen Taiichi Ohno beschouwde overproductie. Het is een factor waardoor andere kosten ontstaan. Er is weer een item toegevoegd aan de bovenstaande lijst. Jeffrey Liker, een onderzoeker naar de Toyota-ervaring, noemde het niet-gerealiseerde potentieel van werknemers als een verspilling. De bronnen van kosten zijn overbelaste capaciteit, medewerkers bij het uitvoeren van activiteiten met verhoogde intensiteit, evenals de ongelijkmatigheid van de uitvoering van de operatie (bijvoorbeeld een onderbroken schema door fluctuaties in de vraag).
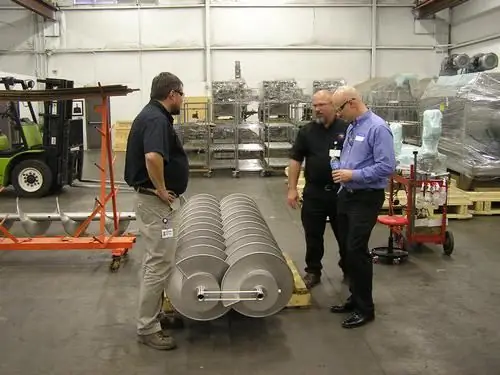
Principes
Lean manufacturing wordt gepresenteerd als een proces dat is verdeeld in vijf fasen:
- Bepalen van de waarde van een bepaald product.
- Stel de waardestroom van dit product in.
- Zorgen voor een continue stroom.
- De consument in staat stellen om aan het product te trekken.
- Streven naar uitmuntendheid.
Onder andere principes waarop lean manufacturing is gebaseerd, moeten we het volgende benadrukken:
- Uitstekende kwaliteit bereiken - op het eerste gezicht, nul defecten, problemen in een vroeg stadium identificeren en oplossen.
- Het creëren van een langdurige relatie met de consument door het delen van informatie, kosten en risico's.
- Flexibiliteit.
Productiesysteem,gebruikt in Toyota is gebaseerd op twee hoofdprincipes: verzelfstandiging en "just in time". Dit laatste betekent dat alle benodigde elementen voor de assemblage precies op het moment dat het nodig is op de lijn arriveren, strikt in de hoeveelheid die is bepaald voor een bepaald proces om de voorraad te verminderen.
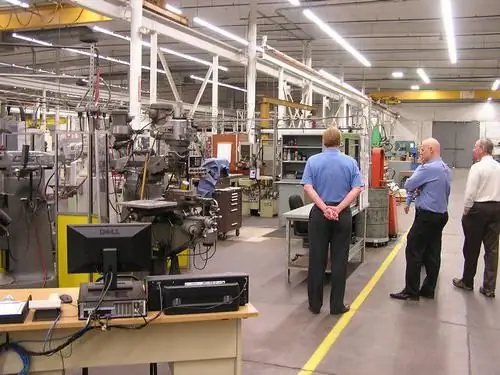
Compositie-elementen
In het kader van het beschouwde concept worden verschillende componenten onderscheiden - methoden van lean productie. Sommigen van hen kunnen zelf als controleschema fungeren. De belangrijkste elementen zijn de volgende:
- Stroom van één item.
- Algemene verzorging van apparatuur.
- 5S systeem.
- Kaizen.
- Snelle omschakeling.
- Foutpreventie.
Industrie-opties
Lean-gezondheidszorg is een concept van het verminderen van de tijd die medisch personeel besteedt aan het helpen van mensen. Lean logistiek is een pull-schema dat alle leveranciers samenbrengt die betrokken zijn bij de waardestroom. In dit systeem is er een gedeeltelijke aanvulling van reserves in kleine volumes. De belangrijkste indicator in dit schema zijn de logistieke totale kosten. Lean manufacturing tools worden gebruikt door het Deense postkantoor. Als onderdeel van het concept is een grootschalige standaardisatie van de aangeboden diensten doorgevoerd. De doelstellingen van het evenement waren om de productiviteit te verhogen en de overdrachten te versnellen. "Kaarten van in-line waardevorming" werden geïntroduceerddiensten te controleren en te identificeren. Ook is een motivatiesysteem voor medewerkers van de afdeling ontwikkeld en vervolgens geïmplementeerd. In de bouw is een speciale strategie gevormd, gericht op het verhogen van de efficiëntie van het bouwproces in alle stadia. Lean manufacturing principes zijn aangepast aan softwareontwikkeling. Elementen van het overwogen schema worden ook gebruikt in stads- en staatsbestuur.
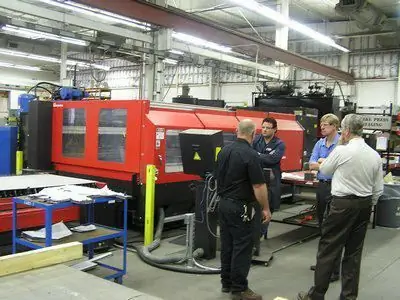
Kaizen
Het idee werd in 1950 geformuleerd door Dr. Deming. De introductie van dit principe heeft Japanse bedrijven grote winsten opgeleverd. Hiervoor kreeg de specialist een medaille van de keizer. Na een tijdje kondigde de Union of Science and Technology of Japan een prijs aan hen aan. Deming voor de kwaliteit van gefabriceerde goederen.
Voordelen van Kaizen-filosofie
De verdiensten van dit systeem zijn geëvalueerd in elke industriële sector, waar voorwaarden zijn gecreëerd om de hoogste efficiëntie en productiviteit te garanderen. Kaizen wordt beschouwd als een Japanse filosofie. Het bestaat uit het bevorderen van continue verandering. De Kaizen-school houdt vol dat constante verandering de enige weg naar vooruitgang is. De nadruk van het systeem ligt op het verhogen van de productiviteit door onnodig en zwaar werk te elimineren. De definitie zelf is gemaakt door twee woorden te combineren: "kai" - "veranderen" ("transformeren") en "zen" - "in de richting van het betere". De voordelen van het systeem weerspiegelen duidelijk het succes van de Japanse economie. Dit wordt niet alleen door de Japanners zelf erkend, maar ook door expertsvrede.
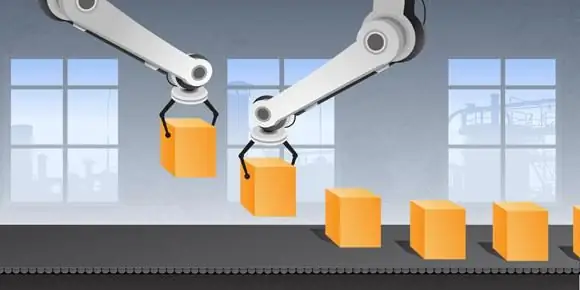
Kaizen Concept Doelen
Er zijn vijf hoofdrichtingen waarin de ontwikkeling van de productie wordt uitgevoerd. Deze omvatten:
- Afvalvermindering.
- Onmiddellijke probleemoplossing.
- Optimaal gebruik.
- Teamwerk.
- Topkwaliteit.
Het moet gezegd worden dat de meeste principes gebaseerd zijn op gezond verstand. De belangrijkste componenten van het systeem zijn het verbeteren van de kwaliteit van goederen, het betrekken van elke medewerker bij het proces, de bereidheid tot interactie en verandering. Al deze activiteiten vereisen geen complexe wiskundige berekeningen of het zoeken naar wetenschappelijke benaderingen.
Afvalvermindering
De principes van de Kaizen-filosofie zijn gericht op het aanzienlijk verminderen van verliezen in elke fase (operatie, proces). Een van de belangrijkste voordelen van de regeling is dat elke werknemer er bij betrokken is. Dit omvat op zijn beurt het ontwikkelen en vervolgens implementeren van verbetervoorstellen op elk managementniveau. Dergelijk werk draagt bij aan het minimaliseren van het verlies van middelen.
Onmiddellijke probleemoplossing
Elke medewerker moet, in overeenstemming met het concept van kaizen, problemen tegengaan. Dit gedrag draagt bij aan de snelle oplossing van problemen. Bij onmiddellijke probleemoplossing loopt de doorlooptijd niet op. Onmiddellijke oplossing van problemen stelt u in staat om activiteiten in een effectieve richting te sturen.
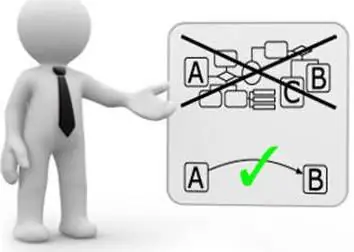
Optimaal gebruik
Bronnen komen vrij wanneer problemen snel worden opgelost. Ze kunnen worden gebruikt om andere doelen te verbeteren en te bereiken. Samen maken deze maatregelen het mogelijk om een continu proces van efficiënte productie tot stand te brengen.
Teamwerk
Door alle medewerkers te betrekken bij het oplossen van problemen, vind je sneller een uitweg. Het succesvol overwinnen van moeilijkheden versterkt de geest en het zelfrespect van de medewerkers van het bedrijf. Teamwerk elimineert conflictsituaties, bevordert de vorming van vertrouwensrelaties tussen hogere en lagere werknemers.
Beste kwaliteit
Snelle en efficiënte probleemoplossing draagt bij aan teamwork en het creëren van een grote hoeveelheid middelen. Dit zal op zijn beurt de kwaliteit van de producten verbeteren. Dit alles zal het bedrijf in staat stellen een nieuw capaciteitsniveau te bereiken.
Aanbevolen:
Moderne productie. De structuur van de moderne productie. Problemen van moderne productie

Ontwikkelde industrie en een hoog niveau van de economie van het land zijn sleutelfactoren die de rijkdom en het welzijn van de mensen beïnvloeden. Zo'n staat heeft grote economische kansen en potentieel. Een belangrijk onderdeel van de economie van veel landen is de productie
Soorten verspilling in lean manufacturing
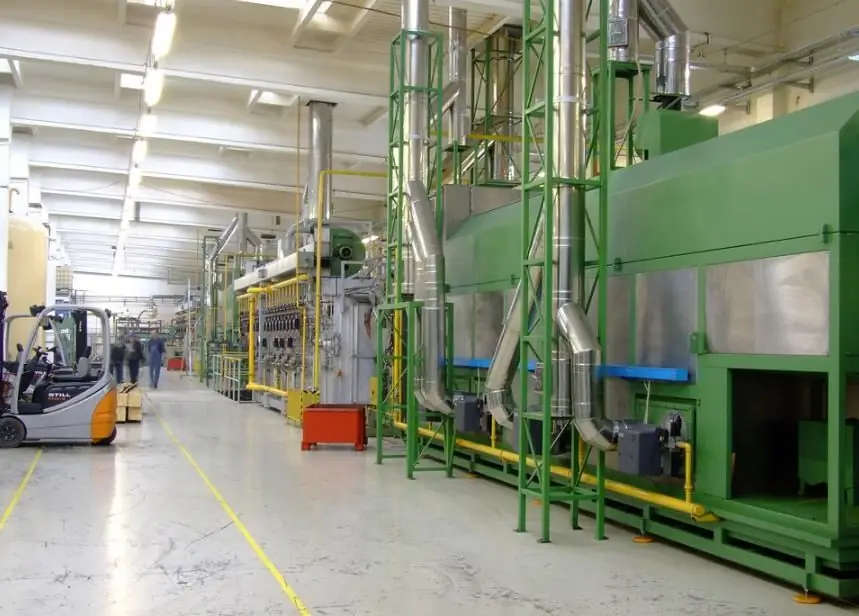
Lean Manufacturing, ook wel bekend als Lean Manufacturing, of LEAN, is een van de beste oplossingen voor organisaties die de productiviteit willen verhogen en de kosten zo laag mogelijk willen houden. Verspilling in Lean-productie interfereert met het bereiken van de belangrijkste doelen van het Lean-systeem. Door de soorten verliezen te kennen, hun bronnen en manieren om ze te elimineren te begrijpen, kunnen fabrikanten het productieorganisatiesysteem dichter bij ideale omstandigheden brengen
Ideeën mini-productie. Miniwinkel voor kleine bedrijven. productie in de garage
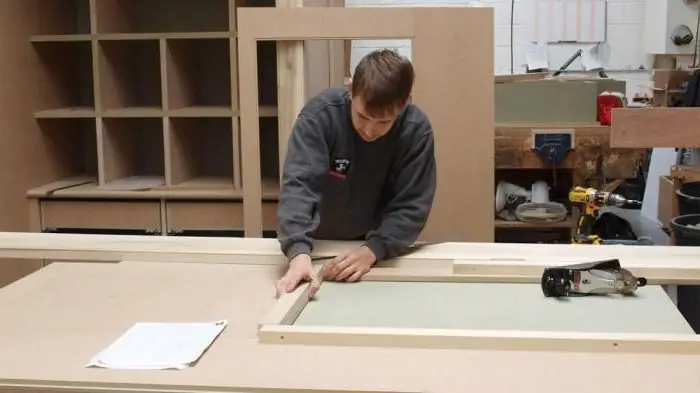
Wat kan er thuis of in de garage geproduceerd worden? Wij organiseren uw bedrijf van de grond af met minimale investering
Bedrijfsidee: productie van bakstenen. Technologie en installatie voor de productie van bakstenen
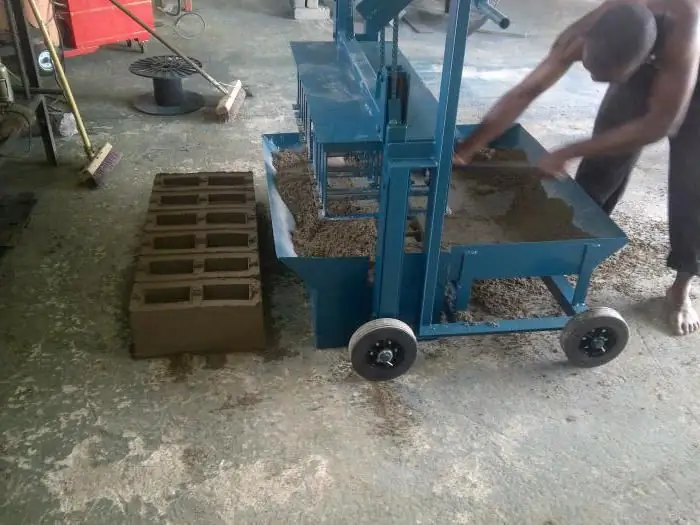
U kunt uw eigen bedrijf opzetten dat aan uw eisen voldoet en ook een bron van inkomsten wordt. Om stenen van hoge kwaliteit te verkrijgen, is het echter noodzakelijk om te voldoen aan de technische voorwaarden en het fabricageproces te volgen. De productie van bakstenen thuis vereist geen gebruik van dure apparatuur. De belangrijkste voorwaarde is de juiste voorbereiding van grondstoffen
De voorman is het hoofd van de productie. Wat zijn zijn rechten en plichten?
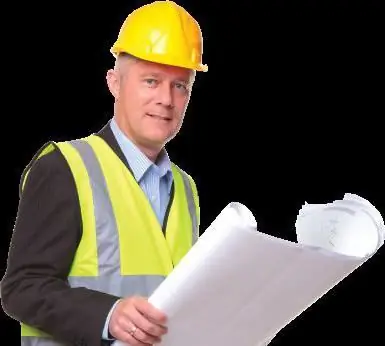
De voorman is een manager, zonder wie het werkproces in productie- en bouworganisaties onmogelijk is voor te stellen. De omvang van zijn taken wordt duidelijk omschreven door de functiebeschrijving, waarvan de naleving en uitvoering garant staat voor vlot werk