2025 Auteur: Howard Calhoun | [email protected]. Laatst gewijzigd: 2025-01-24 13:22
Koper en zijn legeringen worden gebruikt in verschillende sectoren van de economie. Er is veel vraag naar dit metaal vanwege zijn fysisch-chemische eigenschappen, die ook de verwerking van de structuur bemoeilijken. Met name het lassen van koper vereist speciale omstandigheden, hoewel het proces is gebaseerd op vrij gebruikelijke thermische behandelingstechnologieën.
Specifiek lassen van koperen blanks
In tegenstelling tot veel andere metalen en legeringen, worden koperproducten gekenmerkt door een hoge thermische geleidbaarheid, waardoor het noodzakelijk is om het thermische vermogen van de lasboog te vergroten. Tegelijkertijd is een symmetrische warmteafvoer uit het werkgebied vereist, waardoor het risico op defecten wordt geminimaliseerd. Een ander nadeel van koper is de vloeibaarheid. Deze eigenschap wordt een obstakel bij de vorming van plafond- en verticale naden. Bij grote smeltbaden zijn dergelijke bewerkingen helemaal niet mogelijk. Zelfs kleine werkvolumes vereisen de organisatie van speciale voorwaarden met het gebruik van beperkende voeringen op basis van grafieten asbest.
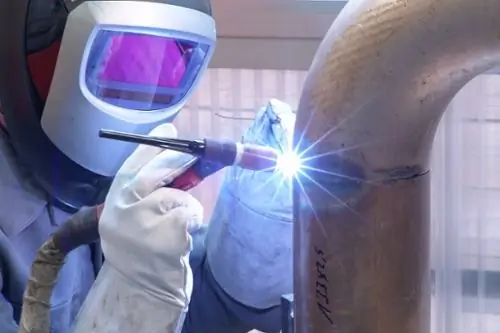
De neiging van het metaal om te oxideren vereist ook dat speciale additieven zoals silicium, mangaan en fosforgels in sommige modi worden gebruikt met de vorming van vuurvaste oxiden. De kenmerken van koperlassen omvatten de absorptie van gassen - bijvoorbeeld waterstof en zuurstof. Als u niet de optimale modus voor thermische blootstelling kiest, zal de naad van slechte kwaliteit blijken te zijn. Grote poriën en scheuren blijven in de structuur achter door actieve interactie met gas.
Interactie van koper met onzuiverheden
Het is noodzakelijk om rekening te houden met de aard van de interactie van koper met verschillende onzuiverheden en chemische elementen in het algemeen, omdat bij het lassen van dit metaal vaak elektroden en draden van verschillende materialen worden gebruikt. Aluminium kan bijvoorbeeld oplossen in een kopersmelt, waardoor de anticorrosie-eigenschappen toenemen en de oxideerbaarheid wordt verminderd. Beryllium - verhoogt de mechanische weerstand, maar vermindert de elektrische geleidbaarheid. De specifieke effecten zullen echter ook afhangen van de aard van de beschermende omgeving en het temperatuurregime. Dus het lassen van koper bij 1050 °C zal het binnendringen van de ijzercomponent in de structuur van het werkstuk vergemakkelijken met een coëfficiënt van ongeveer 3,5%. Maar in een regime van ongeveer 650 ° C zal dit cijfer worden teruggebracht tot 0,15%. Tegelijkertijd vermindert ijzer als zodanig de corrosieweerstand, elektrische en thermische geleidbaarheid van koper sterk, maar verhoogt het de sterkte ervan. Van de metalen die dergelijke werkstukken niet aantasten, kunnen lood en zilver worden onderscheiden.
Basismethoden voor koperlassen
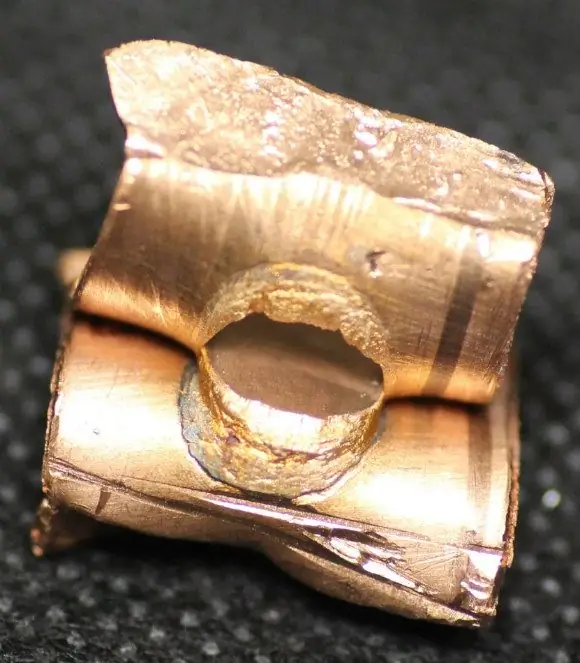
Alle gangbare lasmethoden, inclusief handmatig en automatisch, zijn toegestaan in verschillende configuraties. De keuze voor een of andere methode wordt bepaald door de vereisten voor de verbinding en de kenmerken van het werkstuk. Een van de meest productieve processen zijn elektroslak en booglassen onder water. Als het de bedoeling is om in één keer een hoogwaardige naad te verkrijgen, is het raadzaam om gastechnologie te gebruiken. Deze benadering van het lassen van koper en zijn legeringen bij lage temperatuurgradiënten creëert gunstige omstandigheden voor deoxidatie en legering van het werkstuk. Hierdoor is de naad positief gemodificeerd en duurzaam. Voor zuiver koper kunnen booglastechnieken met wolfraamelektroden en beschermgassen worden gebruikt. Maar meestal werken ze met koperderivaten.
Welke apparatuur wordt er gebruikt?
Pre-koper producten kunnen worden verwerkt op draai-, slijp- en freesmachines om dimensionale blanks te vormen voor het lassen. De industrie gebruikt ook de plasmaboogsnijtechniek, die snijden met bijna perfecte snijkanten mogelijk maakt. Direct lassen van koper wordt uitgevoerd door argon-booginstallaties, halfautomatische apparaten en inverterapparaten. De stroomsterkte van de apparatuur kan variëren van 120 tot 240 A, afhankelijk van de grootte van het werkstuk. De dikte van de elektroden is meestal 2,5-4 mm - nogmaals, het hangt af van de complexiteit en het volume van het werk.
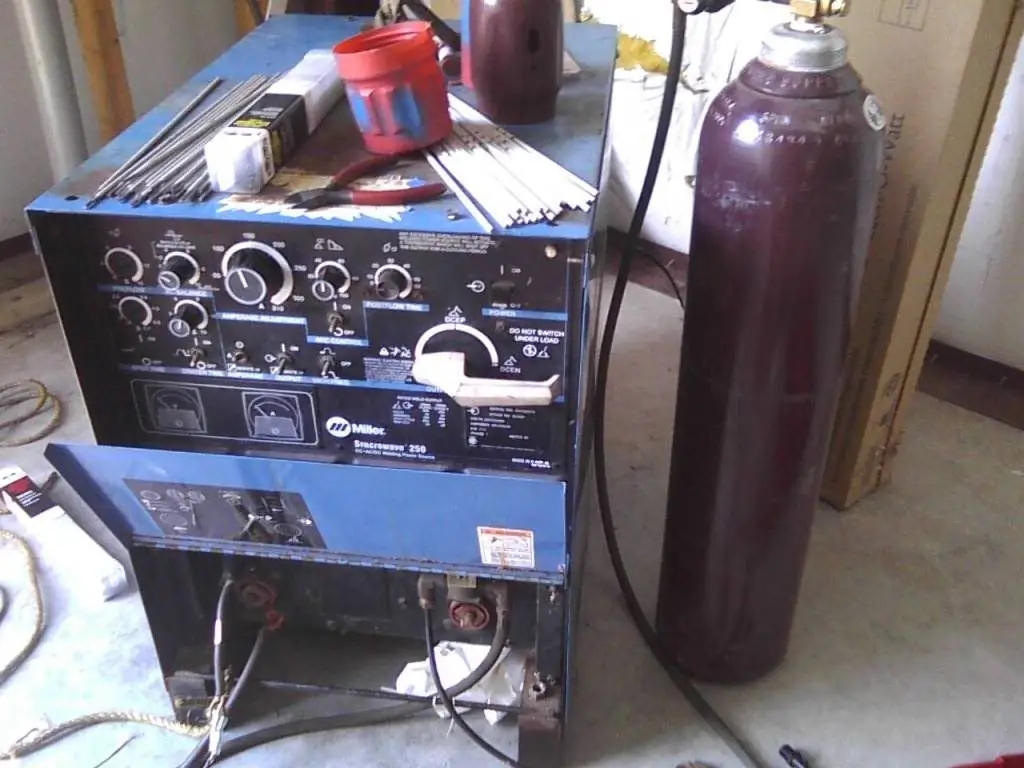
Koper argon lassen
Een van de meest populaire methoden. Met name de genoemde techniek van argon-booglassen, waarbij gebruik wordt gemaakt van wolfraamelektroden, wordt gebruikt. Tijdens het verwarmen interageert koper met zuurstof, waardoor een dioxidecoating op het oppervlak van het werkstuk wordt gevormd. In dit stadium wordt het werkstuk buigzaam en vereist de aansluiting van een niet-verbruikbare elektrode. Zo zorgen staven van het merk MMZ-2 voor een optimale laskwaliteit bij het lassen van koper met argon met beschermende media. Als de taak van een sterke penetratie van het werkstuk niet is ingesteld, kan een lichtgewicht versie van lassen in een stikstofomgeving worden gebruikt. Dit is een goede methode van thermische werking bij lage spanningen, maar een nog groter effect in termen van laskwaliteit kan worden bereikt met gecombineerde gassen. Ervaren lassers gebruiken bijvoorbeeld vaak mengsels die voor 75% uit argon bestaan.
Gaslassen
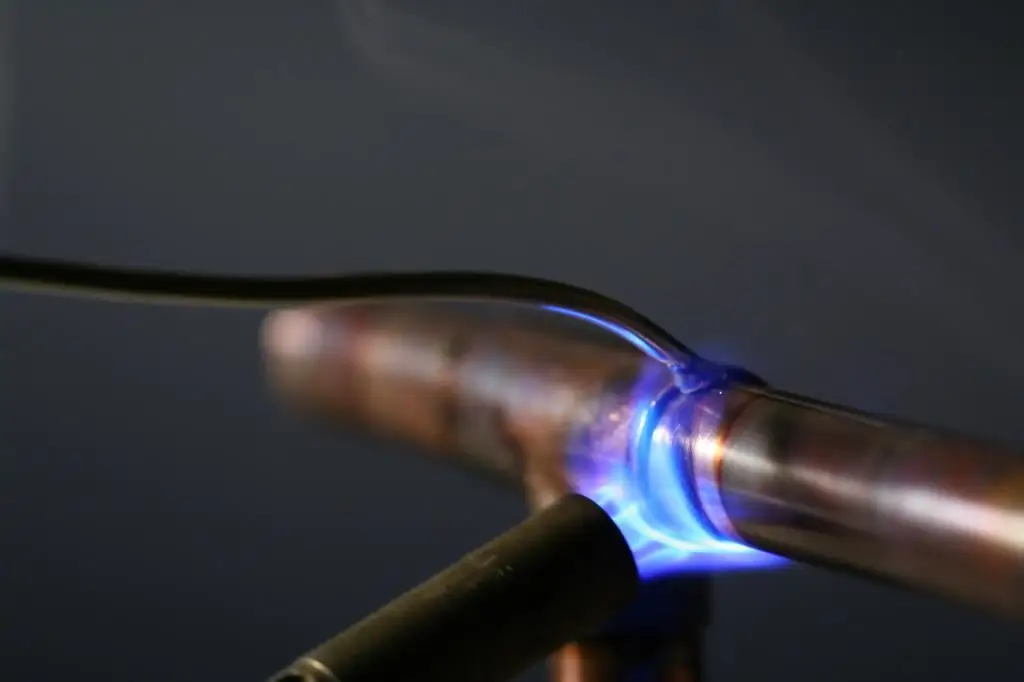
In dit geval wordt een zuurstof-acetyleenmedium gebruikt, waardoor de vlamtemperatuur aanzienlijk stijgt. In het werkproces wordt een gasbrander gebruikt. Deze machine presteert goed, maar dankzij de beperkte instelmogelijkheden kunt u de parameters van het smeltbad niet nauwkeurig afstemmen.
Vaak gebruikt en de methode van verdeelde thermische blootstelling met de aansluiting van twee branders. De ene dient om het werkgebied op te warmen en de tweede - direct voor het gaslassen van het doelwerkstuk. Deze aanpak wordt aanbevolen voor dikke platen van 10 mm. Als er geen tweede brander is,dan kunt u dubbelzijdig verwarmen langs de lijn van de toekomstige naad. Het effect is niet zo hoogstaand, maar de hoofdtaak wordt gerealiseerd.
Maakt gaslastechniek en fluxinjectie mogelijk om een schone verbindingsstructuur te verkrijgen. In het bijzonder worden gasvormige vloeimiddelen gebruikt, zoals azeotrope oplossingen van boormethylether met methyl. De actieve dampen van dergelijke mengsels worden naar de brander gestuurd, waardoor de eigenschappen van het smeltbad worden gewijzigd. De vlam krijgt op dit punt een groenachtige tint.
Kenmerken van lassen met koolstofelektroden
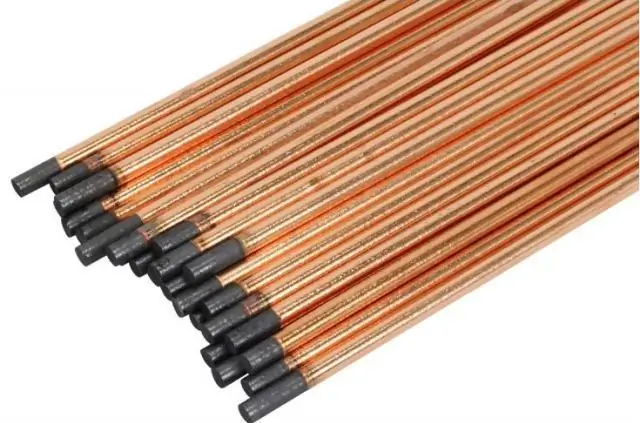
Booglasmethode die optimaal is voor koperlegeringen. Het belangrijkste onderscheidende kenmerk kan ergonomie en veelzijdigheid worden genoemd - althans in alles wat te maken heeft met de mechanica van het uitvoeren van fysieke acties door de operator. Een lasser kan bijvoorbeeld manipulaties direct in de lucht uitvoeren met een minimale set aanvullende beschermingsmiddelen. Dit komt door het feit dat koolstofelektroden tijdens het verwarmingsproces voldoende thermische energie afgeven, waarop koper met een laag vermogen wordt gelast. Het proces blijkt inefficiënt, maar de verbinding krijgt alle benodigde mechanische eigenschappen.
Handmatig booglassen
De technologie van deze lasmethode omvat het gebruik van gecoate elektroden. Dit betekent dat de verbinding behoorlijke sterkte-eigenschappen zal krijgen, maar de samenstelling van de productstructuur zal uiteindelijk verschillen van het primaire werkstuk. Specifieke modificatieparameters worden bepaald door de eigenschappen van legeringsdeoxidatiemiddelen,die aanwezig zijn in de elektrodecoating. In de actieve samenstelling kunnen bijvoorbeeld componenten worden gebruikt zoals koolstofarm ferromangaan, vloeispaat, aluminiumpoeder, enz. Deze koperlastechnologie en onafhankelijke productie van coatings maken het mogelijk. Meestal wordt hiervoor een droog mengsel gebruikt, dat in vloeibaar glas wordt gekneed. Een dergelijke coating maakt de naad dichter, maar de elektrische geleidbaarheid van de structuur wordt aanzienlijk verminderd. Het algemene lasproces met gecoate elektroden wordt gekenmerkt door hoge spatten, wat ongewenst is voor koper.
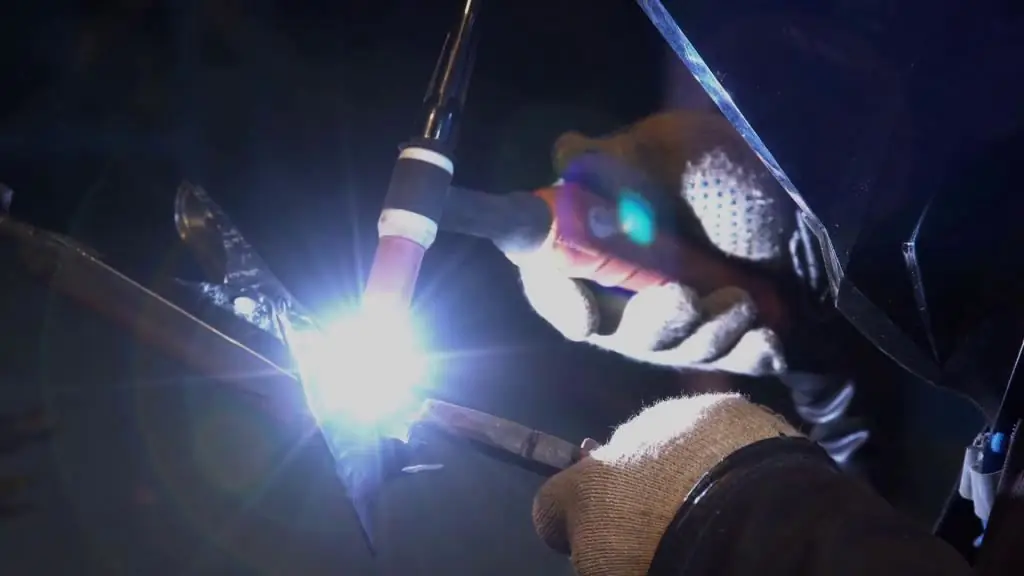
Ondergedompeld booglassen
De flux zelf voor het lassen met koper is nodig als boogstabilisator en, belangrijker nog, als een beschermende barrière tegen de negatieve effecten van atmosferische lucht. Het proces wordt georganiseerd met behulp van niet-verbruikbare grafiet- of koolstofelektroden, evenals met verbruiksstaven onder een keramische flux. Als verbruiksartikelen van koolstof worden gebruikt, worden de elektroden voor het lassen van koper geslepen tot een platte punt in de vorm van een spatel. Een vulmateriaal van tombac of messing wordt ook vanaf de zijkant aan het werkgebied toegevoerd - dit is nodig om de structuur van de naad te deoxideren.
De werking wordt uitgevoerd op gelijkstroom met verwarming. Verschillende beschermingsbarrières behouden de basisstructuur van het werkstuk, hoewel ervaren lassers meestal proberen de samenstelling van het materiaal te verbeteren met gelegeerde draad. Nogmaals, om ongewenste smeltstromen te voorkomen, wordt aanbevolen om in eerste instantie een grafietsubstraat te voorzien,die ook zal fungeren als een vorm voor de flux. De optimale bedrijfstemperatuur voor deze methode is 300-400 °C.
Beschermd booglassen
Laswerkzaamheden met de aansluiting van omvormers en andere halfautomatische apparaten worden uitgevoerd in gasvormige media met draadaanvoer. In dit geval kunnen naast argon en stikstof ook helium en verschillende combinaties van gasmengsels worden gebruikt. De voordelen van deze techniek zijn onder meer de mogelijkheid van effectieve penetratie van dikke werkstukken met een hoge mate van behoud van de mechanische eigenschappen van het werkstuk.
Krachtig thermisch effect wordt verklaard door zeer efficiënte plasmastromen in een brandend gasvormig medium, maar deze parameters zullen ook worden bepaald door de kenmerken van een bepaald invertermodel. Tegelijkertijd heeft de techniek van argon-booglassen van koper meer de voorkeur met betrekking tot werkstukken met een dikte van 1-2 mm. Wat betreft de beschermende functie van het gasvormige medium, daar kan niet volledig op worden vertrouwd. Er blijft het risico van oxiden, porositeit en de negatieve effecten van additieven uit de draad. Aan de andere kant beschermt de argonomgeving het werkstuk effectief tegen blootstelling aan zuurstof in de lucht.
Conclusie
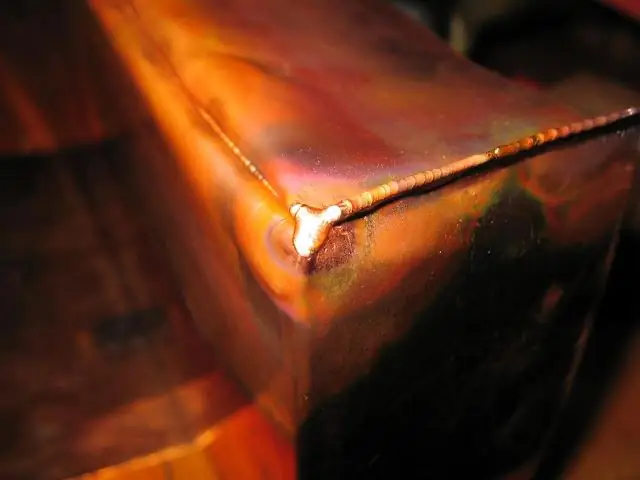
Koper heeft veel kenmerken die het onderscheiden van andere metalen. Maar zelfs binnen de algemene groep van zijn legeringen zijn er veel verschillen, die in elk geval het zoeken naar een individuele benadering voor het kiezen van de optimale technologie voor het vormen van een naad noodzakelijk maken. Gaslassen is bijvoorbeeld geschikt in gevallen waar u een sterke verbinding in een groot werkstuk moet krijgen. Maar nieuwkomersdeze methode wordt niet aanbevolen vanwege de hoge veiligheidseisen voor het werken met branders en gasflessen. Zeer nauwkeurige kleinformaat laswerkzaamheden worden toevertrouwd aan handige en productieve halfautomatische machines. Een onervaren operator kan ook met dergelijke apparatuur omgaan en de parameters van de workflow volledig beheersen. Vergeet het belang van gasvormige media niet. Ze kunnen niet alleen worden gebruikt als isolator van het werkstuk tijdens het lassen, maar ook als een manier om enkele technische en fysieke eigenschappen van het materiaal te verbeteren. Hetzelfde geldt voor elektroden, die een positief legeringseffect kunnen hebben.
Aanbevolen:
Corrosie van aluminium en zijn legeringen. Methoden voor het bestrijden en beschermen van aluminium tegen corrosie
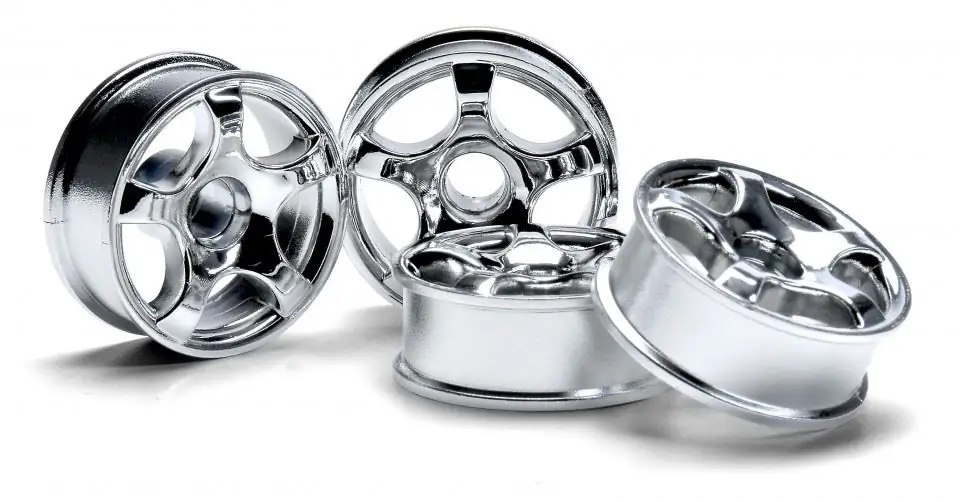
Aluminium is, in tegenstelling tot ijzer en staal, vrij goed bestand tegen corrosie. Dit metaal wordt beschermd tegen roest door een dichte oxidefilm die op het oppervlak wordt gevormd. In het geval van vernietiging van deze laatste neemt de chemische activiteit van aluminium echter sterk toe
Hittebestendige legeringen. Speciale staalsoorten en legeringen. Productie en gebruik van hittebestendige legeringen
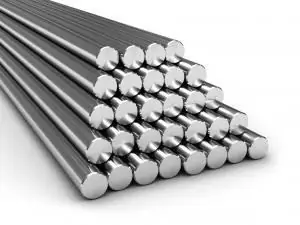
De moderne industrie is niet denkbaar zonder materiaal als staal. We komen het bijna overal tegen. Door verschillende chemische elementen in de samenstelling op te nemen, is het mogelijk om de mechanische en operationele eigenschappen aanzienlijk te verbeteren
Corrosie van koper en zijn legeringen: oorzaken en oplossingen
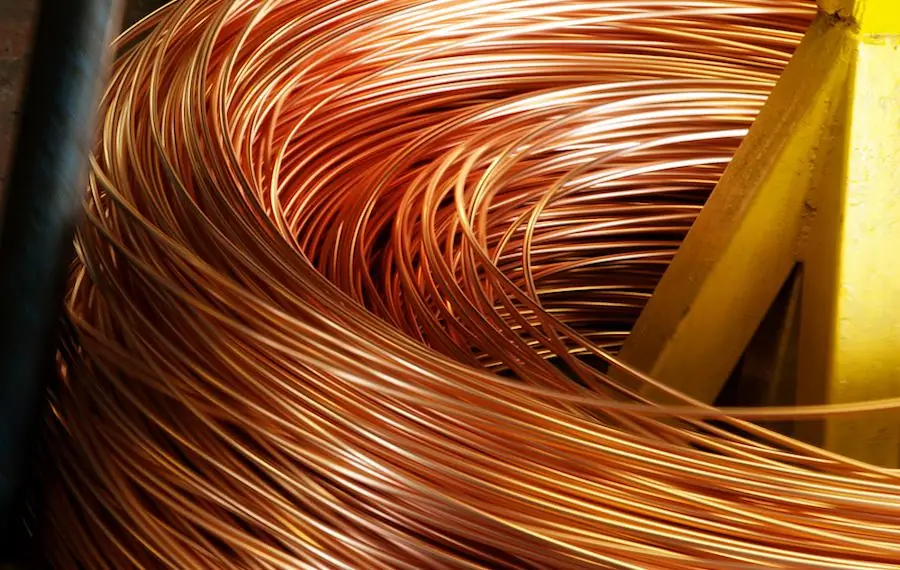
Koper en koperlegeringen hebben een hoge elektrische en thermische geleidbaarheid, kunnen worden bewerkt, hebben een goede corrosieweerstand, dus ze worden actief in veel industrieën gebruikt. Maar wanneer het in een bepaalde omgeving terechtkomt, manifesteert zich nog steeds corrosie van koper en zijn legeringen. Wat is het en hoe producten te beschermen tegen schade, zullen we in dit artikel bespreken
Lassen van ultrasone kunststoffen, kunststoffen, metalen, polymere materialen, aluminium profielen. Ultrasoon lassen: technologie, schadelijke factoren
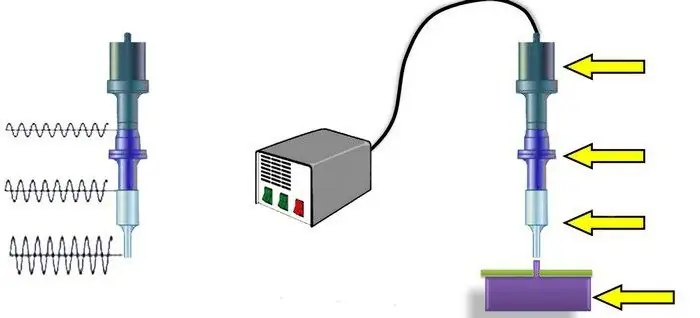
Ultrasoon lassen van metalen is een proces waarbij een permanente verbinding wordt verkregen in de vaste fase. De vorming van juveniele gebieden (waarin banden worden gevormd) en het contact daartussen vindt plaats onder invloed van een speciaal gereedschap
Restauratie van onderdelen door lassen en verharden: methoden en methoden van restauratie, kenmerken, technologisch proces
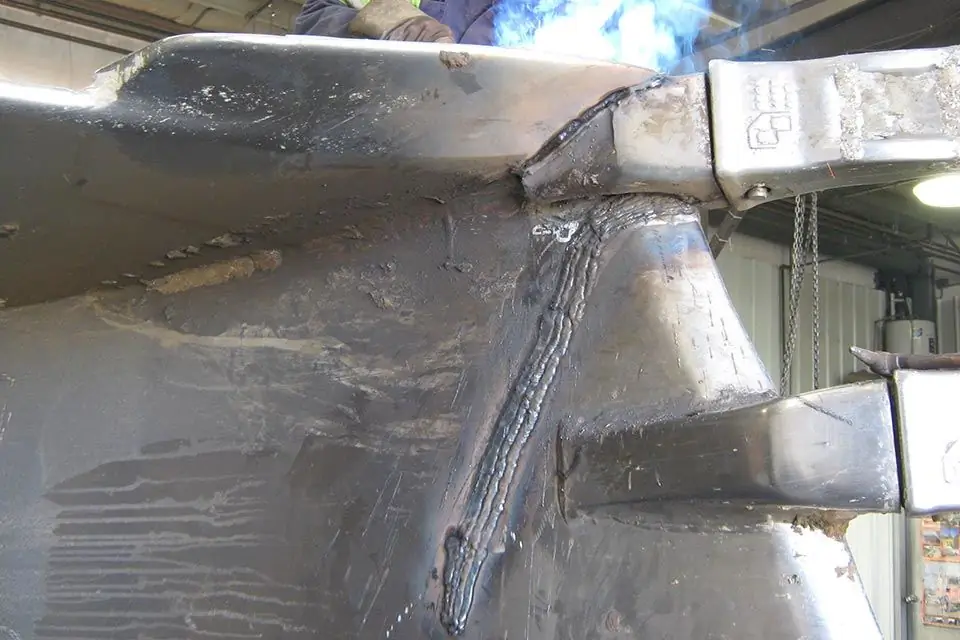
Las- en oppervlaktetechnologieën maken het mogelijk om metalen onderdelen effectief te herstellen, wat zorgt voor een hoge mate van betrouwbaarheid en duurzaamheid van het product. Dit wordt bevestigd door de praktijk om deze methoden te gebruiken bij het uitvoeren van reparatiewerkzaamheden op verschillende gebieden - van autoreparaties tot de productie van gewalst metaal. In de totale hoeveelheid werk aan de reparatie van metalen constructies, duurt het herstel van onderdelen door lassen en verharden ongeveer 60-70%