2025 Auteur: Howard Calhoun | [email protected]. Laatst gewijzigd: 2025-06-01 07:14
De kwaliteit van de las wordt niet alleen bepaald door het vermogen van de meester om de boog correct te organiseren, maar ook door de speciale bescherming van het werkgebied tegen invloeden van buitenaf. De belangrijkste vijand op weg naar het creëren van een sterke en duurzame metalen verbinding is de natuurlijke luchtomgeving. Naadisolatie van zuurstof zorgt voor flux voor het lassen, maar dit is niet alleen zijn taak. Verschillende configuraties van de samenstelling van dit additief met een combinatie van een beschermende gasomgeving stellen u in staat om de parameters van de naadverbinding op verschillende manieren te regelen.
Flux opdracht
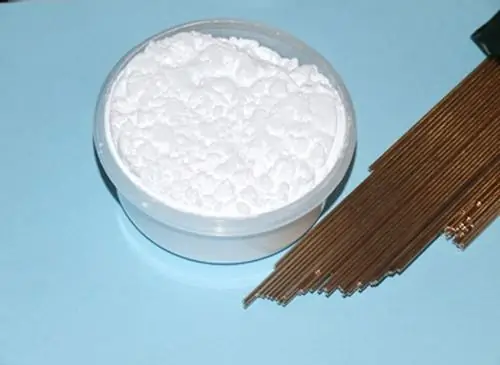
Het lastoevoegmateriaal van dit type wordt naar de verbrandingszone gestuurd en heeft, afhankelijk van de kenmerken van de smelt, een beschermend en wijzigend effect op het lasvormingsgebied. In het bijzonder kan het materiaal de volgende functies vervullen:
- Creëren van slak- en gasisolatie voor het smeltbad.
- Een lasverbinding gevenbepaalde technische en fysieke eigenschappen.
- Boogstabiliteit behouden.
- Overdracht van elektrodemetaal (of draadsmelt) naar de laszone.
- Verwijderen van ongewenste onzuiverheden in de slaklaag.
Als we het hebben over de compatibiliteit van verschillende fluxen voor het lassen met metalen, dan hebben de meest voorkomende merken de volgende doelen:
- FC-9 - koolstoflegeringen van laaggelegeerd staal.
- AN-18 - legeringen van hooggelegeerd staal.
- AN-47 - laag- en middelgelegeerd staal, gekenmerkt door hoge sterkte-eigenschappen.
- AN-60 - laaggelegeerde staalsoorten gebruikt in pijpleidingen.
- ФЦ-7 - gebruikt bij het lassen van zacht staal met hoge stroomsterkte.
- FC-17 - ijzer met een hoge temperatuur in het midden.
- FC-19 - legeringen met een hoog chroomgeh alte.
- ФЦ-22 - wordt gebruikt om een hoeknaadverbinding te maken in het werk met gelegeerd koolstofstaal.
- 48-OF-6 - wordt gebruikt in lastechnieken met de verbinding van hooggelegeerde elektrodedraad.
Flux composities
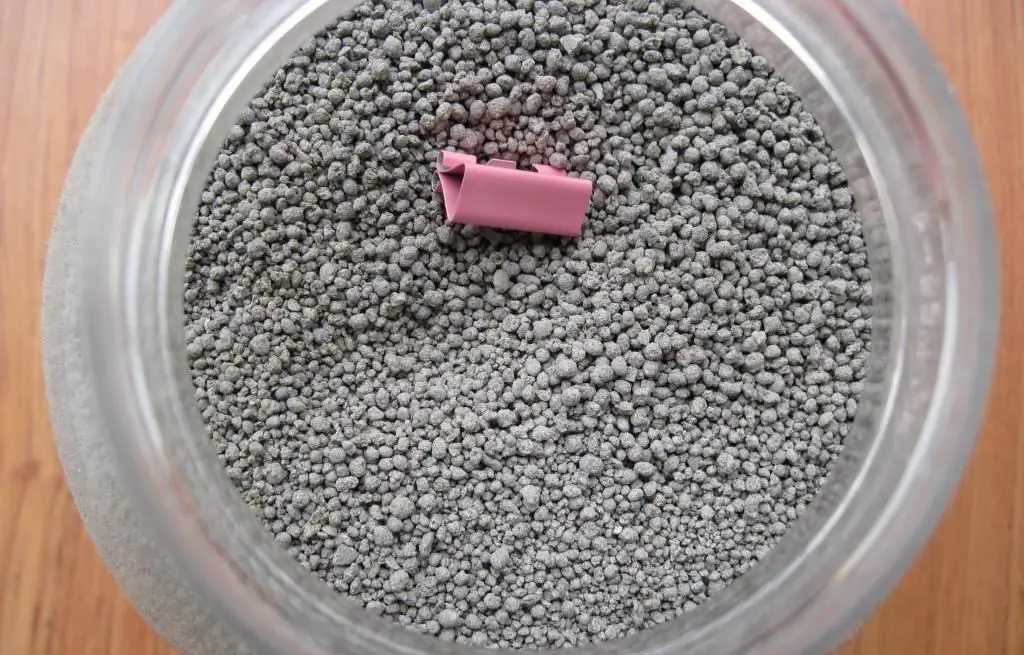
De flux zelf wordt in de regel geproduceerd in de vorm van een korrelig poeder met een fractie in de orde van grootte van 0,2-4 mm. Maar de inhoud en herkomst van dit product kan heel verschillend en niet altijd uniform zijn. In dit opzicht worden de volgende soorten flux voor het lassen onderscheiden:
- Oxide. Het grootste deel van de inhoud is metaaloxiden en ongeveer 10%is verantwoordelijk voor het aandeel fluoride-elementen. Dit vloeimiddel wordt gebruikt om te werken met laaggelegeerde en fluorstaallegeringen. Ook worden, afhankelijk van de inhoud, oxidefluxsamenstellingen onderverdeeld in siliciumvrij, laag-silicium en hoog-silicium.
- Zoutoxide. Dergelijke poeders worden ook wel gemengd genoemd, omdat de vulling gelijk kan worden gevormd door oxiden en zoutverbindingen. Dit vloeimiddel wordt gebruikt om gelegeerd staal te verwerken.
- Zout. De aanwezigheid van oxiden is volledig uitgesloten en fluoriden en chloriden vormen de basis van de samenstelling. Het doel van zoutflux is het hersmelten van elektroslakken en het lassen van actieve metalen.
Flux technologie
Tijdens het productieproces ondergaat de fluxbasis (batch) verschillende verwerkingsprocedures, waaronder smelten, granuleren, vormen en kwaliteitscontrole. De grondstof van de lading vóór het productieproces is gesegmenteerd in klein, middelgroot en groot. Elke batch wordt grondig gewassen en gedroogd, omdat de zuiverheid en nauwkeurigheid in de parameters van de toekomstige flux vanaf het begin worden gehandhaafd. Vervolgens wordt gewogen, gedoseerd en gemengd met andere technologische componenten. Het smelten en granuleren van flux voor het lassen wordt uitgevoerd op speciale apparatuur - er worden gasvlam- of vlamboogovens, zwembaden voor het gieten van koud water en metalen pallets gebruikt. In de laatste stadia van de verwerking wordt drogen met zeven uitgevoerd. Flux dat de inspectie heeft doorstaan, wordt verpakt in speciale zakken of dozen met vuurvaste eigenschappen.
GOST-vereisten voor flux
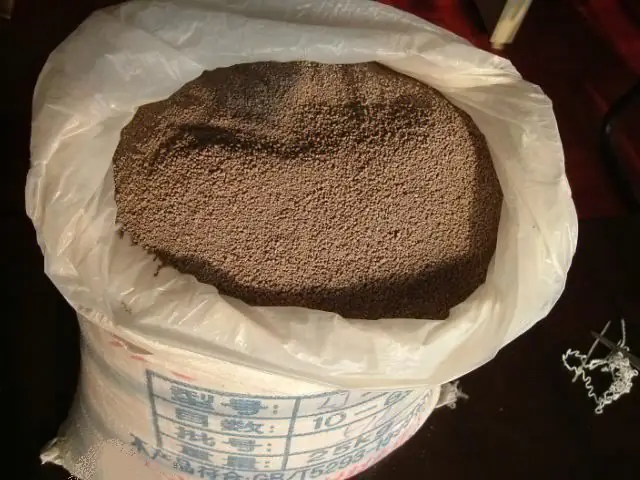
Regelgevende vereisten zijn van invloed op verschillende gebieden van de beoordeling van de fluxkwaliteit, evenals de veiligheidsregels voor het omgaan met het materiaal en de methoden om het te testen. Wat betreft de belangrijkste parameters, worden de volgende eisen gesteld:
- Uitgesloten in fluxpoederkorrels groter dan 1,6 mm. Het percentage van hun inhoud mag niet meer zijn dan 3% van de totale massa.
- Het is toegestaan om een vloeimiddel te produceren met een fractie van maximaal 0,25 mm, als deze voorwaarde in eerste instantie is overeengekomen met de consument.
- In overleg met de consument is het ook toegestaan om materiaal te vervaardigen met een korrelfractie van 0,35 tot 2,8 mm, maar alleen met betrekking tot de AN-348-A-klasse.
- Het vochtgeh alte van vloeimiddelen mag, afhankelijk van het merk, een coëfficiënt van 0,05 tot 0,1% niet overschrijden.
Wat de veiligheidseisen betreft, zijn persoonlijke beschermingsmaatregelen het belangrijkste onderwerp van de GOST-regelgeving. Ondergedompeld booglassen moet worden uitgevoerd in overeenstemming met brandveiligheidsmaatregelen. Afzonderlijk moet de concentratie van het gebruikte vloeimiddel, dat standaard als chemisch gevaarlijk en schadelijk voor de productie wordt beschouwd, worden gecontroleerd.
Gesmolten en niet-gesmolten flux
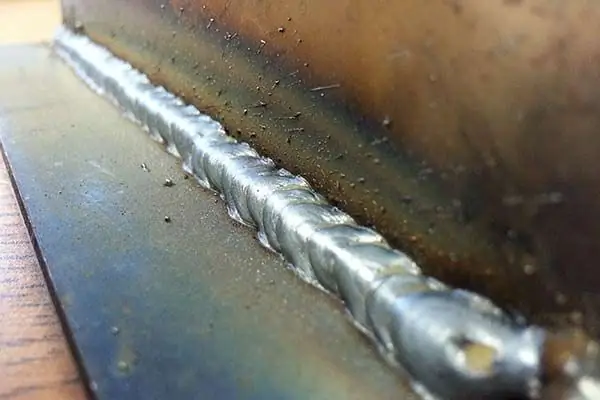
Het geh alte aan gesmolten poeder wordt voornamelijk gevormd door slakvormende componenten. Ze worden geproduceerd als resultaat van de fusie van samenstellende elementen, waaronder kwartszand, mangaanerts en krijt. Door ze in bepaalde verhoudingen te mengen, gevolgd door te smelten in ovens, is het mogelijk om:krijg een modifier voor een naad met een bepaalde reeks kenmerken. Meer functioneel is ondergedompeld booglassen dat op een niet-gesmolten manier wordt geproduceerd. Dit is een mengsel van korrel- en poedermaterialen, die naast de slakvormende basis ook legeringselementen en desoxidatiemiddelen bevatten. De afwezigheid van een smeltbewerking maakt het mogelijk om metaalstof en ijzerlegeringen in het vloeimiddel te brengen, wat de mogelijkheden voor het verbeteren van verbindingen zal ontcijferen.
Soorten ondergedompeld booglassen
Met het gebruik van flux kan zowel handmatig als automatisch worden gelast - het fundamentele verschil hangt af van de geselecteerde apparatuur. Booglassen wordt uitgevoerd in zelfinstellende modus of ondersteund door automatische spanningsregeling. Het is optimaal om inverterinstallaties te gebruiken, aangevuld met draadaanvoertrommels. Lassen met flux zonder gas is ook gebruikelijk, dat standaard fungeert als een beschermende omgeving tegen zuurstof en stikstof. Wat is de goede techniek die deze barrière voor negatieve impactfactoren uitsluit? Ten eerste, als een geschikte flux wordt geselecteerd, zal deze in staat zijn om de volledige lijst van beschermende en ondersteunende taken met betrekking tot de gevormde naad uit te voeren. Ten tweede vergemakkelijkt de afwezigheid van een gasvormig medium de organisatie van het proces zelf. Het is niet nodig om een cilinder met een mengsel van argon en kooldioxide voor te bereiden en ook het lasgebied te beschermen tegen overmatige thermische blootstelling bij gebruik van een toorts.
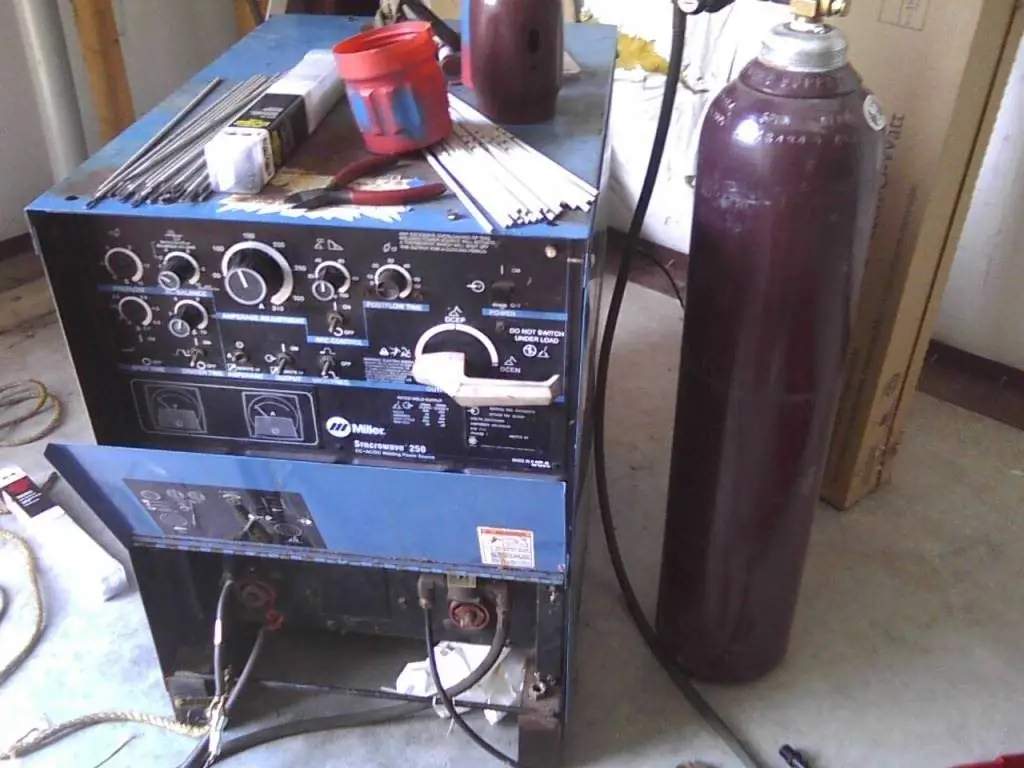
Flux techniek
Na het ontsteken van de boog, moet de operator deze onderhoudentussen het uiteinde van de elektrode en het werkstuk onder de fluxlaag. Het poeder wordt in een laag van 55-60 mm gegoten, waarna de boog letterlijk in deze massa moet worden verdronken totdat deze smelt. Bij een gemiddeld fluxgewicht kan de statische druk op het metaal ongeveer 8-9 g/cm2 zijn. Deze waarde is voldoende om ongewenste mechanische effecten op het smeltbad te elimineren. Bij gebruik van een draad voor het lassen met flux is het mogelijk om minimale smeltspatten te bereiken. Aan deze voorwaarde wordt voldaan door te zorgen voor een stabiel contact van de smeltzone met de verbruiksdraad en het vloeimiddel, evenals door de stroomsterkte te regelen. Bescherming van de gaszijde is in dit geval ook niet vereist, maar vooral de vermogensregeling zal belangrijk zijn. In de regel wordt een combinatie van draad en flux gebruikt bij het lassen met een hoge stroomdichtheid, daarom moet de machine worden gekozen rekening houdend met het handhaven van een constante snelheid van geleiding van de elektrodedraad.
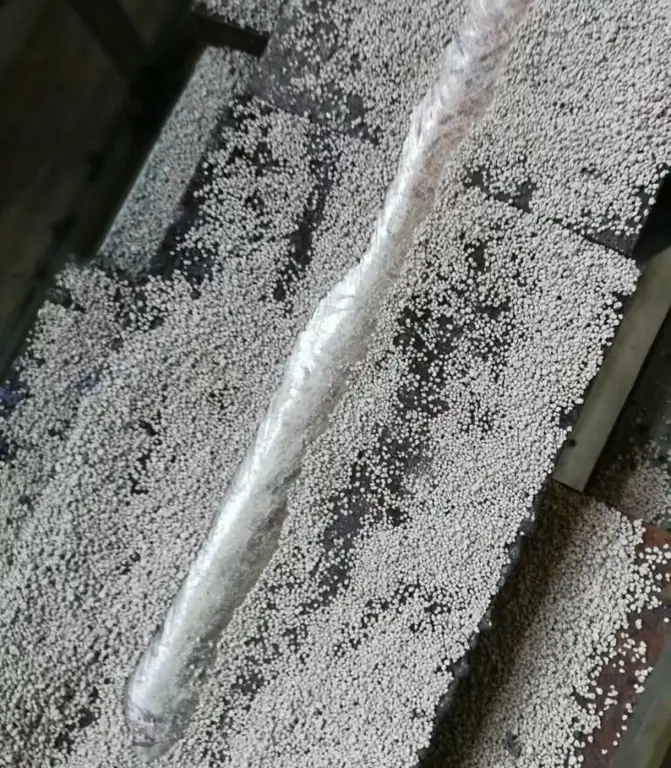
Voordelen van het gebruik van flux
Het gebruik van flux heeft zeker invloed op de vorming van de naad op de beste manier, omdat de negatieve factoren van het werkproces in open lucht worden geminimaliseerd. De voor de hand liggende voordelen zijn onder meer minder defecten in het verbindingsgebied, minimalisering van spatten en efficiëntere boogregeling met volledig automatische controlemogelijkheden. Wat ook erg belangrijk is, is dat het gebied van het booglassen onder water altijd zichtbaar is voor de operator. Dit maakt het mogelijk om, indien nodig, tijdig bij te sturen in het proces, en in sommige gevallen zelfs zonder specialemaskers.
Nadelen van het gebruik van flux
Zwakke punten van deze technologie worden veroorzaakt door hogere eisen aan apparatuur, omdat er meer vermogen nodig is om de flux effectief te smelten. Tegenwoordig worden speciale aanpassingen van apparaten voor argonbooglassen in een fluxomgeving geproduceerd, die speciale apparatuur hebben voor de voorbereiding en levering. Het is logisch dat dergelijke modellen 15-20% meer kosten. Een ander nadeel hangt samen met een toename van de smeltzone. Hoewel het binnen bepaalde grenzen kan worden gecontroleerd, is het problematisch om kleine elementen onder dergelijke omstandigheden te verwerken.
Conclusie
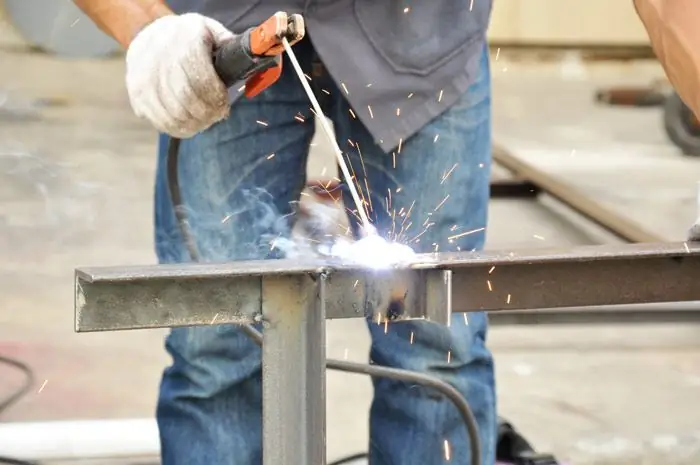
Flux als verbruiksartikel dat de kwaliteit van het lasproces verbetert, vergemakkelijkt veel productie- en constructieactiviteiten van dit spectrum. Maar zelfs thuis wordt het vaak gebruikt in het land, in de garage of gewoon bij reparatiewerkzaamheden. Bij het kiezen van dit materiaal voor uw eigen behoeften, is het erg belangrijk om de kwaliteitsbeoordeling niet verkeerd te berekenen. Zoals opgemerkt door dezelfde GOST, moet vloeimiddel voor lassen op de markt worden geleverd in dikke papieren zakken van 20 tot 50 kg, met vermelding van transportmarkeringen. Op speciale bestelling kunnen ook kleinverpakkingen worden gemaakt, maar hiervoor moeten speciale containers worden voorzien. Bovendien moet het wegen worden uitgevoerd met een maximale fout van 1% ten opzichte van het totale tarragewicht.
Aanbevolen:
Indicatoren zonder vertraging en hertekening: soorten, werkingsprincipe, voor- en nadelen van toepassing, deskundig advies
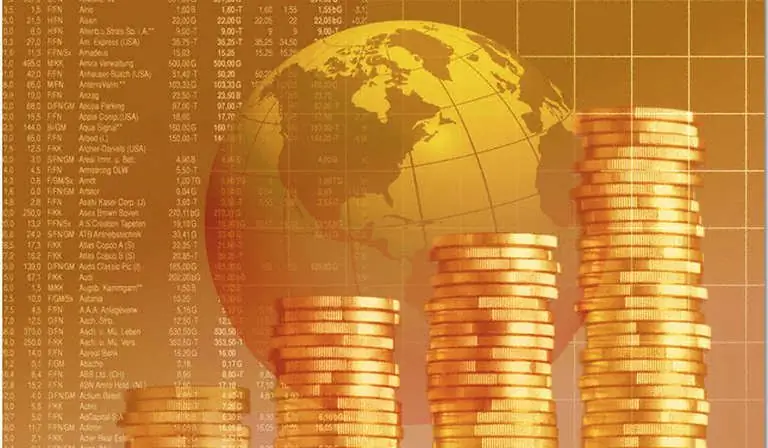
Er is een grote verscheidenheid aan verschillende tools in de handel: grafische constructies, technische indicatoren, geautomatiseerde programma's, handelssignalen en nog veel meer. Om ze met succes toe te passen in de handel, moet u begrijpen hoe ze werken. Indicatoren zonder vertraging en opnieuw tekenen zijn vooral populair bij handelaren
Koreaanse incubators: soorten, gebruiksregels

Het duurt iets meer dan 20 dagen en een broedmachine om kuikens uit bevruchte eieren uit te broeden. Voor werkgemak en voor een grotere garantie is het beter om moderne apparatuur te gebruiken. Automatische Koreaanse incubators zijn heel goed in staat om deze taak uit te voeren
Verbindingen: doel, soorten verbindingen. Voorbeelden, voordelen, nadelen van soorten verbindingen
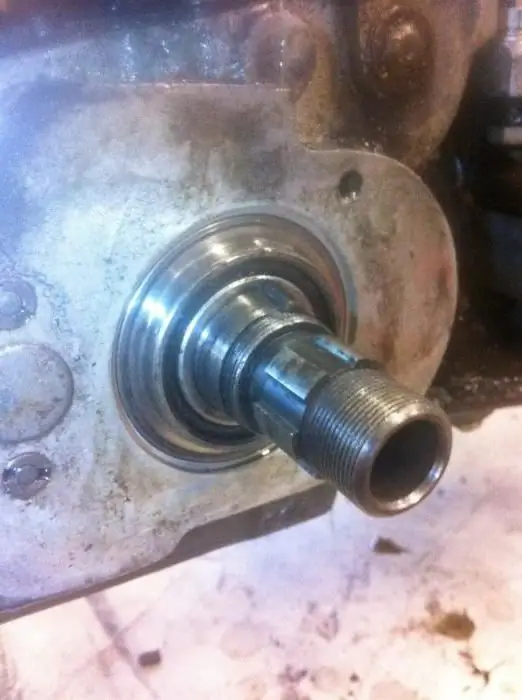
Machines en werktuigmachines, apparatuur en huishoudelijke apparaten - al deze mechanismen hebben veel details in hun ontwerp. Hun hoogwaardige verbinding is een garantie voor betrouwbaarheid en veiligheid tijdens het werk. Welke soorten verbindingen zijn er? Laten we hun kenmerken, voor- en nadelen eens nader bekijken
Minerale woldichtheid: classificatie, voor- en nadelen, doel van minerale wol en toepassing
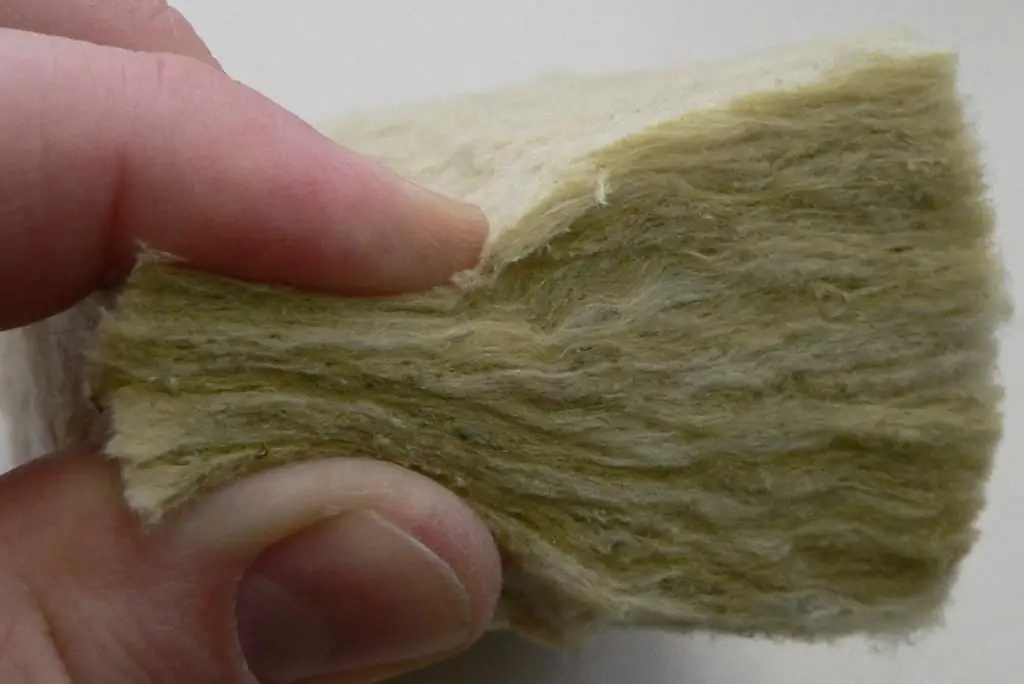
Minerale wol is het meest populaire type isolatie voor een appartement of huis. Tegenwoordig wordt het door iedereen gebruikt, van bouwers tot de eigenaar van het appartement, die de kamer wilden isoleren. Door de eenvoud van de installatie kunt u onmiddellijk het hele huis (plafond, muren, vloer) isoleren. We zullen de kenmerken en kenmerken van het genoemde materiaal verder in het artikel bestuderen
Verdeelrooster voor bijen: doel, beschrijving, gebruiksregels, afmetingen
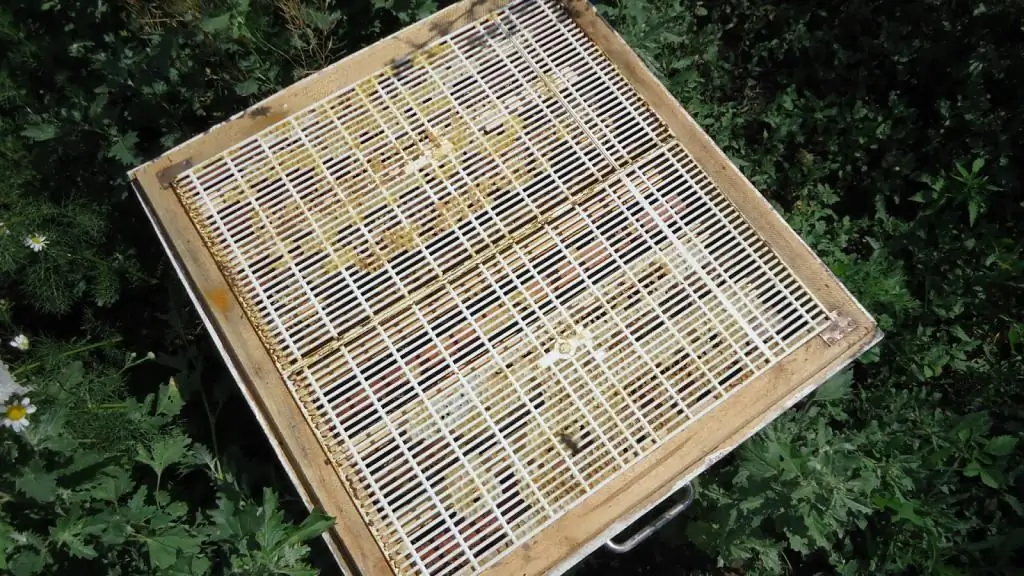
Waarschijnlijk heeft iedereen die al meer dan een jaar bijenteelt heeft gehoord van een dergelijk apparaat als een scheidingsrooster voor bijen. Het biedt veel belangrijke voordelen bij correct gebruik. Daarom zou elke beginner die net zo'n moeilijke maar opwindende activiteit als de bijenteelt begint onder de knie te krijgen, erover moeten leren